Sintering is a critical process in materials science that significantly impacts the strength and durability of materials. By heating powdered materials below their melting point, sintering causes particles to bond and densify, reducing porosity and creating a more cohesive structure. This process enhances mechanical properties such as strength, hardness, and wear resistance. The controlled heating and diffusion mechanisms during sintering lead to a dense microstructure with optimized grain size, pore size, and grain boundary distribution, which collectively contribute to improved material performance.
Key Points Explained:
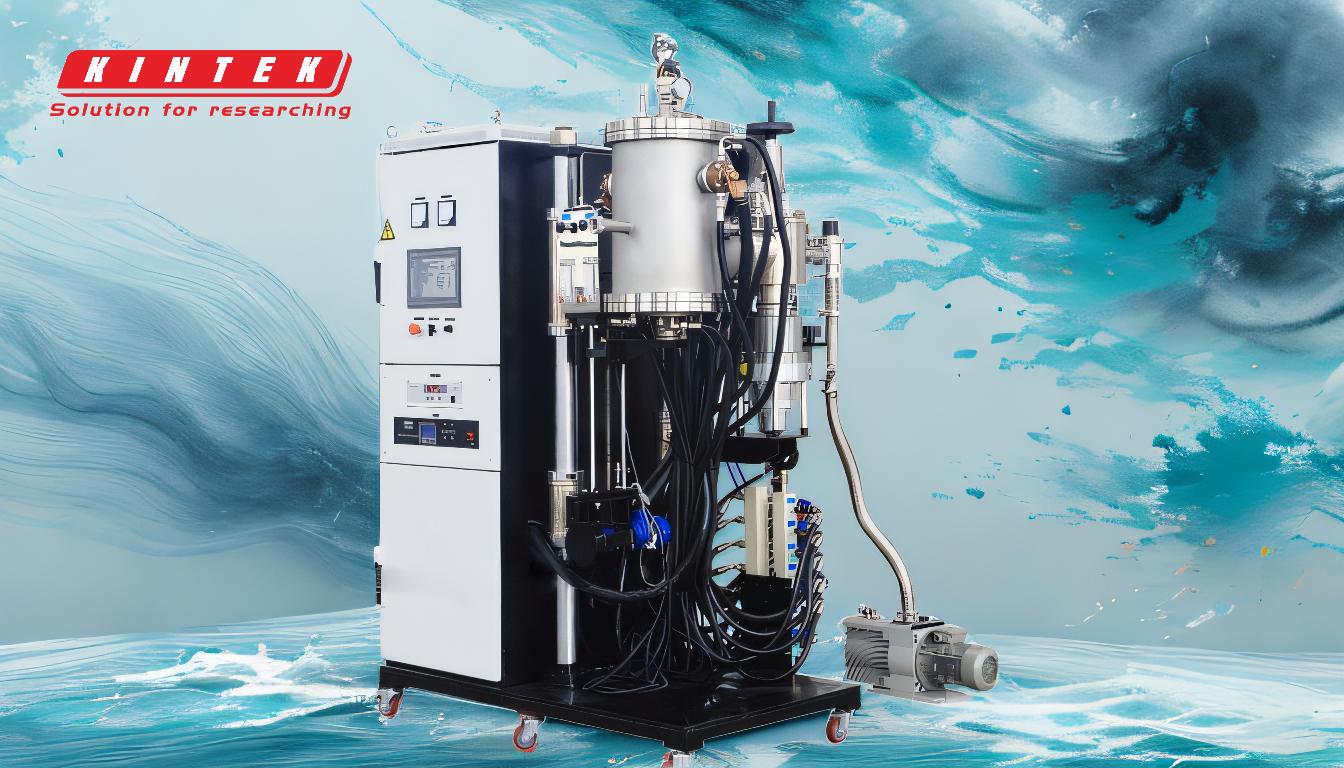
-
Sintering Reduces Porosity
- Sintering minimizes the porosity of a material's surface by bonding particles together.
- Reduced porosity directly enhances the material's strength and durability, as fewer voids and defects weaken the structure.
- This is particularly important for materials like ceramics and metals, where porosity can compromise mechanical integrity.
-
Enhanced Grain Structure and Microstructure
- Sintering influences grain size, pore size, and grain boundary distribution in the material's microstructure.
- A finer and more uniform grain structure improves mechanical properties, as smaller grains and well-distributed grain boundaries resist deformation and cracking.
- The controlled diffusion of atoms during sintering ensures a dense and cohesive structure, which is essential for high-strength applications.
-
Improved Mechanical Properties
- Sintering leads to improved strength, hardness, and wear resistance in materials.
- The bonding and densification of particles during sintering create a robust internal structure capable of withstanding stress and strain.
- These enhanced properties make sintered materials suitable for demanding applications, such as automotive components, cutting tools, and aerospace parts.
-
Energy Efficiency and Environmental Benefits
- Sintering requires less energy compared to melting the same material, making it an environmentally friendly manufacturing option.
- The lower energy consumption also reduces production costs, making sintering a cost-effective method for producing high-strength materials.
-
Consistency and Control in Manufacturing
- Sintering allows for greater control over the manufacturing process, resulting in more consistent and reliable products.
- The ability to precisely control temperature and heating rates ensures uniform densification and microstructure development, which is critical for achieving desired material properties.
-
Application-Specific Benefits
- Sintering is essential for creating fully dense parts that exhibit the desired material properties, such as strength and durability, expected from ceramics or metals.
- The process is widely used in industries requiring high-performance materials, including electronics, medical devices, and construction.
In summary, sintering is a transformative process that enhances material strength by reducing porosity, optimizing microstructure, and improving mechanical properties. Its energy efficiency, consistency, and ability to produce dense, high-performance components make it a vital technique in modern manufacturing.
Summary Table:
Key Benefit | Description |
---|---|
Reduced Porosity | Minimizes voids and defects, enhancing strength and durability. |
Enhanced Microstructure | Optimizes grain size, pore size, and grain boundary distribution for better performance. |
Improved Mechanical Properties | Increases strength, hardness, and wear resistance for demanding applications. |
Energy Efficiency | Requires less energy than melting, reducing costs and environmental impact. |
Manufacturing Consistency | Ensures uniform densification and reliable material properties. |
Wide Applications | Used in automotive, aerospace, electronics, and medical industries. |
Ready to enhance your materials with sintering? Contact our experts today to learn more!