Improving corrosion resistance is a critical aspect of material selection and design, especially in industries where exposure to harsh environments is common. Corrosion can lead to material degradation, structural failures, and increased maintenance costs. To enhance corrosion resistance, several strategies can be employed, including material selection, surface treatments, environmental control, and the use of protective coatings. Each of these methods has its own advantages and limitations, and the choice of method depends on the specific application and environmental conditions. Additionally, understanding the underlying mechanisms of corrosion and the factors that influence it is essential for implementing effective corrosion resistance strategies.
Key Points Explained:
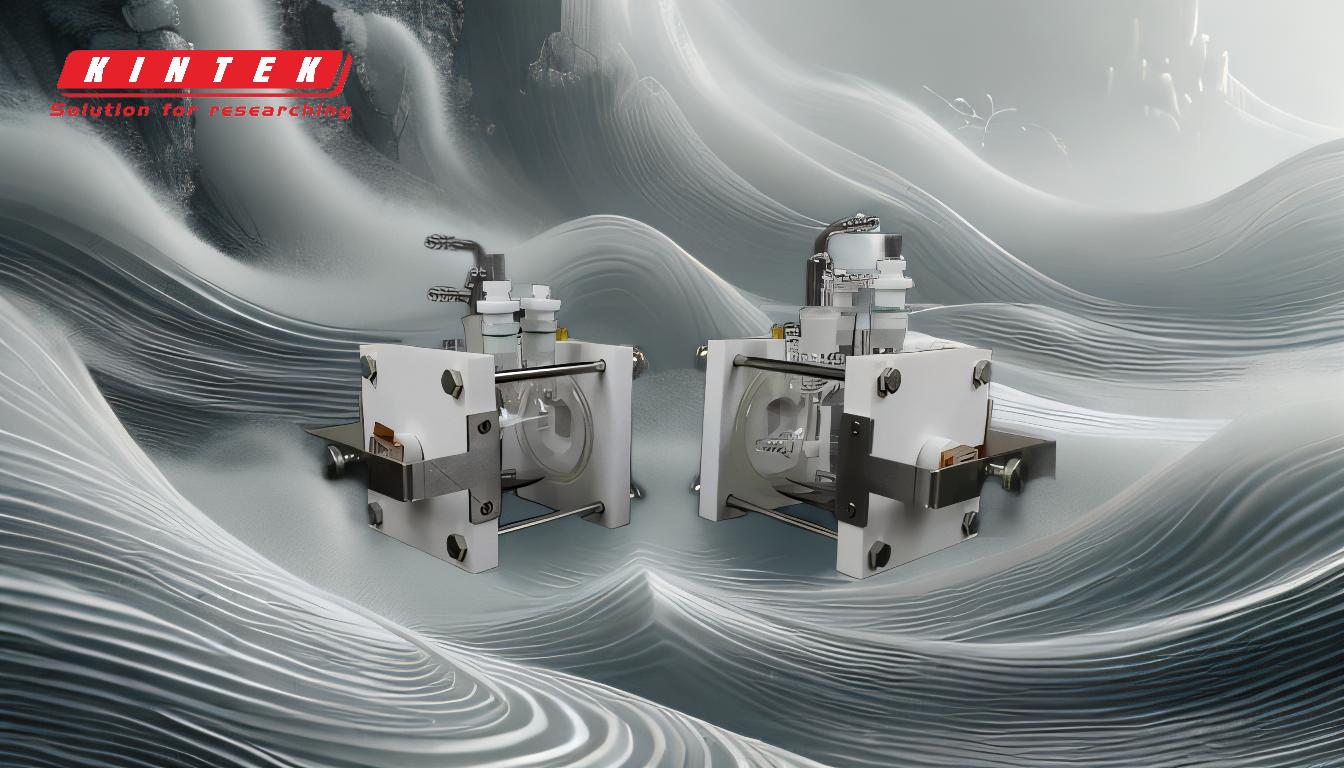
-
Material Selection:
- Stainless Steels: Stainless steels are widely used for their excellent corrosion resistance due to the presence of chromium, which forms a passive oxide layer on the surface. This layer protects the underlying material from further corrosion.
