A vacuum coater is a specialized machine used to apply thin, protective coatings to substrates, typically metals or ceramics, through a process known as physical vapor deposition (PVD). The process occurs in a vacuum chamber where the coating material is vaporized or ionized using thermal energy or plasma, then deposited onto the substrate in a controlled environment. This creates nanoscale layers that enhance properties like hardness, wear resistance, and corrosion resistance. The vacuum coater consists of several critical components, including the vacuum chamber, vacuum system, power supply, gas input system, and cooling system, all working together to ensure precise and efficient coating deposition.
Key Points Explained:
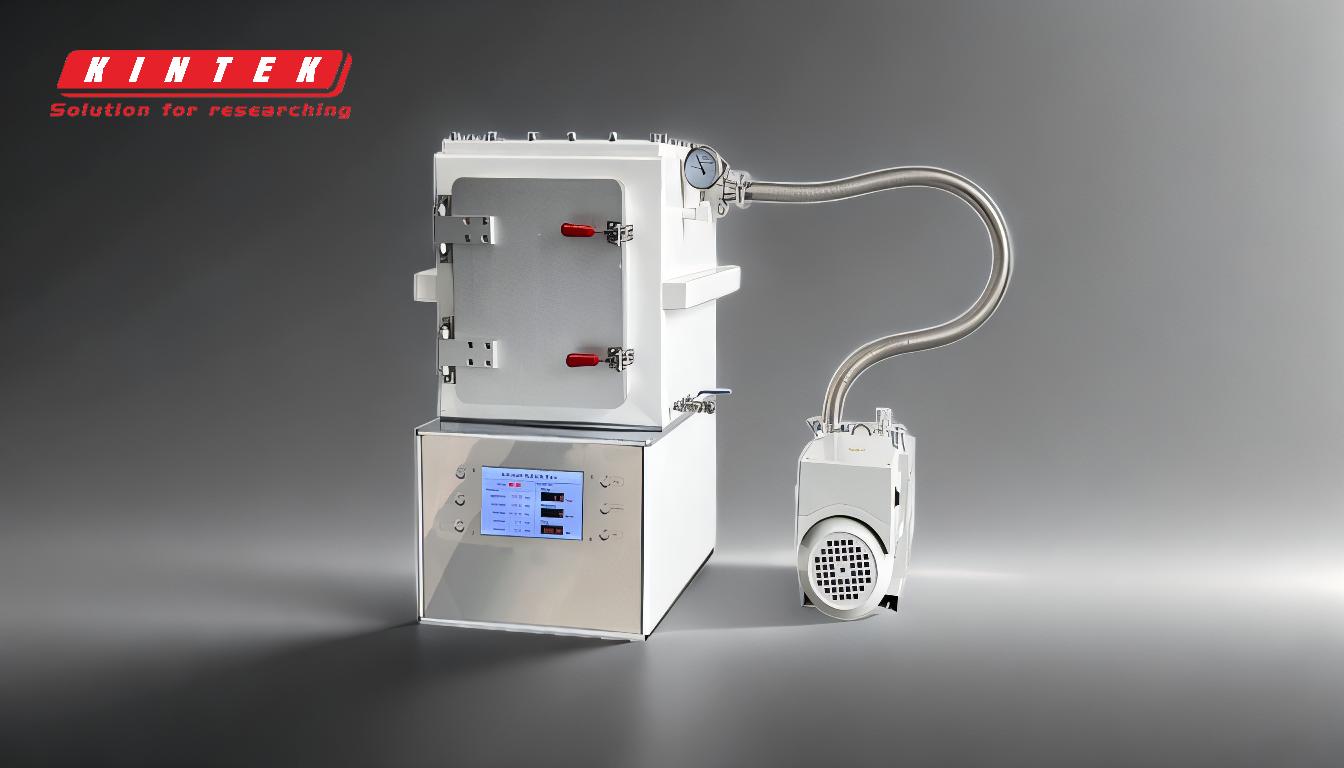
-
Vacuum Chamber and Coating Environment
- The vacuum chamber is the core of the vacuum coater, providing a controlled, sub-atmospheric environment for the coating process.
- A vacuum is essential to eliminate contaminants and ensure the purity of the coating. It also allows for the precise control of vaporized particles, which are deposited onto the substrate.
- The chamber is designed to handle high temperatures and pressures, ensuring stability during the coating process.
-
Coating Material Vaporization
- The coating material, typically a metal or ceramic, is vaporized or ionized within the vacuum chamber.
- This is achieved using thermal energy (e.g., resistive heating) or plasma, which breaks the material into atomic or molecular particles.
- The vaporized material is then transported through the vacuum environment to the substrate.
-
Deposition Process
- The vaporized coating material condenses onto the substrate, forming a thin, uniform layer.
- This process is highly controlled to ensure the desired thickness and properties of the coating, often at the nanoscale.
- The deposition can occur through various PVD techniques, such as sputtering or evaporation, depending on the application.
-
Substrate Preparation
- Before coating, the substrate undergoes thorough cleaning to remove contaminants and ensure proper adhesion of the coating.
- This may involve abrasive cleaning, chemical treatments, or plasma cleaning within the vacuum chamber.
- Proper surface preparation is critical for achieving a high-quality, durable coating.
-
Key Components of a Vacuum Coater
- Vacuum Chamber and Coating Equipment: Houses the substrate and coating material, providing a controlled environment.
- Vacuum Obtaining System: Creates and maintains the vacuum using pumps and seals.
- Vacuum Measurement System: Monitors pressure levels within the chamber.
- Power Supply: Provides energy for vaporization, ionization, and plasma generation.
- Process Gas Input System: Introduces reactive or inert gases to enhance the coating process.
- Mechanical Transmission System: Moves the substrate or coating material as needed.
- Heating and Temperature Control: Regulates the temperature for optimal coating conditions.
- Ion Evaporation and Sputtering Source: Generates the vaporized coating material.
- Water Cooling System: Prevents overheating of the machine components.
-
Applications and Benefits
- Vacuum coating is widely used in industries such as aerospace, automotive, electronics, and medical devices.
- The coatings provide enhanced properties, including improved hardness, wear resistance, corrosion resistance, and thermal stability.
- The process is environmentally friendly, as it minimizes waste and avoids harmful chemicals.
-
Process Control and Precision
- The vacuum coater allows for precise control over coating thickness, composition, and uniformity.
- Advanced monitoring systems ensure consistent quality and performance of the coatings.
- The ability to deposit nanoscale layers makes vacuum coating ideal for high-precision applications.
By combining these elements, a vacuum coater creates high-performance coatings that meet the demanding requirements of modern industries. The process is a testament to the integration of advanced engineering and material science, delivering solutions that enhance the durability and functionality of critical components.
Summary Table:
Key Component | Function |
---|---|
Vacuum Chamber | Provides a controlled, sub-atmospheric environment for coating deposition. |
Vacuum Obtaining System | Creates and maintains the vacuum using pumps and seals. |
Power Supply | Supplies energy for vaporization, ionization, and plasma generation. |
Process Gas Input System | Introduces reactive or inert gases to enhance the coating process. |
Water Cooling System | Prevents overheating of machine components. |
Ion Evaporation/Sputtering Source | Generates vaporized coating material for deposition. |
Ready to enhance your materials with precision coatings? Contact us today to learn more about vacuum coaters!