Heat treating aluminum castings is a critical process to enhance their mechanical properties, such as strength, hardness, and durability. The process involves controlled heating and cooling to achieve desired material characteristics. Common heat treatment methods for aluminum castings include solution heat treatment, quenching, and aging (either natural or artificial). Each step must be carefully controlled to avoid defects like warping or cracking. The specific parameters, such as temperature, time, and cooling rate, depend on the alloy composition and the intended application of the casting. Proper heat treatment ensures the castings meet performance requirements and industry standards.
Key Points Explained:
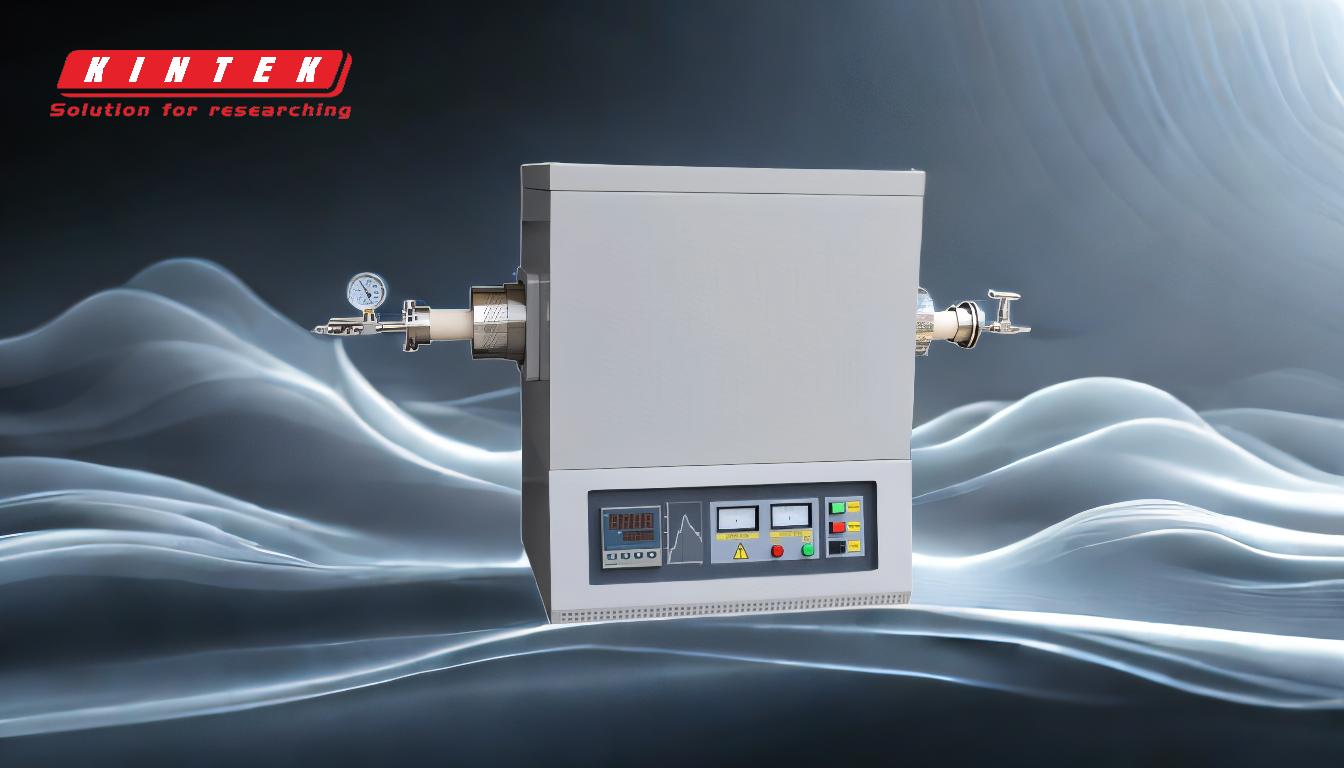
-
Solution Heat Treatment:
- Purpose: Dissolve alloying elements into the aluminum matrix to create a uniform solid solution.