- Nickel Alloys: Nickel-based alloys, such as Inconel and Hastelloy, offer superior resistance to corrosion in highly aggressive environments, including those with high temperatures and acidic or alkaline conditions.
- Titanium: Titanium and its alloys are known for their exceptional corrosion resistance, particularly in seawater and chloride-containing environments. They form a stable oxide layer that prevents further corrosion.
-
Surface Treatments:
- Passivation: Passivation is a chemical treatment process that enhances the natural oxide layer on metals like stainless steel, making them more resistant to corrosion.
- Anodizing: Anodizing is an electrochemical process used primarily on aluminum to increase the thickness of the natural oxide layer, improving corrosion resistance and surface hardness.
- Plating: Electroplating with metals such as chromium, nickel, or zinc can provide a protective barrier against corrosion. For example, zinc plating (galvanizing) is commonly used to protect steel from rust.
-
Protective Coatings:
- Paints and Primers: Organic coatings, such as paints and primers, can be applied to metal surfaces to create a barrier against moisture and corrosive agents. These coatings often contain corrosion inhibitors to enhance their protective properties.
- Powder Coating: Powder coating involves applying a dry powder to a surface and then curing it to form a durable, corrosion-resistant layer. This method is commonly used for outdoor equipment and machinery.
- Ceramic Coatings: Ceramic coatings provide a hard, inert layer that is highly resistant to corrosion, wear, and high temperatures. They are often used in aerospace and automotive applications.
-
Environmental Control:
- Humidity Control: Reducing humidity levels in the environment can significantly decrease the rate of corrosion, especially for metals like steel and iron. This can be achieved through dehumidification systems or by controlling the ambient conditions.
- pH Control: Maintaining a neutral pH in the environment can help prevent acidic or alkaline corrosion. This is particularly important in industries like chemical processing and water treatment.
- Temperature Control: High temperatures can accelerate corrosion rates. Controlling the temperature, especially in industrial processes, can help mitigate this effect.
-
Cathodic Protection:
- Sacrificial Anodes: Sacrificial anodes are made from metals that are more electrochemically active than the metal they are protecting. They corrode preferentially, thereby protecting the main structure from corrosion. This method is commonly used in marine environments and for underground pipelines.
- Impressed Current Systems: In this method, an external power source is used to apply a direct current to the metal structure, making it the cathode in the electrochemical cell. This prevents the metal from corroding and is often used for large structures like ships and offshore platforms.
-
Design Considerations:
- Avoiding Crevices: Crevices can trap moisture and corrosive agents, leading to localized corrosion. Designing structures to minimize crevices can help improve overall corrosion resistance.
- Proper Drainage: Ensuring that water and other liquids can drain away from surfaces helps prevent the accumulation of corrosive substances.
- Material Compatibility: Using materials that are compatible with each other in terms of galvanic potential can prevent galvanic corrosion, which occurs when two dissimilar metals are in electrical contact in the presence of an electrolyte.
By combining these strategies, it is possible to significantly improve the corrosion resistance of materials and structures, thereby extending their service life and reducing maintenance costs. Each method has its own set of advantages and limitations, and the choice of method should be based on the specific requirements of the application and the environmental conditions in which the material will be used.
Summary Table:
Strategy | Key Methods | Applications |
---|---|---|
Material Selection | Stainless steels, nickel alloys, titanium | Harsh environments, marine, chemical processing |
Surface Treatments | Passivation, anodizing, plating (e.g., zinc, chromium, nickel) | Automotive, aerospace, industrial equipment |
Protective Coatings | Paints, powder coatings, ceramic coatings | Outdoor equipment, machinery, aerospace |
Environmental Control | Humidity, pH, and temperature control | Chemical processing, water treatment, industrial settings |
Cathodic Protection | Sacrificial anodes, impressed current systems | Marine environments, pipelines, offshore platforms |
Design Considerations | Avoid crevices, ensure proper drainage, use compatible materials | Structural engineering, construction, manufacturing |
Need help improving corrosion resistance for your materials? Contact our experts today for tailored solutions!