Reducing the power consumption of an induction furnace is a critical goal for improving energy efficiency and lowering operational costs. By focusing on optimizing the furnace design, improving operational practices, and leveraging advanced technologies like IGBT (Insulated Gate Bipolar Transistor) induction furnaces, significant energy savings can be achieved. Key strategies include proper maintenance, optimizing melting cycles, using high-quality raw materials, and ensuring efficient power management systems. These measures not only reduce power consumption but also enhance the overall performance and lifespan of the furnace.
Key Points Explained:
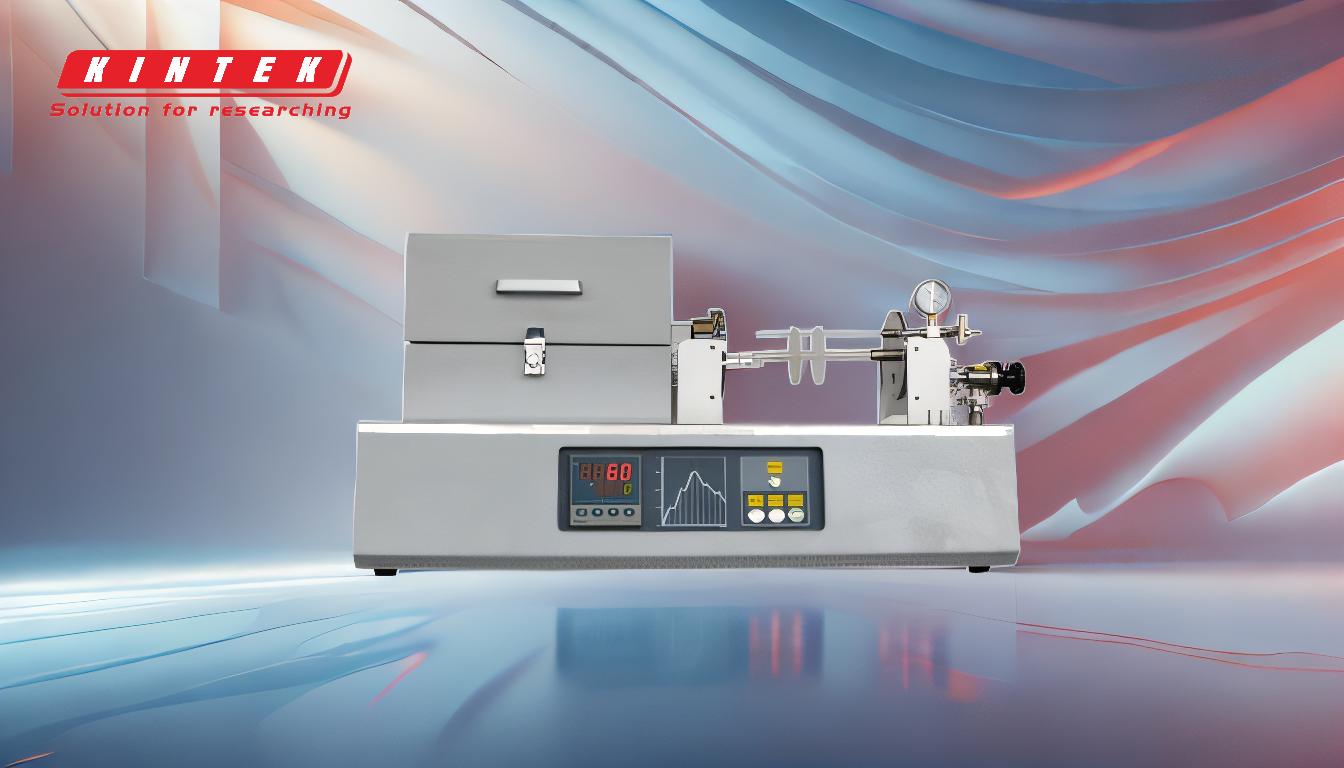
-
Optimize Furnace Design and Technology:
- Upgrade to an IGBT induction furnace, which is more energy-efficient compared to traditional SCR (Silicon Controlled Rectifier) based furnaces. IGBT technology offers better power control, higher frequency operation, and reduced heat loss, leading to lower energy consumption.
- Ensure the furnace is properly insulated to minimize heat loss. High-quality refractory materials and proper lining thickness can significantly reduce energy waste.
-
Improve Operational Practices:
- Batch Size Optimization: Avoid underloading or overloading the furnace. Operating at optimal batch sizes ensures efficient energy use and reduces power consumption per unit of material.
- Preheating Raw Materials: Preheating materials before loading them into the furnace can reduce the energy required for melting. This can be done using waste heat recovery systems.
- Optimize Melting Cycles: Implement shorter and more efficient melting cycles by adjusting power settings based on the material type and quantity. Avoid prolonged idling or standby modes.
-
Regular Maintenance and Monitoring:
- Conduct regular inspections and maintenance of the furnace components, including coils, crucibles, and power supply systems. Worn-out or damaged parts can lead to energy inefficiencies.
- Use advanced monitoring systems to track energy consumption in real-time. This helps identify inefficiencies and allows for timely corrective actions.
-
Use High-Quality Raw Materials:
- Impurities in raw materials can increase energy consumption during melting. Using high-quality, clean materials reduces the time and energy required for the melting process.
- Ensure proper material preparation, such as cutting or shredding, to facilitate faster and more uniform melting.
-
Efficient Power Management:
- Implement power factor correction systems to improve the efficiency of the electrical supply. A poor power factor can lead to higher energy losses and increased power consumption.
- Use variable frequency drives (VFDs) to control the speed and power of the induction furnace, ensuring it operates at the most efficient levels.
-
Heat Recovery and Reuse:
- Install heat recovery systems to capture and reuse waste heat generated during the melting process. This heat can be used for preheating raw materials or other industrial processes, reducing overall energy demand.
-
Training and Operator Awareness:
- Train operators on best practices for energy-efficient furnace operation. Educated operators can make informed decisions to minimize energy waste.
- Encourage a culture of energy conservation within the facility, where all staff are aware of the importance of reducing power consumption.
By implementing these strategies, you can significantly reduce the power consumption of your induction furnace, leading to cost savings and improved environmental sustainability.
Summary Table:
Strategy | Key Actions |
---|---|
Optimize Furnace Design | Upgrade to IGBT induction furnaces, ensure proper insulation. |
Improve Operational Practices | Optimize batch sizes, preheat raw materials, and refine melting cycles. |
Regular Maintenance | Inspect coils, crucibles, and power systems; use real-time energy monitoring. |
High-Quality Raw Materials | Use clean materials and prepare them properly for faster melting. |
Efficient Power Management | Implement power factor correction and variable frequency drives (VFDs). |
Heat Recovery | Capture and reuse waste heat for preheating or other processes. |
Operator Training | Train staff on energy-efficient practices and foster a culture of conservation. |
Ready to cut your furnace's power consumption? Contact our experts today for tailored solutions!