Industrial furnaces are heated primarily through two methods: burning fuel or converting electricity into heat. Fuel-powered furnaces, such as those using natural gas, are the most common due to the lower cost of fuel compared to electricity. These furnaces rely on direct fuel combustion to generate heat within the internal chamber. Electric furnaces, on the other hand, use electrical heaters with ceramic fiber and metallic wire thermal elements, which heat through conduction, convection, or blackbody radiation. Electric furnaces are preferred in specific applications where precise temperature control and the absence of combustion byproducts are critical. Temperature control in industrial furnaces varies from basic fuel flow regulation to advanced proportional and pulse control systems, which optimize efficiency and consistency.
Key Points Explained:
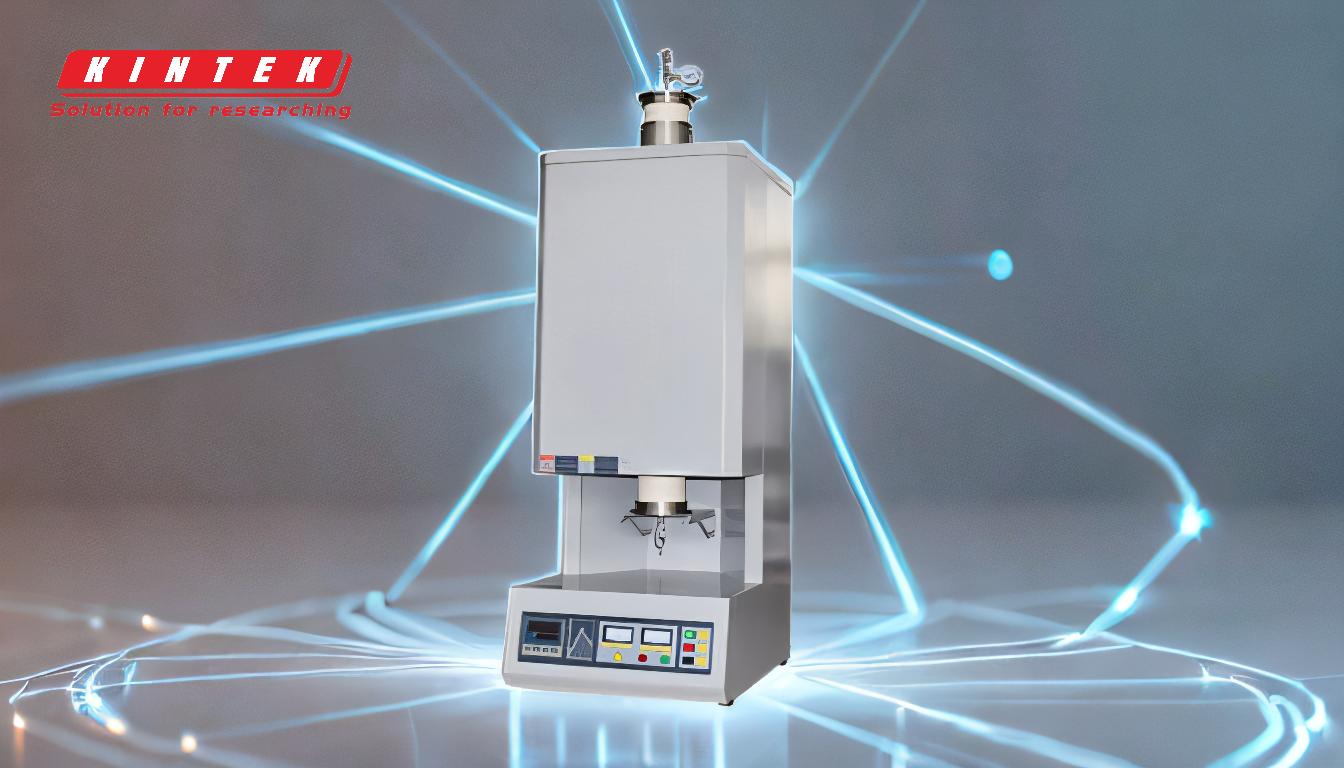
-
Primary Heating Methods:
-
Fuel-Powered Heating:
- This is the most common method due to the lower cost of fuel compared to electricity.
