PVD (Physical Vapor Deposition) coatings on watches are known for their durability and longevity, often lasting anywhere from 10 years to several decades, depending on various factors. These coatings are highly resistant to corrosion, oxidation, and scratching due to their thin, hard, and tightly bonded nature. The vacuum environment during the PVD process ensures a contamination-free application, enhancing the coating's durability. While PVD coatings are generally long-lasting, their lifespan can be influenced by the substrate material, coating thickness, and the conditions under which the watch is used. Overall, PVD coatings are considered one of the most durable finishes available for watches.
Key Points Explained:
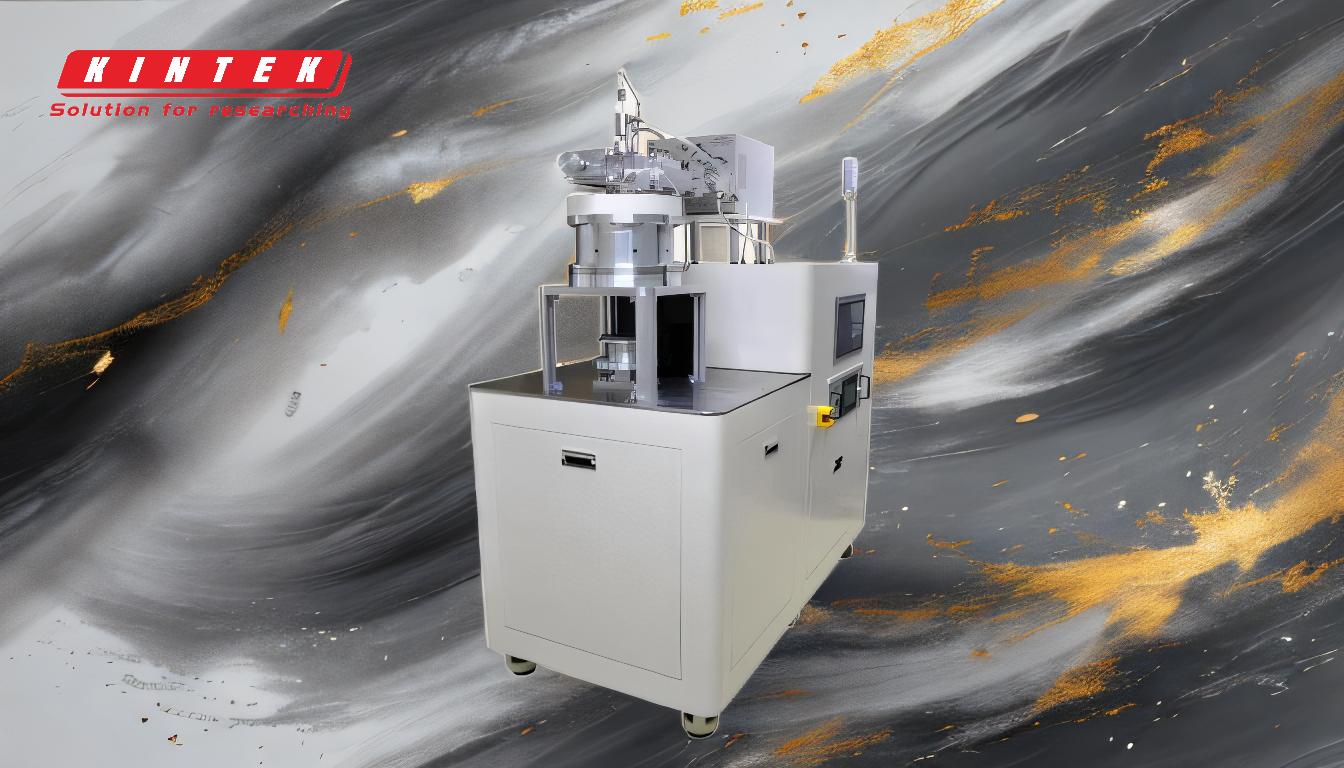
-
Durability and Longevity of PVD Coatings:
- PVD coatings are known for their exceptional durability, often lasting between 10 years to hundreds of years, depending on factors like substrate material, coating thickness, and application conditions.
- The coatings are highly resistant to corrosion, oxidation, and scratching, making them ideal for long-term use in watches.
-
Thickness and Bonding:
- PVD coatings are very thin, ranging from 0.5 to 5 microns, which makes them difficult to remove and ensures they replicate the original finish of materials with minimal effort.
- The vacuum environment during the PVD process eliminates contamination and forms a strong bond with the substrate, enhancing the coating's durability and resistance to wear.
-
Hardness and Wear Resistance:
- PVD coatings are harder and more wear-resistant compared to other types of coatings. This hardness contributes significantly to their longevity and ability to withstand daily wear and tear.
- The coatings also exhibit low friction properties, which further reduce wear over time.
-
Resistance to Environmental Factors:
- The vacuum environment used in the PVD process prevents oxidation and degradation caused by oxygen and moisture, making the coatings highly resistant to environmental factors.
- This resistance to corrosion and scratching ensures that the watch maintains its appearance and functionality over extended periods.
-
Substrate Material Influence:
- The properties of PVD coatings are influenced by the underlying substrate material. For example, coatings like TiN (Titanium Nitride) can increase the fatigue limit and endurance of certain alloys, enhancing the overall durability of the watch.
- The hardness of the coating, determined by the substrate material, plays a crucial role in its durability.
-
Applications and Suitability:
- PVD coatings are used in various demanding industries, including automotive, aerospace, and medical, due to their robust temperature tolerance, impact strength, and excellent abrasion and corrosion resistance.
- These properties make PVD coatings particularly suitable for watches, which are often subjected to harsh conditions and require long-lasting finishes.
-
Comparison with Traditional Finishes:
- PVD coatings are considered superior to traditional finishes in terms of durability and quality. They are often described as the most durable coating available today, capable of outlasting any traditional finish.
- This makes PVD-coated watches a preferred choice for consumers seeking long-lasting and high-quality timepieces.
In summary, PVD coatings on watches are highly durable and long-lasting, thanks to their hardness, wear resistance, and resistance to environmental factors. The vacuum application process ensures a strong bond with the substrate, further enhancing their durability. While the exact lifespan can vary based on factors like substrate material and usage conditions, PVD coatings are generally considered one of the most durable finishes available for watches.
Summary Table:
Key Feature | Details |
---|---|
Durability | Lasts 10 years to several decades, depending on usage and material factors. |
Resistance | Highly resistant to corrosion, oxidation, and scratching. |
Thickness | 0.5 to 5 microns, ensuring a strong bond and minimal wear. |
Hardness | Harder and more wear-resistant than traditional finishes. |
Environmental Resistance | Resists oxidation and degradation caused by oxygen and moisture. |
Applications | Used in automotive, aerospace, and medical industries for durability. |
Interested in PVD-coated watches? Contact us today to learn more about their durability and benefits!