PVD (Physical Vapor Deposition) coatings are known for their durability, versatility, and resistance to wear, corrosion, and scratches. However, proper care is essential to maintain their longevity and performance. PVD coatings can be damaged by hard impacts or abrasive materials, so gentle cleaning methods are recommended. Understanding the factors that influence PVD coating properties, such as temperature, thickness, and material type, can help in maintaining their quality. Regular cleaning with soft materials like cotton or microfiber cloths is ideal for daily maintenance, ensuring the coating remains intact and functional over time.
Key Points Explained:
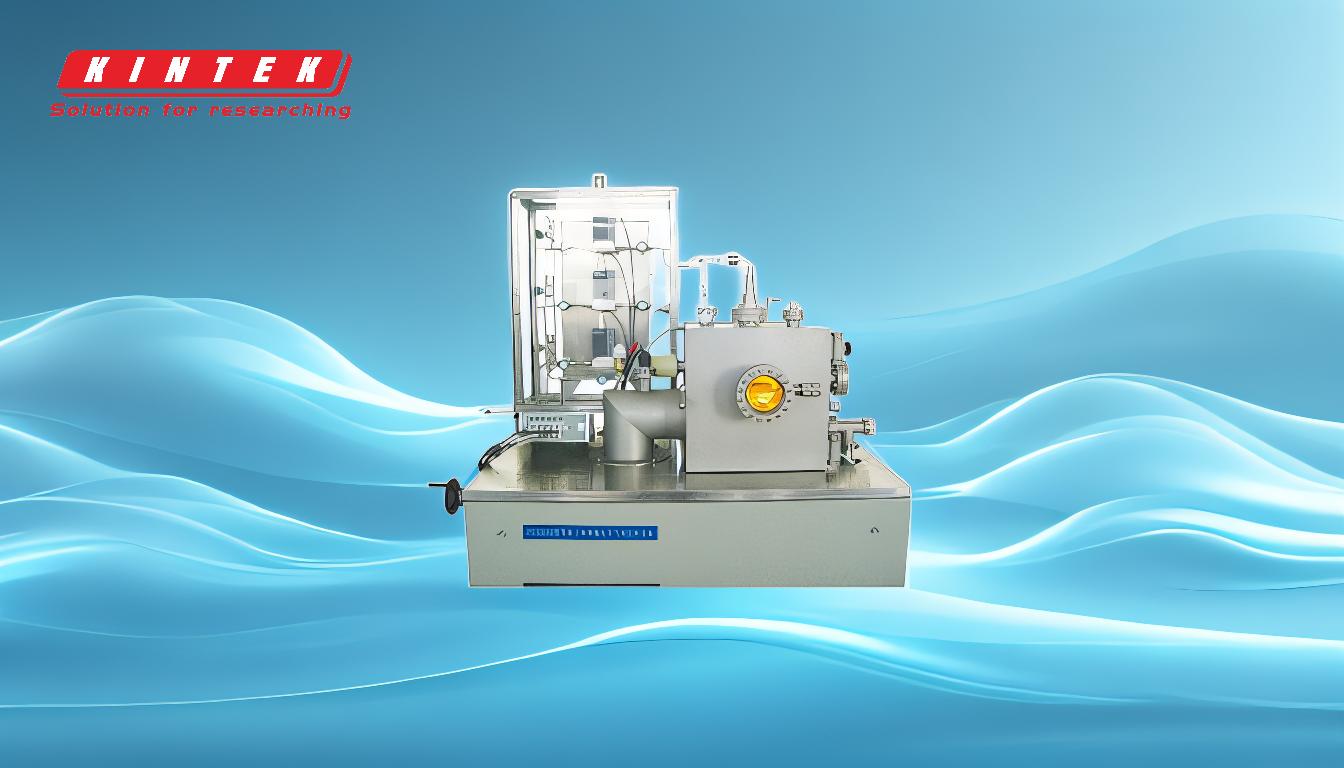
-
Durability and Resistance of PVD Coatings
- PVD coatings are highly durable, with excellent resistance to abrasion, corrosion, and scratches. They are four times harder than chrome and can withstand significant wear and tear.
- Despite their robustness, PVD coatings can still be damaged by hard impacts or repeated rubbing with abrasive materials. This makes proper care crucial to maintaining their integrity.
-
Factors Influencing PVD Coating Properties
- The characteristics of PVD coatings, such as friction, color, and hardness, can be controlled by adjusting factors like temperature, coating thickness, the nature of the coating substance, vacuum chamber pressure, and the volume and type of reagent gases.
- Understanding these factors can help in selecting the right PVD coating for specific applications and ensuring its long-term performance.
-
Cleaning and Maintenance of PVD Coatings
- PVD coatings do not require cleaning before deposition, unlike CVD coatings. However, regular cleaning is essential for maintenance.
- For daily cleaning, it is recommended to use a soft and clean cotton or microfiber cloth. Avoid using abrasive materials or harsh chemicals that could damage the coating.
-
Applications and Versatility of PVD Coatings
- PVD coatings are versatile and can be applied to almost any inorganic coating material over a wide range of substrates. They are suitable for various applications due to their ability to generate different finishes.
- Their versatility makes them ideal for industries requiring durable and aesthetically pleasing coatings, such as automotive, aerospace, and consumer electronics.
-
Techniques for Assessing PVD Coating Quality
- Various thin film characterization techniques can be used to measure the physical properties of PVD coatings. These include:
- Calo tester for coating thickness.
- Nanoindentation for hardness.
- Pin-on-disc tester for wear and friction coefficient.
- Scratch tester for coating adhesion.
- X-ray micro-analyzer for investigating structural features and elemental composition.
- These techniques help ensure the quality and performance of PVD coatings, providing valuable data for maintenance and improvement.
- Various thin film characterization techniques can be used to measure the physical properties of PVD coatings. These include:
By following these guidelines, you can effectively care for PVD coatings, ensuring they remain durable, functional, and visually appealing over time.
Summary Table:
Key Aspect | Details |
---|---|
Durability | Highly resistant to abrasion, corrosion, and scratches; 4x harder than chrome. |
Cleaning | Use soft cotton or microfiber cloths; avoid abrasives or harsh chemicals. |
Influencing Factors | Temperature, coating thickness, material type, and vacuum chamber pressure. |
Applications | Versatile for automotive, aerospace, and consumer electronics industries. |
Quality Assessment Tools | Calo tester, nanoindentation, pin-on-disc tester, scratch tester, X-ray analyzer. |
Ensure your PVD coatings stay durable and functional—contact our experts today for personalized advice!