Physical Vapor Deposition (PVD) coatings are applied through a highly controlled process that involves vaporizing a solid material in a vacuum environment and depositing it onto a substrate to form a thin, durable film. The process is widely used in industries such as aerospace, automotive, and tool manufacturing to enhance surface properties like hardness, wear resistance, and corrosion resistance. The key steps include preparing the substrate, creating a vacuum, vaporizing the target material, and depositing the vaporized material onto the substrate. Reactive gases can be introduced to modify the coating's properties, and the process is carried out in a vacuum chamber to ensure cleanliness and precision.
Key Points Explained:
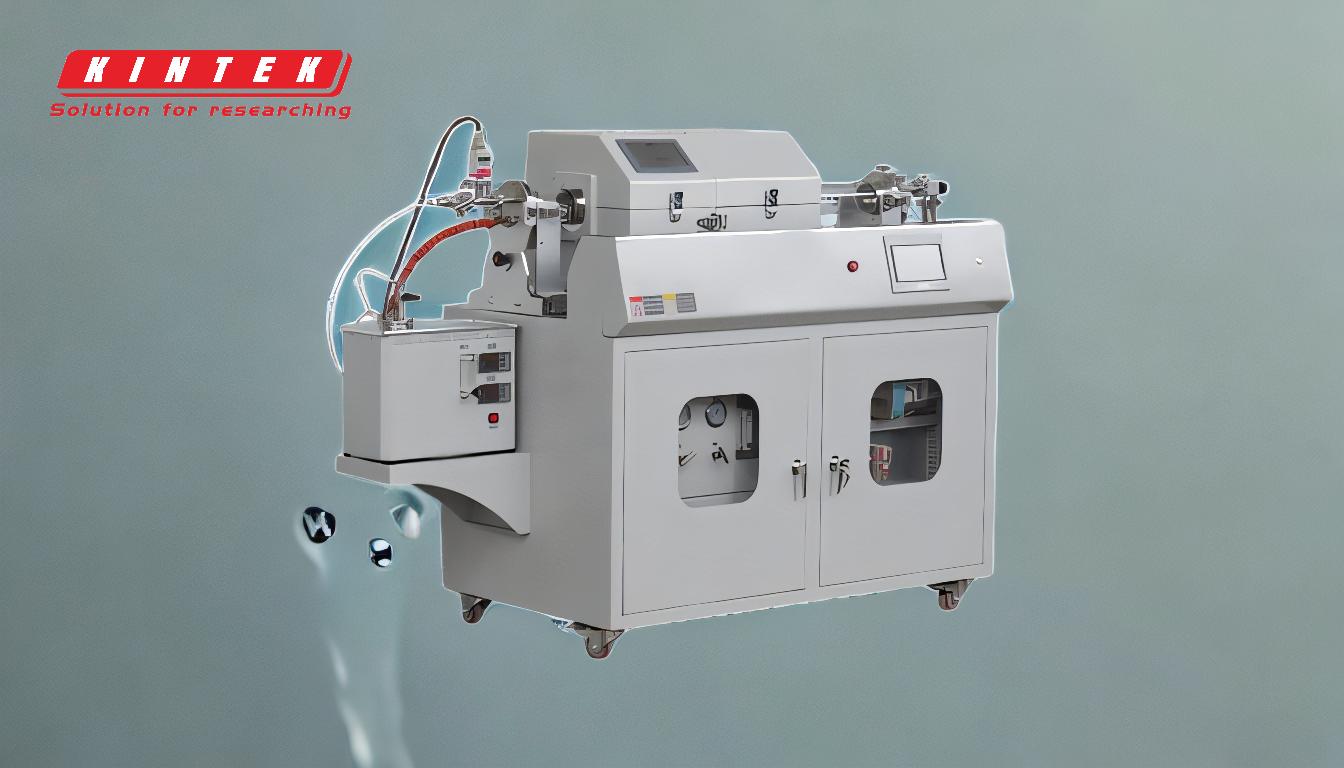
-
Preparation of the Substrate:
- Cleaning: The substrate is thoroughly cleaned to remove contaminants like oils, dust, or oxides. This step is crucial to ensure strong adhesion of the coating.
- Pretreatment: The substrate may undergo additional treatments, such as etching or ion bombardment, to improve surface roughness and enhance coating adhesion.
-
Creation of a Vacuum Environment:
- The substrate and target material are placed in a vacuum chamber, which is then evacuated to create a high-vacuum environment (typically 10⁻³ to 10⁻⁹ Torr). This step ensures that the vaporized material remains uncontaminated and can be precisely controlled.
-
Vaporization of the Target Material:
-
Techniques for Vaporization: Various methods are used to vaporize the target material, including:
- Electron Beam Evaporation: A high-energy electron beam heats the target material until it vaporizes.
- Sputtering: Ion bombardment dislodges atoms from the target material.
- Cathodic Arc Evaporation: A high-current arc vaporizes the target material.
- Thermal Evaporation: The target material is heated in a crucible until it vaporizes.
- Reactive Gases: Reactive gases like nitrogen or oxygen can be introduced to modify the composition of the vaporized material, forming compounds such as metal nitrides or oxides.
-
Techniques for Vaporization: Various methods are used to vaporize the target material, including:
-
Transportation of Vaporized Material:
- The vaporized atoms or molecules are transported through the vacuum chamber to the substrate. This step is influenced by the vacuum pressure and the distance between the target and substrate.
-
Deposition onto the Substrate:
- The vaporized material condenses onto the substrate, forming a thin, uniform film. The deposition process can be enhanced by:
- Ion Bombardment: Ions are used to improve the density and adhesion of the coating.
- Plasma Assistance: A plasma environment can enhance the reactivity and uniformity of the coating.
- The vaporized material condenses onto the substrate, forming a thin, uniform film. The deposition process can be enhanced by:
-
Post-Deposition Processes:
- Quality Control: The coating is inspected to ensure it meets specifications for thickness, adhesion, and performance.
- Finishing: Additional treatments, such as polishing or surface modification, may be applied to improve the coating's appearance or functionality.
-
Advantages of PVD Coatings:
- Durability: PVD coatings are highly resistant to wear, corrosion, and oxidation.
- Precision: The process allows for precise control over coating thickness and composition.
- Versatility: A wide range of materials can be used as targets, and the properties of the coating can be tailored by adjusting process parameters.
By following these steps, PVD coatings provide a high-performance, durable surface that meets the demanding requirements of modern industrial applications.
Summary Table:
Step | Key Details |
---|---|
Preparation of Substrate | Cleaning and pretreatment (etching, ion bombardment) for strong adhesion. |
Vacuum Environment | High-vacuum chamber (10⁻³ to 10⁻⁹ Torr) ensures contamination-free vaporization. |
Vaporization Techniques | Electron beam, sputtering, cathodic arc, or thermal evaporation methods. |
Reactive Gases | Nitrogen or oxygen modifies coating properties (e.g., metal nitrides/oxides). |
Transportation & Deposition | Vaporized material condenses onto substrate for uniform, thin film formation. |
Post-Deposition Processes | Quality control and finishing (polishing, surface modification) for performance. |
Discover how PVD coatings can enhance your industrial applications—contact our experts today!