Choosing a lab filter press involves understanding your specific filtration needs, the characteristics of the slurry or material to be filtered, and the operational environment. Key considerations include the type of filter press (e.g., plate and frame, recessed chamber), material of construction, filtration area, pressure requirements, and automation level. Additionally, factors such as ease of maintenance, cost, and compliance with industry standards should be evaluated. By systematically assessing these parameters, you can select a filter press that optimizes filtration efficiency, durability, and overall performance for your laboratory or industrial application.
Key Points Explained:
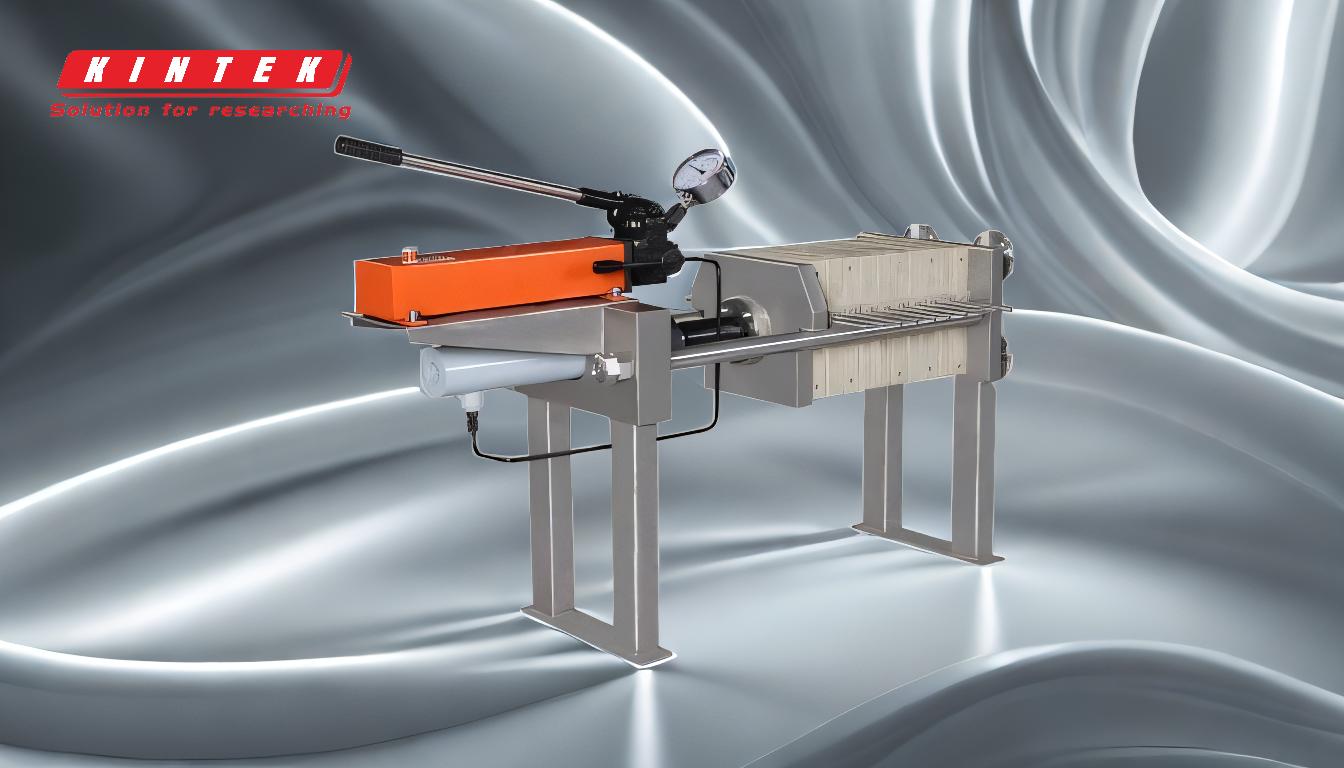
-
Understand Your Filtration Needs:
- Material Characteristics: Determine the properties of the slurry or material to be filtered, such as particle size, viscosity, and chemical compatibility. This will influence the choice of filter media and the design of the filter press.
- Filtration Goals: Identify whether your primary goal is to achieve high clarity, high throughput, or both. This will help in selecting the appropriate type of filter press and its configuration.
-
Types of Filter Presses:
- Plate and Frame Filter Press: This type consists of alternating plates and frames that create chambers for filtration. It is suitable for applications requiring high clarity and is often used in laboratories for small-scale filtration.
- Recessed Chamber Filter Press: This design features recessed plates that form chambers without the need for separate frames. It is ideal for handling larger volumes and more viscous materials.
- Membrane Filter Press: Incorporates flexible membranes that can be inflated to squeeze the filter cake, enhancing dewatering efficiency. This type is beneficial for applications requiring low moisture content in the filter cake.
-
Material of Construction:
- Compatibility: Choose materials that are chemically resistant to the substances being filtered. Common materials include polypropylene, stainless steel, and cast iron.
- Durability: Consider the mechanical strength and longevity of the materials, especially in high-pressure or corrosive environments.
-
Filtration Area and Capacity:
- Filtration Area: The total surface area available for filtration directly impacts the throughput and efficiency. Ensure the filtration area matches your volume requirements.
- Chamber Volume: The volume of each chamber determines the amount of material that can be processed in a single cycle. Select a filter press with an appropriate chamber volume for your needs.
-
Pressure Requirements:
- Operating Pressure: Determine the maximum pressure required to achieve effective filtration. Higher pressures may be needed for fine particles or high-viscosity materials.
- Pressure Rating: Ensure the filter press can safely operate at the required pressures without risk of failure or leakage.
-
Automation and Control:
- Manual vs. Automated: Manual filter presses are cost-effective but require more labor. Automated systems offer higher efficiency and consistency, especially in continuous or large-scale operations.
- Control Systems: Advanced control systems can monitor and adjust parameters such as pressure, temperature, and cycle time, enhancing filtration performance and repeatability.
-
Ease of Maintenance:
- Accessibility: Consider how easy it is to access and replace filter plates, cloths, and other components. Easy maintenance reduces downtime and operational costs.
- Cleaning: Evaluate the ease of cleaning the filter press, especially if handling materials that are prone to clogging or require frequent cleaning.
-
Cost and Budget:
- Initial Investment: Compare the upfront costs of different filter press models, considering both the equipment and installation expenses.
- Operational Costs: Factor in ongoing costs such as energy consumption, maintenance, and replacement parts. A higher initial investment may be justified by lower long-term costs.
-
Compliance and Standards:
- Industry Standards: Ensure the filter press complies with relevant industry standards and regulations, such as those for food, pharmaceuticals, or hazardous materials.
- Certifications: Look for certifications that indicate quality and safety, such as ISO or CE marks.
By carefully evaluating these factors, you can select a lab filter press that meets your specific requirements, ensuring efficient and reliable filtration for your laboratory or industrial processes.
Summary Table:
Factor | Key Considerations |
---|---|
Filtration Needs | Material characteristics, filtration goals (clarity, throughput) |
Types of Filter Press | Plate and frame, recessed chamber, membrane filter press |
Material of Construction | Chemical compatibility, durability (polypropylene, stainless steel, cast iron) |
Filtration Area | Surface area, chamber volume |
Pressure Requirements | Operating pressure, pressure rating |
Automation | Manual vs. automated, control systems |
Maintenance | Accessibility, cleaning ease |
Cost | Initial investment, operational costs |
Compliance | Industry standards, certifications (ISO, CE) |
Need help choosing the right filter press? Contact our experts today for personalized guidance!