DC magnetron sputtering is a widely used thin-film deposition technique that utilizes a magnetic field to enhance the efficiency of the sputtering process. It involves creating a plasma in a vacuum chamber, where high-energy ions bombard a target material (cathode), causing atoms to be ejected and deposited onto a substrate. The magnetic field traps electrons, increasing their collision probability with gas atoms, which sustains the plasma and improves deposition rates. This method is known for its ability to deposit high-quality, uniform coatings at relatively low temperatures, making it suitable for a wide range of materials, including metals, alloys, and compounds.
Key Points Explained:
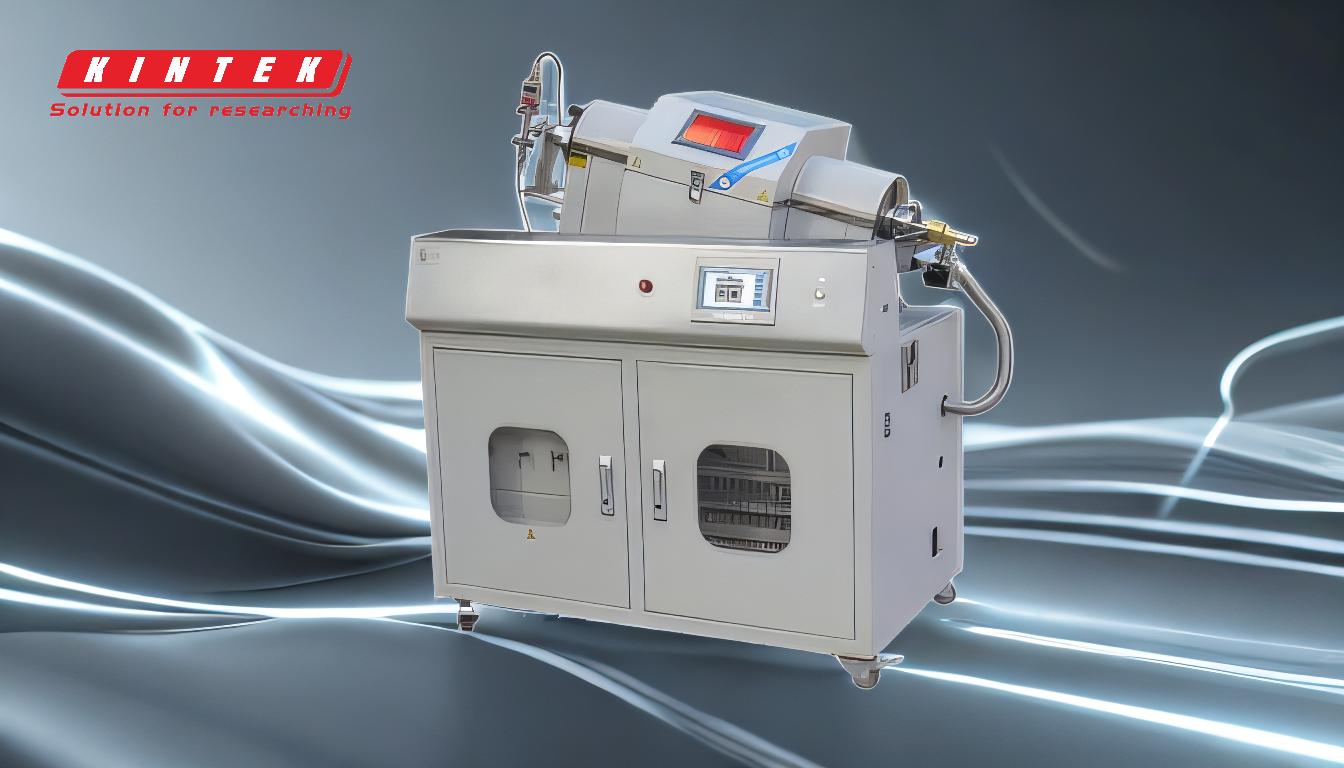
-
Generation of Plasma:
- A vacuum chamber is filled with an inert gas, typically argon.
- A high-voltage DC power supply is applied to the target material (cathode), creating a negative potential.
- This negative potential attracts positively charged argon ions from the gas, forming a plasma.
-
Role of the Magnetic Field:
- Magnets are placed behind the target to create a closed magnetic field.
- This magnetic field traps electrons, forcing them into a spiral trajectory near the target surface.
- The trapped electrons increase the likelihood of collisions with argon atoms, generating more ions and sustaining the plasma.
-
Sputtering Process:
- High-energy argon ions bombard the target surface, transferring kinetic energy to the target atoms.
- If the energy is sufficient, target atoms are ejected (sputtered) from the surface.
- These ejected atoms travel through the vacuum and deposit onto the substrate, forming a thin film.
-
Advantages of Magnetron Sputtering:
- High Deposition Rates: The magnetic field enhances plasma density, allowing for faster sputtering.
- Low Temperature Operation: The process does not require the target material to melt or evaporate, making it suitable for heat-sensitive substrates.
- Material Versatility: Compatible with a wide range of materials, including metals, alloys, and compounds, while maintaining their composition.
- Uniform Coatings: The controlled plasma and magnetic field ensure even deposition, resulting in high-quality, uniform thin films.
-
Pulsed DC Magnetron Sputtering:
- In this variation, power is applied in pulses, alternating between negative and positive voltages.
- During the "on time," a negative voltage is applied, attracting ions to the target and initiating sputtering.
- During the "reverse time," a positive voltage is applied to discharge any accumulated charges on the target surface, preventing arcing.
- This method is particularly useful for depositing dielectric materials, as it minimizes charge buildup and arcing.
-
Applications:
- Semiconductor Industry: Used for depositing conductive and insulating layers in integrated circuits.
- Optical Coatings: Ideal for creating anti-reflective, reflective, and protective coatings on lenses and mirrors.
- Decorative Coatings: Applied to consumer products for aesthetic purposes, such as metallic finishes on electronics.
- Wear-Resistant Coatings: Used in industrial applications to enhance the durability of tools and components.
-
Process Control and Optimization:
- Power Supply: The DC power supply must be carefully controlled to maintain stable plasma conditions.
- Gas Pressure: Optimal gas pressure ensures efficient ionization and sputtering.
- Magnetic Field Configuration: The strength and shape of the magnetic field can be adjusted to optimize electron trapping and plasma density.
- Substrate Positioning: Proper placement of the substrate relative to the target ensures uniform film deposition.
In summary, DC magnetron sputtering is a versatile and efficient method for depositing thin films, leveraging magnetic fields to enhance plasma generation and sputtering rates. Its ability to work with a wide range of materials and produce high-quality coatings makes it a cornerstone technology in various industries.
Summary Table:
Key Aspect | Description |
---|---|
Plasma Generation | Inert gas (e.g., argon) is ionized in a vacuum chamber using a high-voltage DC power supply. |
Magnetic Field Role | Magnets trap electrons, increasing collisions with gas atoms to sustain plasma and boost efficiency. |
Sputtering Process | High-energy ions bombard the target, ejecting atoms that deposit onto a substrate as a thin film. |
Advantages | High deposition rates, low-temperature operation, material versatility, and uniform coatings. |
Applications | Semiconductor, optical, decorative, and wear-resistant coatings. |
Process Control | Optimize power supply, gas pressure, magnetic field, and substrate positioning for best results. |
Discover how DC magnetron sputtering can elevate your thin-film deposition process—contact our experts today!