Sintering is a critical process that significantly influences the mechanical properties of materials, particularly ceramics and metals. By heating materials to temperatures below their melting points, sintering promotes particle bonding and densification, leading to improved strength, hardness, and wear resistance. The process affects microstructural features such as grain size, pore size, and grain boundary distribution, which in turn determine the material's mechanical integrity. For example, higher sintering temperatures can increase compressive strength but may also affect shrinkage and porosity. Understanding these relationships is essential for optimizing material performance in applications requiring durability and consistency.
Key Points Explained:
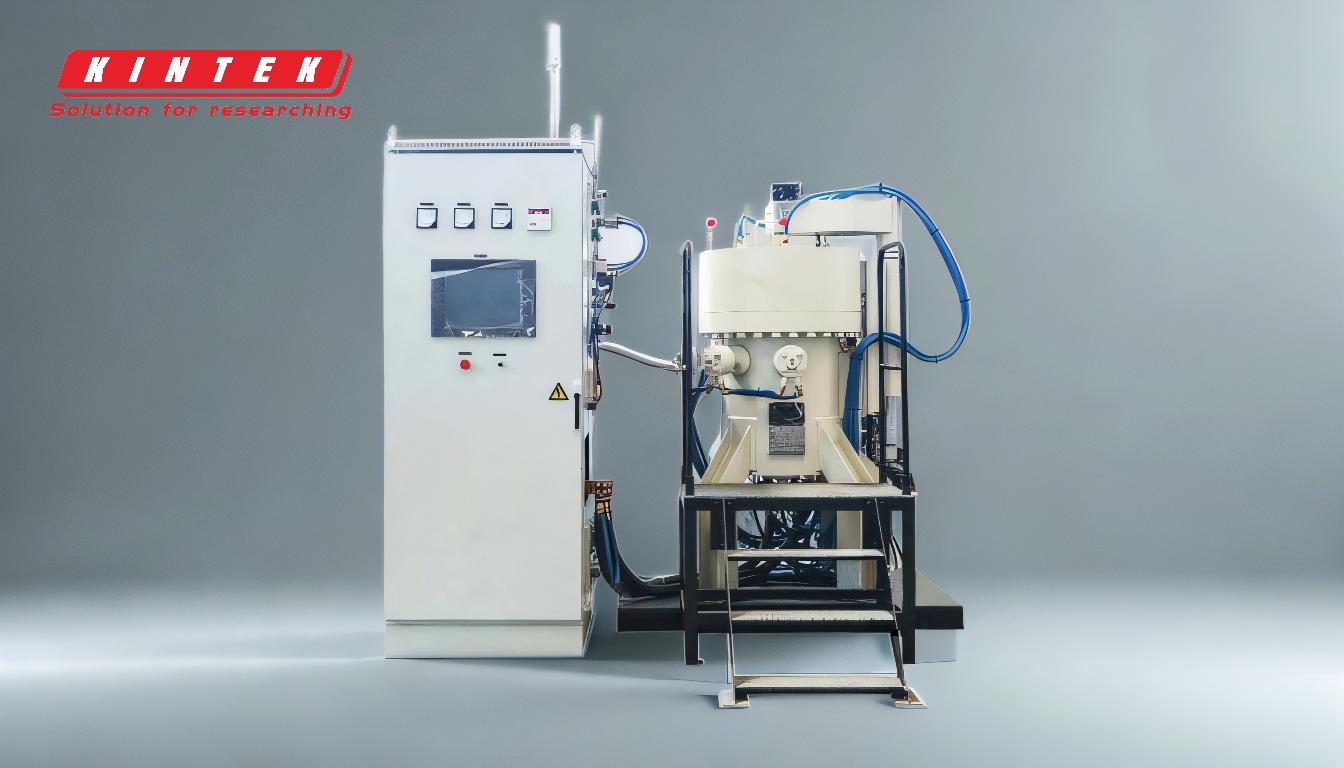
-
Impact of Sintering on Microstructure:
- Sintering alters the microstructure of materials by influencing grain size, pore size, and grain boundary distribution.
- Smaller grain sizes and reduced porosity generally lead to stronger and more durable materials.
- The shape and distribution of grain boundaries play a crucial role in determining mechanical properties such as strength and toughness.
-
Effect of Sintering Temperature:
- Higher sintering temperatures can enhance compressive strength. For example, ceramics sintered at 900 °C achieve a compressive strength of 21.09 MPa.
- However, optimal shrinkage and porosity are often achieved at lower temperatures, such as 800 °C for ceramics.
- Temperature control is essential to balance strength and porosity, as excessive temperatures can lead to unwanted grain growth or defects.
-
Densification and Mechanical Properties:
- Sintering densifies materials by reducing porosity, which directly improves mechanical properties like strength, hardness, and wear resistance.
- Fully dense parts exhibit the desired material properties, such as high strength and durability, which are critical for industrial applications.
- Densification also enhances the material's ability to withstand external stresses and environmental conditions.
-
Energy Efficiency and Environmental Benefits:
- Sintering requires less energy compared to melting, making it an environmentally friendly manufacturing process.
- The process allows for greater control over material properties, resulting in consistent and high-quality products.
- Reduced energy consumption aligns with sustainable manufacturing practices, making sintering a preferred method for producing durable components.
-
Enhanced Performance Characteristics:
- Sintered materials exhibit superior performance characteristics, including increased strength, hardness, and wear resistance.
- The controlled heating and diffusion mechanisms during sintering contribute to the development of a dense and cohesive structure.
- These improvements make sintered components ideal for demanding applications in industries such as aerospace, automotive, and construction.
By understanding how sintering affects mechanical properties, manufacturers can optimize the process to produce materials with tailored characteristics for specific applications. This knowledge is particularly valuable for purchasers of equipment and consumables, as it ensures the selection of materials that meet performance and durability requirements.
Summary Table:
Key Aspect | Impact on Mechanical Properties |
---|---|
Microstructure Alteration | Influences grain size, pore size, and grain boundary distribution, enhancing strength and toughness. |
Sintering Temperature Control | Higher temperatures increase compressive strength but may affect shrinkage and porosity. |
Densification | Reduces porosity, improving strength, hardness, and wear resistance. |
Energy Efficiency | Requires less energy than melting, aligning with sustainable manufacturing practices. |
Performance Characteristics | Produces materials with superior strength, hardness, and durability for demanding applications. |
Optimize your sintering process for superior material performance—contact our experts today!