A rotary furnace, also known as a rotating furnace, is a specialized heating device used for processes such as smelting, calcination, and thermal treatment of materials. It operates by rotating a cylindrical chamber around its central axis, allowing materials to be mixed and heated uniformly as they move through the furnace. The rotation ensures consistent heat distribution and efficient processing, making it ideal for applications in metallurgy, chemical processing, and waste treatment. Below, we break down the working principles and key components of a rotary furnace in detail.
Key Points Explained:
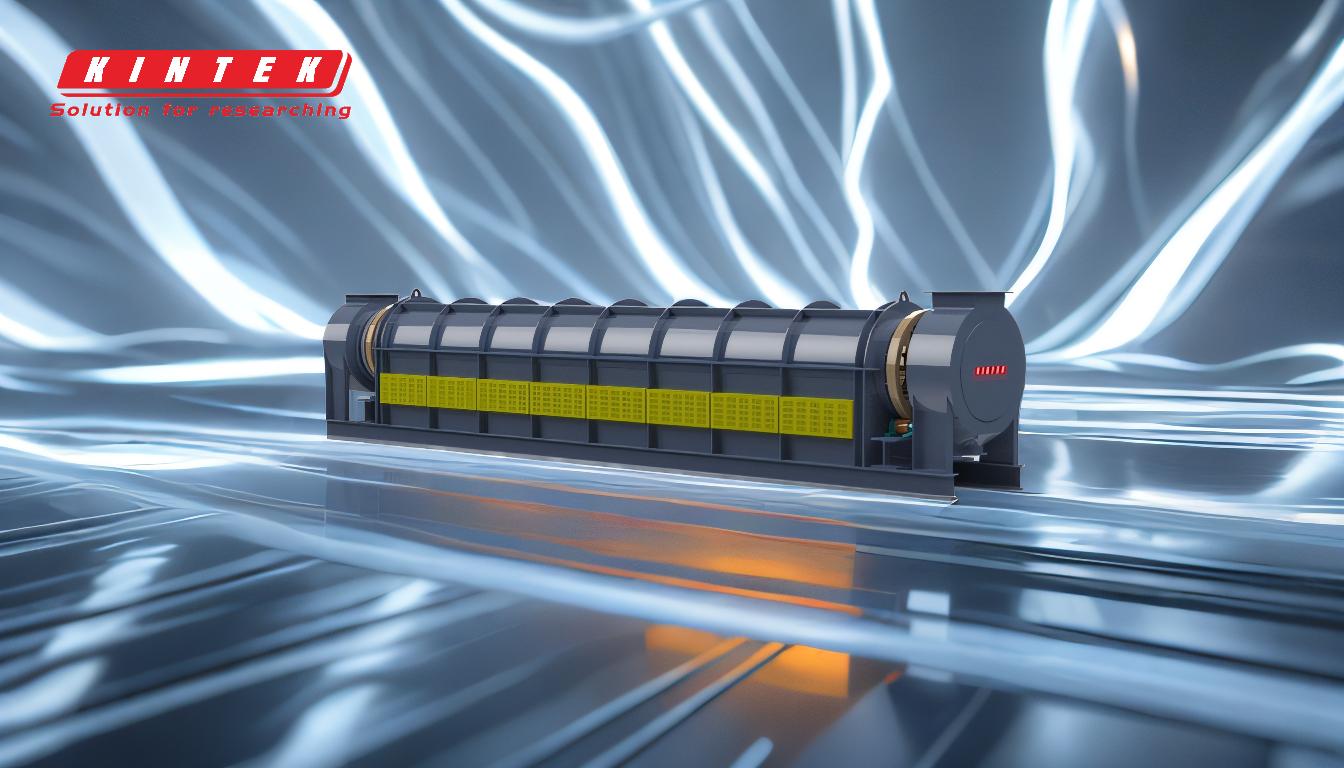
-
Structure and Components:
- Cylindrical Chamber: The main body of the rotary furnace is a cylindrical tube, typically made of heat-resistant materials like refractory bricks or metals. This chamber rotates around its central axis.
- Heating System: The furnace is equipped with burners or electric heating elements that provide the necessary heat for processing materials. The heat source is strategically placed to ensure uniform heating.
- Drive Mechanism: A motor-driven system rotates the chamber at a controlled speed, ensuring consistent movement of materials inside.
- Feed and Discharge Systems: Materials are fed into one end of the furnace and gradually move toward the discharge end as the chamber rotates.
-
Material Processing:
- The mineral feed or material is introduced into the reactor portion of the furnace. As the chamber rotates, the material is transported down the length of the tube.
- The rotation ensures thorough mixing and exposure to heat, which is critical for processes like smelting or calcination. This movement also prevents material from sticking to the walls or forming clumps.
-
Heating Mechanism:
- The heating system raises the temperature inside the chamber to the required level, depending on the material and process. The heat is evenly distributed due to the rotation of the chamber.
- In some cases, the furnace may operate under controlled atmospheres or vacuum conditions to achieve specific processing outcomes.
-
Applications:
- Metallurgy: Used for smelting metals and alloys, where uniform heating and mixing are essential.
- Chemical Processing: Ideal for calcination, pyrolysis, and other thermal treatments of chemicals.
- Waste Treatment: Effective for incinerating hazardous waste or recovering valuable materials from industrial byproducts.
-
Advantages:
- Uniform Heating: The rotating motion ensures consistent heat distribution, reducing the risk of hot spots or uneven processing.
- Efficient Mixing: The tumbling action of the materials promotes thorough mixing, which is crucial for chemical reactions or phase transformations.
- Versatility: Suitable for a wide range of materials and processes, making it a versatile tool in industrial applications.
-
Comparison with Other Furnaces:
- Unlike a pusher furnace, which moves materials in a linear fashion, a rotary furnace relies on rotation for material transport and mixing.
- Unlike a vacuum furnace, which operates under reduced pressure, a rotary furnace typically operates at atmospheric pressure unless specifically designed for vacuum conditions.
In summary, a rotary furnace is a highly efficient and versatile heating device that relies on the rotation of its chamber to ensure uniform heating and mixing of materials. Its design and operation make it suitable for a wide range of industrial applications, from metallurgy to waste treatment. For more details, refer to the topic on rotating furnace.
Summary Table:
Key Aspect | Description |
---|---|
Structure | Cylindrical chamber made of heat-resistant materials, rotating around its axis. |
Heating System | Burners or electric elements for uniform heating. |
Drive Mechanism | Motor-driven system for controlled rotation. |
Material Processing | Materials are mixed and heated uniformly as they move through the furnace. |
Applications | Metallurgy, chemical processing, and waste treatment. |
Advantages | Uniform heating, efficient mixing, and versatility. |
Discover how a rotary furnace can optimize your industrial processes—contact our experts today!