A sintering furnace is a critical piece of equipment used in the manufacturing process to bond powdered materials into a solid structure through controlled heating. The process involves several stages, including material preparation, compaction, heating, and cooling. The furnace operates by applying heat to the compacted powder, causing the particles to bond at a molecular level without completely melting. This results in a dense, cohesive, and durable product. Different types of sintering furnaces, such as vacuum, microwave, and hot press furnaces, are designed to meet specific material and application requirements. The sintering process is widely used in industries like ceramics, metallurgy, and dental restoration, where precise control of temperature, pressure, and atmosphere is essential for achieving high-quality results.
Key Points Explained:
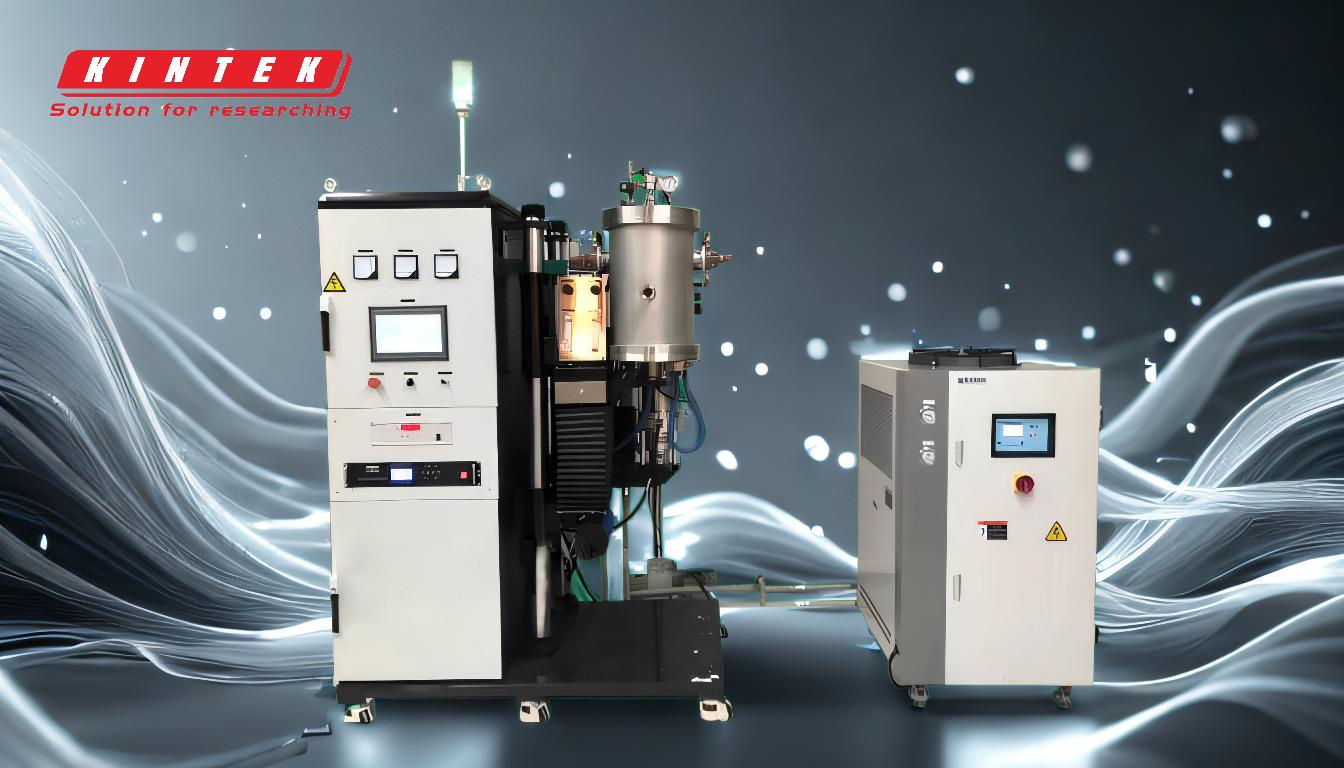
-
Stages of the Sintering Process:
- Material Preparation: The raw material, often in powder form, is prepared and mixed with additives or coupling agents to achieve the desired composition.
- Compaction: The powder is pressed into a specific shape using pressure to eliminate voids and ensure uniformity.
- Heating: The compacted material is placed in a sintering furnace and heated to a temperature below its melting point. This allows particles to bond through diffusion, forming necks and densifying the material.
- Cooling: The sintered product is cooled gradually to solidify into a rigid and cohesive structure.
-
Types of Sintering Furnaces:
- Vacuum Sintering Furnace: Operates in a vacuum environment to prevent oxidation and contamination. It uses medium-frequency induction heating to generate high temperatures, making it ideal for refractory alloys like tungsten and molybdenum.
- Microwave Sintering Furnace: Utilizes microwave energy to heat ceramic materials directly, enabling rapid and uniform heating. This method is energy-efficient and suitable for advanced ceramics.
- Hot Press Sintering Furnace: Combines high temperature and pressure in a vacuum to sinter ceramic powders. This method is particularly effective for producing dense and high-strength materials.
-
Key Components of Sintering Furnaces:
- Heating System: Provides the necessary heat to facilitate particle bonding. Different furnaces use various heating methods, such as induction, resistance, or microwave.
- Atmosphere Control: Ensures the sintering environment is free from contaminants. Vacuum or protective gas atmospheres are commonly used.
- Cooling System: Allows controlled cooling to prevent thermal stress and ensure material stability.
- Pressure System (for hot press furnaces): Applies high pressure to enhance densification during sintering.
-
Applications of Sintering Furnaces:
- Ceramics: Used to produce advanced ceramics with high strength, wear resistance, and thermal stability.
- Metallurgy: Enables the production of metal alloys, refractory metals, and powder metallurgy components.
- Dental Restoration: Ensures precise control of temperature and atmosphere to create high-quality dental prosthetics.
- Electronics: Used in the production of components like capacitors, resistors, and magnetic materials.
-
Advantages of Sintering:
- Densification: Produces materials with low porosity and high density.
- Precision: Allows for the creation of complex shapes with tight tolerances.
- Material Efficiency: Minimizes waste by using powdered materials.
- Versatility: Suitable for a wide range of materials, including metals, ceramics, and composites.
-
Challenges and Considerations:
- Temperature Control: Precise regulation of temperature is crucial to avoid defects like warping or cracking.
- Atmosphere Management: Maintaining a contaminant-free environment is essential for high-quality sintering.
- Energy Consumption: Sintering furnaces, especially high-temperature ones, can be energy-intensive.
- Equipment Cost: Advanced sintering furnaces, such as vacuum or microwave types, can be expensive to purchase and maintain.
By understanding the working principles and applications of sintering furnaces, manufacturers can select the appropriate equipment and optimize the sintering process for their specific needs. This ensures the production of high-quality, durable, and cost-effective materials and components.
Summary Table:
Aspect | Details |
---|---|
Stages of Sintering | Material Preparation, Compaction, Heating, Cooling |
Types of Furnaces | Vacuum, Microwave, Hot Press |
Key Components | Heating System, Atmosphere Control, Cooling System, Pressure System |
Applications | Ceramics, Metallurgy, Dental Restoration, Electronics |
Advantages | Densification, Precision, Material Efficiency, Versatility |
Challenges | Temperature Control, Atmosphere Management, Energy Consumption, Equipment Cost |
Discover the right sintering furnace for your needs—contact our experts today!