Vacuum casting is a widely used manufacturing process for producing high-quality prototypes and small-batch production parts. Its accuracy depends on several factors, including the mold material, casting resin, process control, and post-processing techniques. Typically, vacuum casting can achieve dimensional tolerances of ±0.15 mm per 100 mm, making it suitable for applications requiring fine details and precise geometries. However, its accuracy is influenced by the quality of the master model, the skill of the operator, and the specific materials used. While it may not match the precision of CNC machining or injection molding, vacuum casting offers a cost-effective solution for producing complex parts with good surface finishes and moderate accuracy.
Key Points Explained:
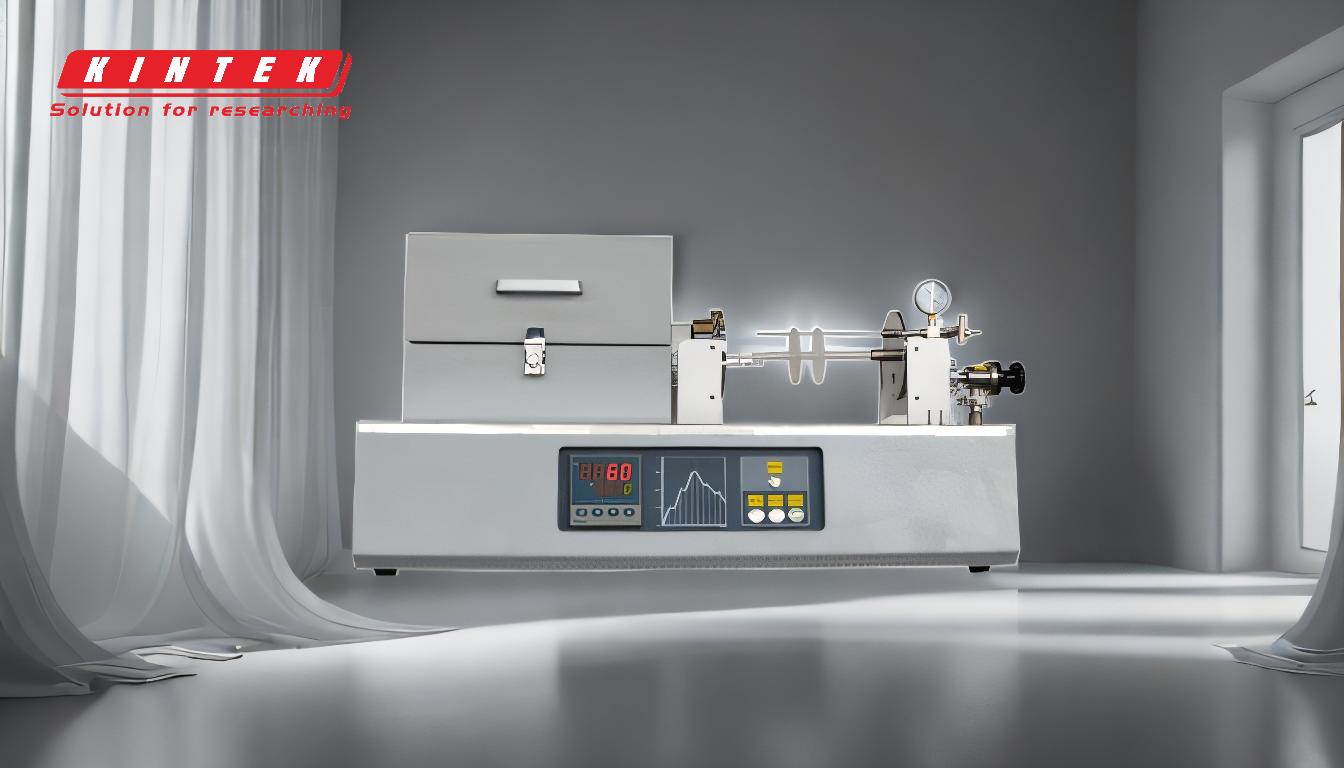
-
Dimensional Tolerances of Vacuum Casting:
- Vacuum casting typically achieves tolerances of ±0.15 mm per 100 mm, which is sufficient for most prototyping and low-volume production needs.
- This level of accuracy is influenced by factors such as mold shrinkage, resin properties, and the curing process.
-
Comparison with Other Manufacturing Methods:
- CNC Machining: Offers higher precision (±0.025 mm) but is more expensive and less suitable for complex geometries.
- Injection Molding: Provides better accuracy (±0.05 mm) and scalability but requires higher initial tooling costs.
- Vacuum casting strikes a balance between cost, complexity, and accuracy, making it ideal for prototyping and small-batch production.
-
Factors Affecting Accuracy:
- Master Model Quality: The accuracy of the final cast part depends on the precision of the master model, which is often created using 3D printing or CNC machining.
- Mold Material: Silicone molds used in vacuum casting can degrade over time, affecting the consistency and accuracy of subsequent parts.
- Casting Resin: The type of resin used (e.g., polyurethane) can impact shrinkage rates and surface finish.
- Process Control: Proper vacuum pressure, degassing, and curing times are critical to achieving consistent results.
-
Applications and Limitations:
- Vacuum casting is ideal for producing parts with intricate details, fine textures, and moderate accuracy requirements, such as consumer products, medical devices, and automotive components.
- It is less suitable for high-precision applications or large-scale production due to limitations in mold durability and material properties.
-
Post-Processing and Finishing:
- Post-processing techniques, such as sanding, painting, or coating, can enhance the surface finish and dimensional accuracy of vacuum-cast parts.
- However, excessive post-processing may introduce additional variability and reduce overall accuracy.
-
Cost-Effectiveness and Turnaround Time:
- Vacuum casting is cost-effective for small batches, with shorter lead times compared to traditional manufacturing methods.
- The ability to produce multiple parts from a single mold makes it a practical choice for prototyping and functional testing.
In summary, vacuum casting offers a good balance of accuracy, cost, and versatility for prototyping and low-volume production. While it may not match the precision of CNC machining or injection molding, its ability to produce complex parts with fine details makes it a valuable option in many industries.
Summary Table:
Aspect | Details |
---|---|
Dimensional Tolerances | ±0.15 mm per 100 mm |
Comparison | - CNC Machining: ±0.025 mm - Injection Molding: ±0.05 mm |
Key Factors | - Master Model Quality - Mold Material - Casting Resin - Process Control |
Applications | Prototyping, consumer products, medical devices, automotive components |
Limitations | Less suitable for high-precision or large-scale production |
Cost-Effectiveness | Ideal for small batches with shorter lead times |
Need precise prototypes or small-batch parts? Contact us today to explore vacuum casting solutions!