Protecting PVD (Physical Vapor Deposition) coatings involves understanding their properties, application process, and potential vulnerabilities. PVD coatings are highly durable, corrosion-resistant, and scratch-resistant due to their atomic-level deposition process. However, ensuring their longevity requires proper handling, application, and maintenance. Key considerations include protecting the coating during application, avoiding exposure to harmful environments, and maintaining the substrate's integrity. Additionally, understanding the specific materials and processes used in PVD coatings can help tailor protective measures to maximize their performance.
Key Points Explained:
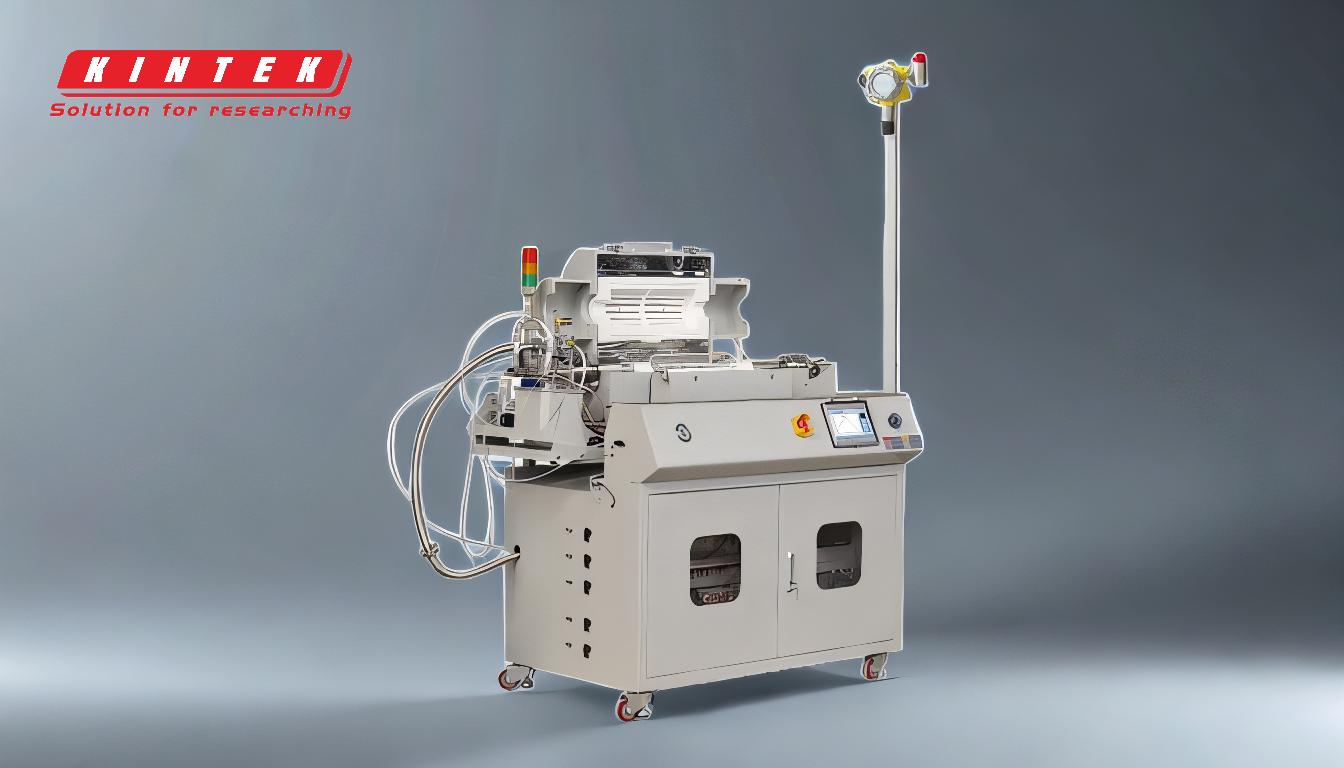
-
Understanding the PVD Coating Process:
- PVD coatings are created by vaporizing a target material in a vacuum and depositing it onto a substrate. This process ensures a pure, durable, and long-lasting coating.
- The atomic-level deposition allows for precise control over the coating's density, structure, and properties, such as hardness, adhesion, and corrosion resistance.
-
Protecting PVD Coatings During Application:
- During the PVD process, precautions must be taken to avoid inhaling vaporized particles, as they can be harmful. Proper ventilation and protective equipment are essential.
- Ensuring a clean and contaminant-free environment during application prevents impurities from compromising the coating's integrity.
-
Enhancing Durability Through Material Selection:
- The choice of target material significantly impacts the coating's properties. For example, materials like titanium nitride (TiN) or chromium nitride (CrN) are commonly used for their hardness and corrosion resistance.
- Tailoring the coating material to the specific application (e.g., wear resistance, lubricity) ensures optimal performance and longevity.
-
Protecting PVD Coatings from Environmental Factors:
- While PVD coatings are highly resistant to corrosion and wear, prolonged exposure to harsh environments (e.g., saltwater or extreme temperatures) can degrade them over time.
- Applying additional protective layers or sealants can further enhance resistance to environmental stressors.
-
Maintaining Substrate Integrity:
- The durability of PVD coatings depends on the substrate's condition. Any defects or impurities in the substrate can weaken the coating's adhesion and performance.
- Proper surface preparation, such as cleaning and polishing, ensures a strong bond between the coating and the substrate.
-
Avoiding Mechanical Damage:
- Although PVD coatings are scratch-resistant, excessive mechanical stress or abrasion can damage them. Using tools or equipment with care minimizes the risk of surface damage.
- For high-wear applications, selecting coatings with enhanced hardness or lubricity can reduce wear and tear.
-
Regular Maintenance and Inspection:
- Periodic inspection of PVD-coated surfaces helps identify early signs of wear or damage, allowing for timely repairs or recoating.
- Cleaning coated surfaces with appropriate methods (e.g., mild detergents, non-abrasive cloths) maintains their appearance and functionality.
-
Reapplying PVD Coatings When Necessary:
- Over time, even the most durable coatings may wear out. Reapplying PVD coatings through the same vacuum deposition process restores their protective properties.
- The annealing process, which involves heating and replacing the coating layer, can be used to refresh the surface.
By following these steps, you can effectively protect PVD coatings and maximize their durability, ensuring they perform optimally in various applications.
Summary Table:
Key Steps to Protect PVD Coatings | Details |
---|---|
Understand the PVD Process | Atomic-level deposition ensures durability, hardness, and corrosion resistance. |
Protect During Application | Use proper ventilation and protective equipment; maintain a contaminant-free environment. |
Choose the Right Materials | Select target materials like TiN or CrN for hardness and corrosion resistance. |
Guard Against Environmental Factors | Avoid prolonged exposure to harsh conditions; use additional protective layers if needed. |
Maintain Substrate Integrity | Ensure a clean, defect-free substrate for strong coating adhesion. |
Prevent Mechanical Damage | Handle with care; use coatings with enhanced hardness for high-wear applications. |
Regular Maintenance | Inspect and clean coated surfaces periodically to maintain functionality. |
Reapply Coatings When Needed | Restore coatings through vacuum deposition or annealing processes. |
Need expert advice on protecting PVD coatings? Contact us today to ensure optimal performance and longevity!