To reduce sintering issues such as cracking and unevenness, it is essential to focus on material selection, process optimization, and equipment adjustments. By choosing suitable materials, optimizing sintering parameters, and ensuring uniform heating, you can significantly improve product quality and yield. Key strategies include using sintering aids, controlling heating zones, and matching the original heat curve to minimize defects. Additionally, understanding sintering mechanisms, such as liquid phase sintering, can help lower temperatures and enhance microstructural development. Implementing these steps systematically will lead to a more efficient and consistent sintering process.
Key Points Explained:
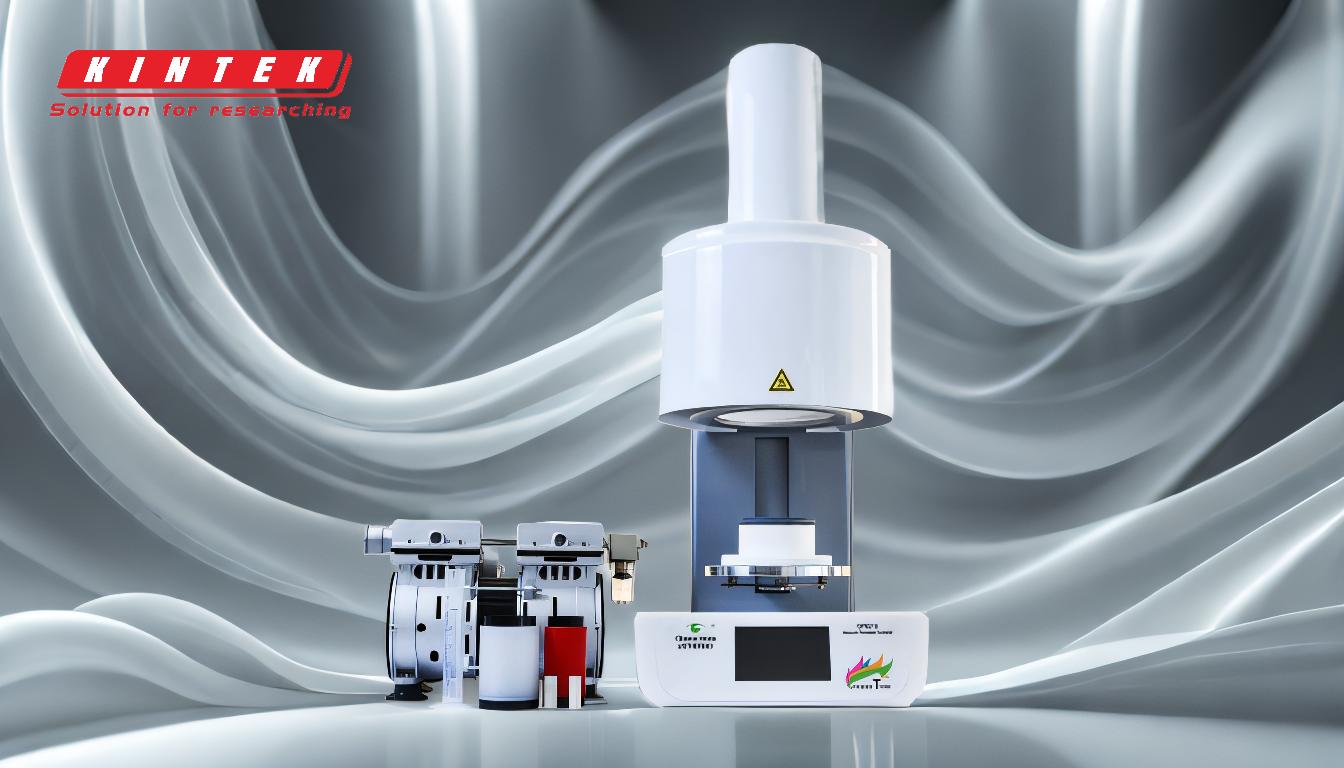
-
Material Selection:
- Importance: Choosing the right materials is crucial to reducing sintering defects like cracking. Materials with better thermal and mechanical properties can withstand the sintering process more effectively.
-
Actionable Steps:
- Evaluate material properties such as thermal conductivity, melting point, and mechanical strength.
- Consider using sintering aids or additives that form transient liquid phases to improve particle bonding.
-
Optimizing Sintering Parameters:
- Importance: Properly adjusted sintering parameters ensure uniform heating and cooling, reducing the risk of cracking and unevenness.
-
Actionable Steps:
- Adjust temperature profiles to match the material's requirements.
- Control heating and cooling rates to minimize thermal stress.
- Monitor and adjust pressure settings to ensure consistent densification.
-
Equipment Adjustments:
- Importance: Advanced equipment can provide better control over the sintering process, leading to more uniform results.
-
Actionable Steps:
- Use a rotating drum with a driving device to ensure even material distribution.
- Independently control heating zones in the electric furnace to match the desired heat curve.
- Implement real-time monitoring systems to measure and adjust the sintering process dynamically.
-
Understanding Sintering Mechanisms:
- Importance: A deep understanding of sintering mechanisms can lead to innovative solutions for reducing defects and improving material properties.
-
Actionable Steps:
- Study liquid phase sintering to lower the sintering temperature and enhance particle bonding.
- Explore the use of sintering aids that form transient liquid phases at particle contact surfaces.
- Investigate the impact of different sintering atmospheres on material properties.
-
Matching the Original Heat Curve:
- Importance: Ensuring that the sintering process matches the original heat curve is critical for maintaining product consistency and quality.
-
Actionable Steps:
- Use precise measurement tools to replicate the original heat curve.
- Adjust the sintering process parameters to align with the historical data.
- Continuously monitor and refine the process to maintain alignment with the desired heat curve.
By systematically addressing each of these key points, you can effectively reduce sintering issues and achieve a more reliable and high-quality sintering process.
Summary Table:
Key Area | Importance | Actionable Steps |
---|---|---|
Material Selection | Choosing the right materials reduces defects like cracking. | - Evaluate thermal conductivity, melting point, and mechanical strength. Use sintering aids for better particle bonding. |
Optimizing Parameters | Proper parameters ensure uniform heating and cooling, reducing defects. | - Adjust temperature profiles, control heating/cooling rates, and monitor pressure settings for consistent densification. |
Equipment Adjustments | Advanced equipment improves control and uniformity in the sintering process. | - Use rotating drums, independently control heating zones, and implement real-time monitoring systems. |
Sintering Mechanisms | Understanding mechanisms like liquid phase sintering lowers temperatures. | - Study liquid phase sintering, explore sintering aids, and investigate sintering atmospheres. |
Matching Heat Curve | Aligning with the original heat curve ensures product consistency and quality. | - Use precise tools to replicate heat curves, adjust parameters, and continuously monitor the process. |
Ready to optimize your sintering process? Contact our experts today for tailored solutions!