- Process: The casting is heated to a temperature just below its melting point (typically between 450°C and 540°C, depending on the alloy) and held for a specific duration.
- Importance: Ensures the alloying elements are evenly distributed, which is crucial for subsequent strengthening processes.
-
Quenching:
- Purpose: Rapidly cool the casting to "freeze" the solid solution structure achieved during solution heat treatment.
- Process: The casting is quickly immersed in water, oil, or air to achieve rapid cooling.
- Challenges: Improper quenching can lead to warping, cracking, or residual stresses. The cooling medium and rate must be carefully selected based on the alloy and casting geometry.
-
Aging:
- Natural Aging: The casting is left at room temperature for several days to allow precipitation hardening. This process is slower and less controllable.
- Artificial Aging: The casting is heated to a lower temperature (typically 120°C to 200°C) for a specific time to accelerate precipitation hardening.
- Outcome: Aging increases the strength and hardness of the casting by forming fine precipitates within the aluminum matrix.
-
Alloy-Specific Considerations:
- Different aluminum alloys respond differently to heat treatment. For example, 2xxx, 6xxx, and 7xxx series alloys are heat-treatable, while 1xxx and 3xxx series are not.
- The exact heat treatment parameters (temperature, time, cooling rate) must be tailored to the specific alloy to achieve optimal results.
-
Pre- and Post-Treatment Steps:
- Pre-Treatment: Cleaning the casting to remove surface contaminants like oils or oxides is essential to ensure uniform heating and avoid defects.
- Post-Treatment: Machining or surface finishing may be required after heat treatment to achieve the final dimensions and surface quality.
-
Quality Control:
- Heat-treated castings must undergo rigorous testing, including hardness testing, tensile testing, and microstructure analysis, to ensure they meet the required specifications.
- Non-destructive testing methods, such as ultrasonic or X-ray inspection, may also be used to detect internal defects.
-
Common Challenges and Solutions:
- Warping and Distortion: Controlled heating and cooling rates, along with proper fixture design, can minimize these issues.
- Cracking: Avoiding thermal shocks during quenching and ensuring uniform heating can prevent cracking.
- Inconsistent Properties: Precise control of temperature and time during each stage of heat treatment ensures consistent material properties.
By following these steps and considerations, aluminum castings can be effectively heat-treated to achieve the desired mechanical properties and performance characteristics.
Summary Table:
Step | Purpose | Process | Key Considerations |
---|---|---|---|
Solution Heat Treatment | Dissolve alloying elements into the aluminum matrix for uniform distribution. | Heat to 450°C–540°C, hold for a specific duration. | Temperature and time depend on alloy composition. |
Quenching | Rapidly cool to "freeze" the solid solution structure. | Immerse in water, oil, or air for rapid cooling. | Avoid warping, cracking, and residual stresses by selecting the right cooling medium. |
Aging | Increase strength and hardness through precipitation hardening. | Natural aging (room temperature) or artificial aging (120°C–200°C for a specific time). | Tailor aging method and duration to the alloy and application. |
Alloy-Specific Considerations | Ensure optimal results based on alloy type. | Adjust parameters (temperature, time, cooling rate) for 2xxx, 6xxx, and 7xxx series alloys. | Non-heat-treatable alloys (1xxx, 3xxx) require alternative approaches. |
Pre- and Post-Treatment | Prepare and finish castings for heat treatment. | Clean before heating; machine or finish after treatment. | Remove contaminants and achieve final dimensions and surface quality. |
Quality Control | Verify mechanical properties and detect defects. | Perform hardness, tensile, and microstructure tests; use ultrasonic or X-ray inspection. | Ensure compliance with industry standards and specifications. |
Need expert guidance on heat treating aluminum castings? Contact us today for tailored solutions!