A hydraulic press generates force by utilizing the principles of fluid mechanics and Pascal's Law. It consists of a hydraulic cylinder filled with a liquid, typically oil, which transmits pressure uniformly in all directions. When force is applied to a small piston, it creates pressure in the fluid, which is then transferred to a larger piston, amplifying the force. This mechanical advantage allows the hydraulic press to generate significant force with relatively low input energy. The press can be single-acting (applying force in one direction) or double-acting (applying force in both directions), depending on the design and application requirements.
Key Points Explained:
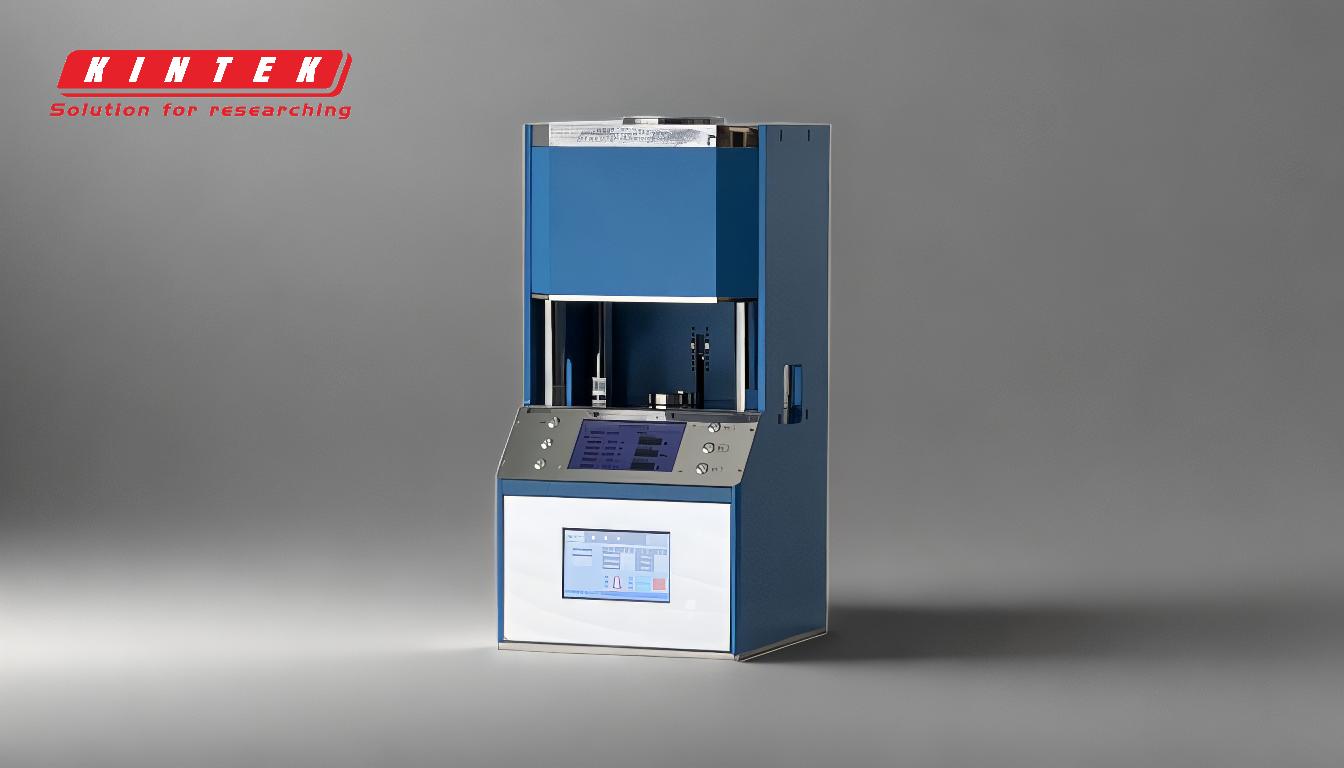
-
Principle of Hydraulic Force Generation:
- Hydraulic presses operate based on Pascal's Law, which states that pressure applied to a confined fluid is transmitted equally in all directions.
- A small input force applied to a smaller piston creates pressure in the hydraulic fluid, which is then transferred to a larger piston, resulting in a much greater output force.
-
Components of a Hydraulic Press:
- Hydraulic Cylinder: Contains the hydraulic fluid and houses the pistons. The cylinder is the core component where force is generated.
- Pistons: Two pistons of different sizes (small and large) are used. The small piston applies the input force, while the large piston generates the amplified output force.
- Hydraulic Fluid: Typically oil, which is incompressible and transmits pressure efficiently.
- Hydraulic Pump: Supplies the fluid to the cylinder, creating the necessary pressure.
-
Mechanical Advantage:
- The force amplification is achieved through the difference in the surface areas of the two pistons. The larger the area of the output piston compared to the input piston, the greater the force amplification.
- Formula: ( F_{output} = F_{input} \times \frac{A_{output}}{A_{input}} ), where ( F ) is force and ( A ) is the piston area.
-
Types of Hydraulic Presses:
- Single-Acting Press: Applies force in one direction only, typically using a spring or gravity to return the piston to its original position.
- Double-Acting Press: Applies force in both directions, using hydraulic pressure to move the piston in both the forward and backward strokes.
-
Applications of Hydraulic Presses:
- Hydraulic presses are widely used in industries such as manufacturing, automotive, and construction for tasks like metal forming, molding, and compression.
- The hydraulic hot press machine is a specialized type of hydraulic press used for applications requiring high temperatures, such as laminating or bonding materials.
-
Advantages of Hydraulic Presses:
- High force output with relatively low input energy.
- Precise control over force and speed.
- Versatility in handling a wide range of materials and applications.
-
Limitations:
- Hydraulic systems can be prone to leaks and require regular maintenance.
- The response time may be slower compared to mechanical presses due to the incompressibility of the hydraulic fluid.
By understanding these key points, one can appreciate how hydraulic presses efficiently generate force and their importance in various industrial applications.
Summary Table:
Aspect | Details |
---|---|
Principle | Operates on Pascal's Law: pressure in a confined fluid is transmitted equally. |
Components | Hydraulic cylinder, pistons (small and large), hydraulic fluid, hydraulic pump. |
Mechanical Advantage | Force amplification through piston area ratio: ( F_{output} = F_{input} \times \frac{A_{output}}{A_{input}} ). |
Types | Single-acting (one direction) or double-acting (both directions). |
Applications | Metal forming, molding, compression, and specialized uses like laminating. |
Advantages | High force output, precise control, versatility. |
Limitations | Prone to leaks, slower response time compared to mechanical presses. |
Ready to harness the power of hydraulic presses for your industrial needs? Contact us today to learn more!