Cleaning a sputtering chamber is a critical process to ensure the quality and consistency of thin film coatings. The process involves several steps, including pre-cleaning methods, vacuum and heating procedures, and regular maintenance. Pre-cleaning methods such as RF glow plate, gridded ion source, and plasma pre-treaters are used to prepare the chamber surface. The vacuum chamber must be closed, heated to remove moisture, and pumped to full vacuum before the coating process begins. Regular cleaning of the chamber's internal components, such as electrodes and gas pipelines, is essential to maintain optimal performance. Proper cleaning techniques and the use of appropriate detergents are crucial to avoid damaging the equipment.
Key Points Explained:
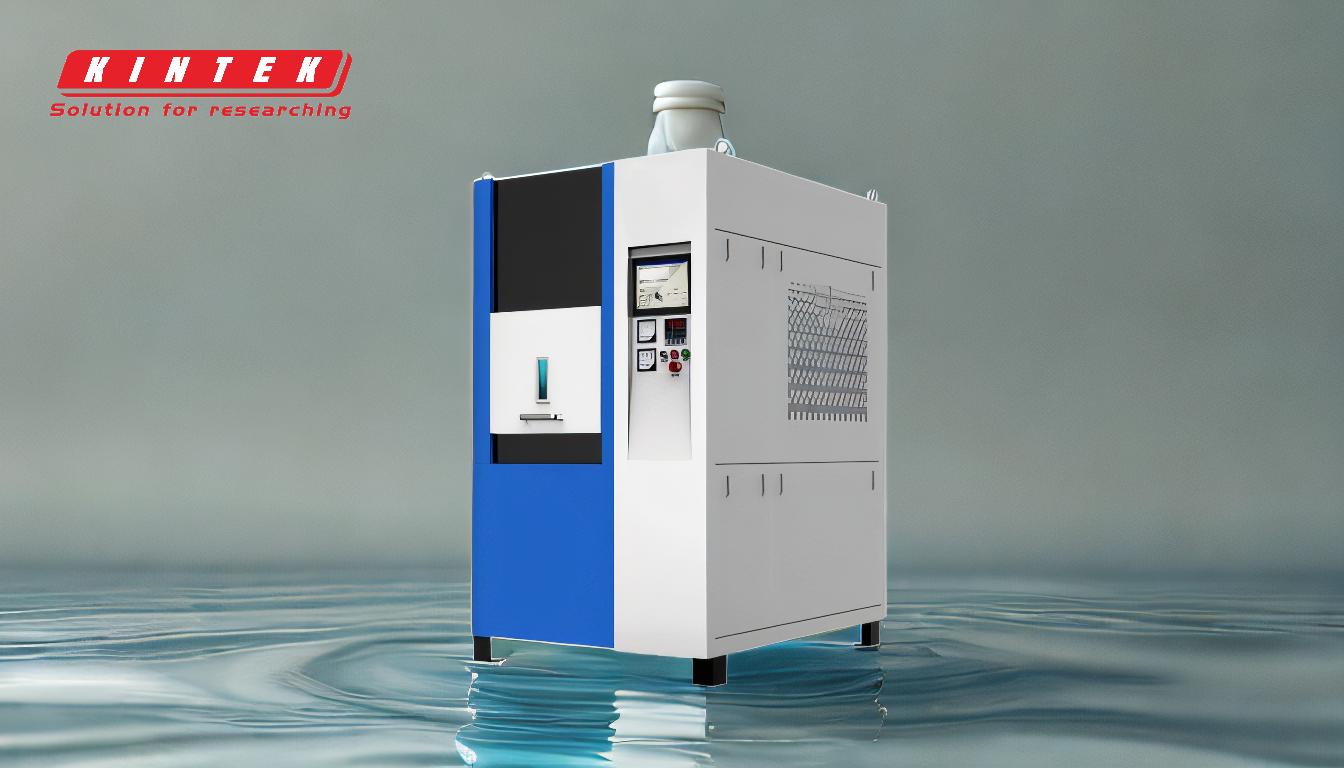
-
Pre-Cleaning Methods:
- RF Glow Plate: This method uses radio frequency (RF) energy to create a glow discharge that cleans the chamber surfaces by removing contaminants.
- Gridded Ion Source: This involves using a grid to focus ion beams that clean the chamber surfaces. It is effective for removing stubborn contaminants.
- Gridless End-Hall Ion Source: This method uses a gridless design to generate a broad ion beam, which is useful for cleaning large areas.
- Plasma Pre-Treater: This technique uses plasma to clean and activate the chamber surfaces, improving adhesion for subsequent coatings.
- RF or Microwave Plasma Pre-Treater: These methods use RF or microwave energy to generate plasma, which is effective for thorough cleaning and surface activation.
-
Vacuum and Heating Procedures:
- Closing the Vacuum Chamber: The chamber must be sealed to create a vacuum environment, which is essential for the sputtering process.
- Heating the Chamber: Turning on the heater helps to remove any water vapor or moisture from the chamber, ensuring a dry environment.
- Starting the Vacuum Pump: The vacuum pump is started to evacuate the chamber, reaching the required vacuum level for the sputtering process.
- Reaching Full Vacuum and Operating Temperature: The chamber must achieve full vacuum and the recommended operating temperature before the coating process can begin. This ensures optimal conditions for thin film deposition.
-
Regular Cleaning of Internal Components:
- Equipment Surface: The outer surfaces of the sputtering chamber should be cleaned regularly to prevent dust and contaminants from entering the chamber.
- Internal Cavity: The internal cavity of the chamber must be cleaned to remove any residual materials or contaminants that could affect the coating process.
- Electrodes: Electrodes should be cleaned to ensure proper electrical conductivity and prevent arcing during the sputtering process.
- Gas Pipelines: Gas pipelines must be cleaned to prevent blockages and ensure the proper flow of gases required for the sputtering process.
-
Use of Appropriate Detergents and Tools:
- Choosing the Right Detergents: It is important to use detergents that are effective yet gentle enough to avoid damaging the chamber components. Harsh chemicals can degrade the materials used in the chamber.
- Tools for Cleaning: Appropriate tools, such as soft brushes, lint-free cloths, and non-abrasive sponges, should be used to clean the chamber without causing scratches or other damage.
-
Avoiding Harsh Cleaners:
- Risks of Harsh Cleaners: Using cleaners that are too harsh or chemically strong can damage the delicate components of the sputtering chamber, leading to costly repairs or replacements.
- Safe Cleaning Practices: Always follow the manufacturer's recommendations for cleaning agents and procedures to ensure the longevity and performance of the sputtering chamber.
By following these steps and using the appropriate methods and materials, you can effectively clean a sputtering chamber, ensuring high-quality thin film coatings and maintaining the equipment's performance and longevity.
Summary Table:
Step | Details |
---|---|
Pre-Cleaning Methods | RF Glow Plate, Gridded Ion Source, Plasma Pre-Treater, RF/Microwave Plasma |
Vacuum & Heating | Close chamber, heat to remove moisture, pump to full vacuum, reach temp |
Regular Cleaning | Clean internal components (electrodes, gas pipelines), equipment surfaces |
Detergents & Tools | Use gentle detergents, soft brushes, lint-free cloths, non-abrasive sponges |
Avoid Harsh Cleaners | Follow manufacturer guidelines to prevent damage to chamber components |
Need expert advice on maintaining your sputtering chamber? Contact us today for tailored solutions!