The temperature during deposition processes can either increase or decrease depending on the specific method and materials involved. Generally, deposition techniques like chemical vapor deposition (CVD) or physical vapor deposition (PVD) often require elevated temperatures to facilitate the reaction or evaporation of materials. Conversely, some deposition methods, such as certain types of sputtering or cold spray techniques, may operate at lower temperatures to prevent damage to the substrate or to maintain specific material properties. The temperature control is crucial as it directly impacts the quality, adhesion, and properties of the deposited layer.
Key Points Explained:
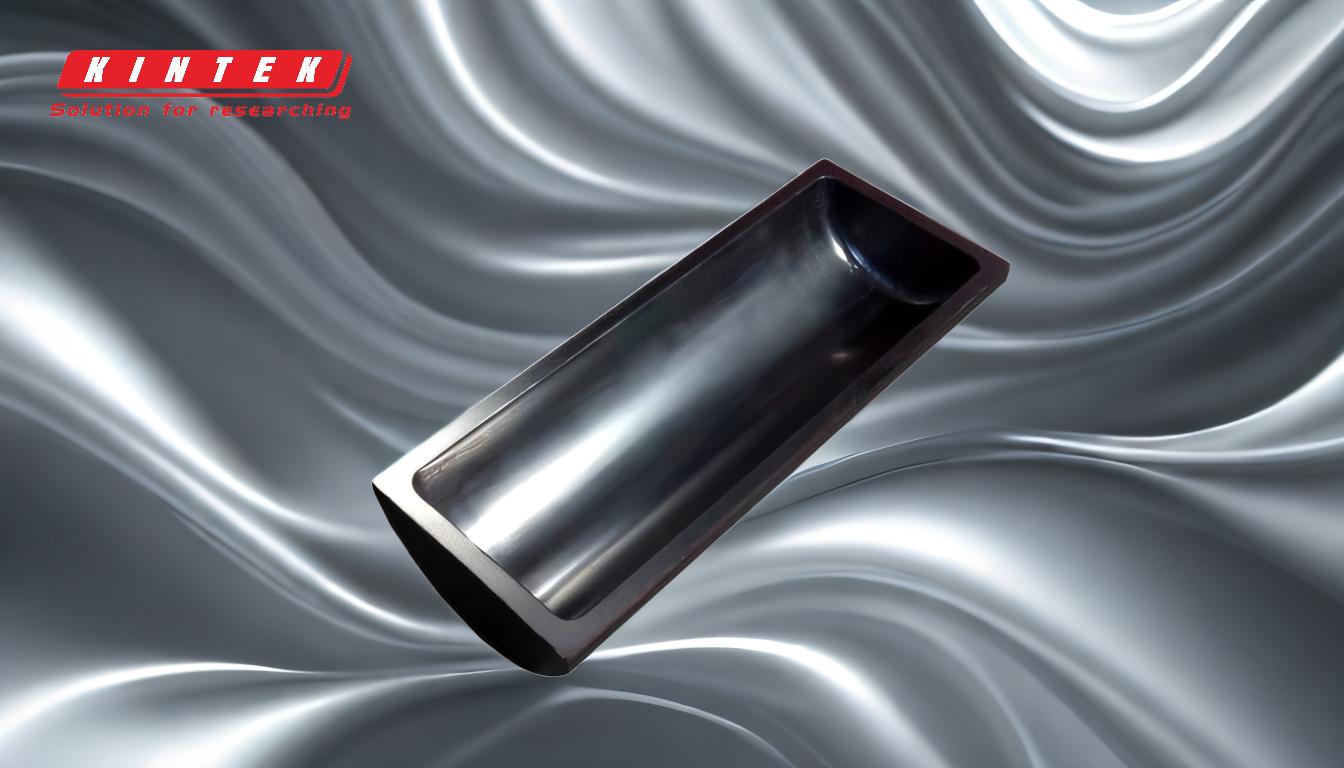
-
Types of Deposition Processes:
- Chemical Vapor Deposition (CVD): Typically requires high temperatures to decompose gaseous precursors and form a solid deposit on the substrate. The temperature can range from 500°C to 1200°C depending on the material and desired film properties.
- Physical Vapor Deposition (PVD): Involves processes like sputtering or evaporation, which can operate at lower temperatures compared to CVD. However, some PVD methods may still require moderate heating to improve film adhesion and quality.
- Electrochemical Deposition: Often occurs at ambient or slightly elevated temperatures, making it suitable for temperature-sensitive substrates.
-
Temperature Influence on Deposition:
- High-Temperature Deposition: Enhances the mobility of atoms on the substrate surface, leading to better film quality and adhesion. However, it may not be suitable for substrates that cannot withstand high temperatures.
- Low-Temperature Deposition: Preserves the integrity of temperature-sensitive substrates and can be used to deposit materials that degrade at high temperatures. Techniques like cold spray or low-temperature CVD are examples.
-
Material Considerations:
- Substrate Material: The choice of substrate material can dictate the deposition temperature. For instance, polymers or certain metals may degrade or warp at high temperatures, necessitating low-temperature deposition methods.
- Deposited Material: Different materials have varying temperature requirements for optimal deposition. For example, silicon dioxide deposition via CVD typically requires higher temperatures compared to metal deposition via sputtering.
-
Process Control and Optimization:
- Temperature Uniformity: Ensuring a uniform temperature across the substrate is crucial for consistent film properties. Non-uniform temperatures can lead to defects like cracking or poor adhesion.
- Cooling Systems: In high-temperature deposition processes, cooling systems are often employed to manage the heat and prevent damage to the equipment or substrate.
-
Applications and Implications:
- Semiconductor Manufacturing: High-temperature deposition is commonly used in semiconductor manufacturing to create high-quality, defect-free films.
- Flexible Electronics: Low-temperature deposition techniques are essential for flexible electronics, where substrates like plastics cannot withstand high temperatures.
Understanding the temperature dynamics in deposition processes is essential for selecting the appropriate method and achieving the desired material properties. The choice between high and low temperatures depends on the specific application, material properties, and substrate limitations.
Summary Table:
Aspect | High-Temperature Deposition | Low-Temperature Deposition |
---|---|---|
Process Examples | CVD, some PVD methods | Cold spray, low-temperature CVD, sputtering |
Temperature Range | 500°C to 1200°C (CVD) | Ambient to moderate temperatures |
Impact on Substrate | May damage heat-sensitive substrates | Preserves substrate integrity |
Material Quality | Enhanced adhesion and film quality | Suitable for temperature-sensitive materials |
Applications | Semiconductor manufacturing | Flexible electronics, polymers |
Need help optimizing your deposition process? Contact our experts today for tailored solutions!