PVD (Physical Vapor Deposition) coatings are renowned for their durability and resistance to wear, but like any material, they are not entirely immune to degradation over time. The longevity of a PVD coating depends on several factors, including the type of coating, the substrate material, the application environment, and the thickness of the coating. While PVD coatings are designed to be highly durable, they can wear off under extreme conditions or prolonged exposure to harsh environments. The coating process itself is relatively quick, typically taking about half an hour to an hour for each coating, though larger pieces may require up to 2 hours.
Key Points Explained:
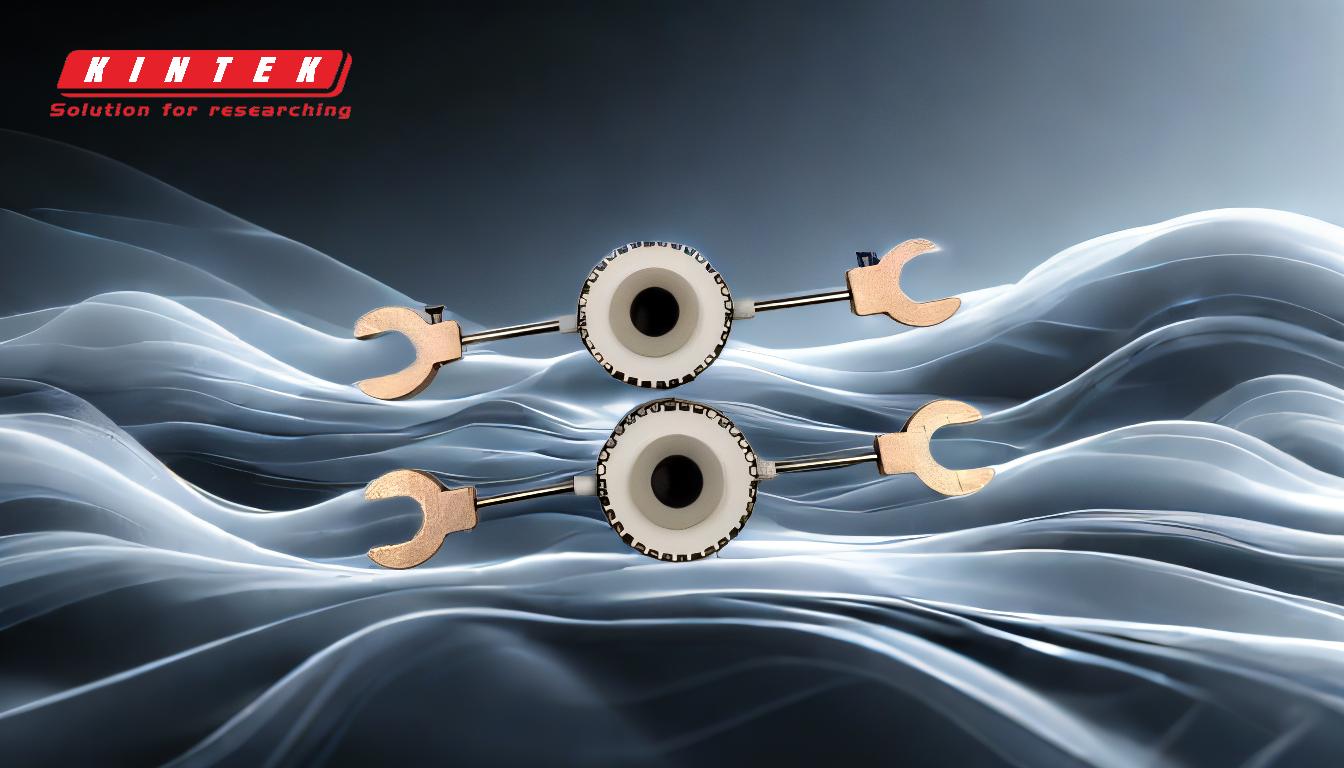
-
Durability of PVD Coatings:
- PVD coatings are known for their exceptional hardness and resistance to wear, making them suitable for a wide range of applications, including cutting tools, medical devices, and decorative finishes.
- The coatings are typically composed of materials like titanium nitride (TiN), chromium nitride (CrN), or diamond-like carbon (DLC), which are chosen for their hardness and resistance to corrosion.
-
Factors Influencing Wear:
- Type of Coating: Different PVD coatings have varying levels of hardness and wear resistance. For example, DLC coatings are known for their exceptional hardness and low friction, making them more resistant to wear than some other types of PVD coatings.
- Substrate Material: The material being coated also plays a role in how well the PVD coating adheres and resists wear. A well-prepared substrate with proper surface treatment will enhance the coating's durability.
- Application Environment: The conditions under which the coated part is used can significantly impact the longevity of the PVD coating. High temperatures, abrasive materials, or corrosive environments can accelerate wear.
- Coating Thickness: Thicker coatings generally offer better wear resistance, but they may also be more prone to cracking or delamination under certain conditions.
-
Wear Mechanisms:
- Abrasive Wear: This occurs when hard particles or surfaces rub against the coating, gradually wearing it down. PVD coatings are designed to resist this type of wear, but over time, even the hardest coatings can be affected.
- Adhesive Wear: This type of wear happens when two surfaces in contact transfer material between them, leading to gradual loss of the coating. PVD coatings are less prone to adhesive wear due to their hardness and low friction properties.
- Corrosive Wear: In environments where the coating is exposed to corrosive substances, the coating may degrade over time. PVD coatings generally have good corrosion resistance, but prolonged exposure to harsh chemicals can still cause wear.
-
Maintenance and Care:
- To maximize the lifespan of a PVD coating, proper maintenance is essential. This includes regular cleaning to remove abrasive particles and avoiding exposure to extreme conditions that could accelerate wear.
- In some cases, reapplication of the PVD coating may be necessary after extended use, especially in high-wear applications.
-
Conclusion:
- While PVD coatings are highly durable and resistant to wear, they are not completely immune to degradation. The rate at which a PVD coating wears off depends on various factors, including the type of coating, the substrate material, and the application environment. With proper care and maintenance, the lifespan of a PVD coating can be significantly extended, but in high-wear or harsh environments, some degree of wear over time is inevitable.
Summary Table:
Factor | Impact on PVD Coating Wear |
---|---|
Type of Coating | Different coatings (e.g., TiN, CrN, DLC) vary in hardness and wear resistance. |
Substrate Material | Proper surface preparation enhances adhesion and durability. |
Application Environment | Harsh conditions (high temps, abrasives, corrosive substances) accelerate wear. |
Coating Thickness | Thicker coatings resist wear better but may crack or delaminate under stress. |
Wear Mechanisms | Abrasive, adhesive, and corrosive wear can degrade PVD coatings over time. |
Maintenance | Regular cleaning and avoiding extreme conditions can extend coating lifespan. |
Want to maximize the lifespan of your PVD coatings? Contact our experts today for tailored solutions!