- Natural gas furnaces, for example, use direct fuel combustion to generate heat within the furnace's internal chamber.
- The combustion process involves burning fuel (e.g., natural gas, oil, or coal) in the presence of oxygen, releasing heat energy.
-
Electric Heating:
- Electric furnaces convert electrical energy into heat through processes like conduction, convection, or blackbody radiation.
- These furnaces are often used in applications requiring precise temperature control or where combustion byproducts are undesirable.
- Electric heaters typically use ceramic fiber and metallic wire thermal elements, which are efficient and provide consistent heating.
-
Fuel-Powered Heating:
-
Advantages of Fuel-Powered Furnaces:
- Cost-Effectiveness: Fuel is generally cheaper than electricity, making fuel-powered furnaces more economical for large-scale industrial applications.
- High Heat Output: Fuel combustion can generate very high temperatures, suitable for processes like metal smelting or glass manufacturing.
- Wide Availability: Fuels like natural gas, oil, and coal are widely available, making fuel-powered furnaces accessible in most regions.
-
Advantages of Electric Furnaces:
- Precision and Control: Electric furnaces offer precise temperature control, which is crucial in processes like semiconductor manufacturing or heat treatment of metals.
- Clean Operation: Since electric furnaces do not involve combustion, they produce no combustion byproducts, making them environmentally friendly and suitable for cleanroom environments.
- Energy Efficiency: Electric furnaces can be more energy-efficient in specific applications, especially when combined with advanced insulation materials like low-mass vacuum-formed ceramic insulation.
-
Temperature Control Systems:
-
Basic Systems:
- These systems regulate only the fuel flow, which is cost-effective but less efficient.
- They are suitable for processes where precise temperature control is not critical.
-
Proportional Systems:
- These systems control both fuel and air supply, improving fuel efficiency and reducing operating costs.
- They are more efficient than basic systems and are used in applications requiring moderate temperature control.
-
Pulse Control Systems:
- These systems maintain a fixed ratio of fuel and air with high flame velocity, ensuring consistent temperatures throughout the process cycle.
- They are ideal for processes requiring high precision and uniformity in temperature, such as in the heat treatment of metals.
-
Basic Systems:
-
Innovations in Heating Technology:
- Ceramic Fiber Insulation: Advances in low-mass vacuum forming of ceramic insulation have improved the thermodynamic capacities of electric furnaces, making them more efficient and capable of reaching higher temperatures.
- Metallic Wire Thermal Elements: These elements are commonly used in electric furnaces due to their durability and ability to withstand high temperatures, providing consistent and reliable heating.
-
Applications of Different Heating Methods:
- Fuel-Powered Furnaces: Commonly used in industries like steel production, glass manufacturing, and chemical processing, where high temperatures and large-scale operations are required.
- Electric Furnaces: Preferred in industries like electronics, aerospace, and precision engineering, where clean, precise, and controlled heating is necessary.
By understanding these key points, a purchaser can make informed decisions about the type of furnace that best suits their industrial needs, balancing factors like cost, efficiency, precision, and environmental impact.
Summary Table:
Aspect | Fuel-Powered Furnaces | Electric Furnaces |
---|---|---|
Primary Heating Method | Direct fuel combustion | Conduction, convection, or blackbody radiation |
Cost | Lower fuel costs | Higher electricity costs |
Heat Output | High temperatures for large-scale applications | Precise, controlled heating |
Environmental Impact | Produces combustion byproducts | Clean operation, no byproducts |
Applications | Steel, glass, chemical industries | Electronics, aerospace, precision engineering |
Need help choosing the right furnace for your industry? Contact our experts today!