A vulcanizing machine , also known as a vulcanizer, is a specialized piece of equipment used to transform raw rubber into a durable, elastic material through a process called vulcanization. This process involves applying heat and pressure to rubber compounds, typically in the presence of sulfur or other curing agents, to create cross-links between polymer chains. The machine achieves this by using a hydraulic system to generate pressure and a heating medium (such as steam or heat transfer oil) to provide the necessary temperature. The result is a rubber product with enhanced mechanical properties, such as increased strength, elasticity, and resistance to wear and environmental factors.
Key Points Explained:
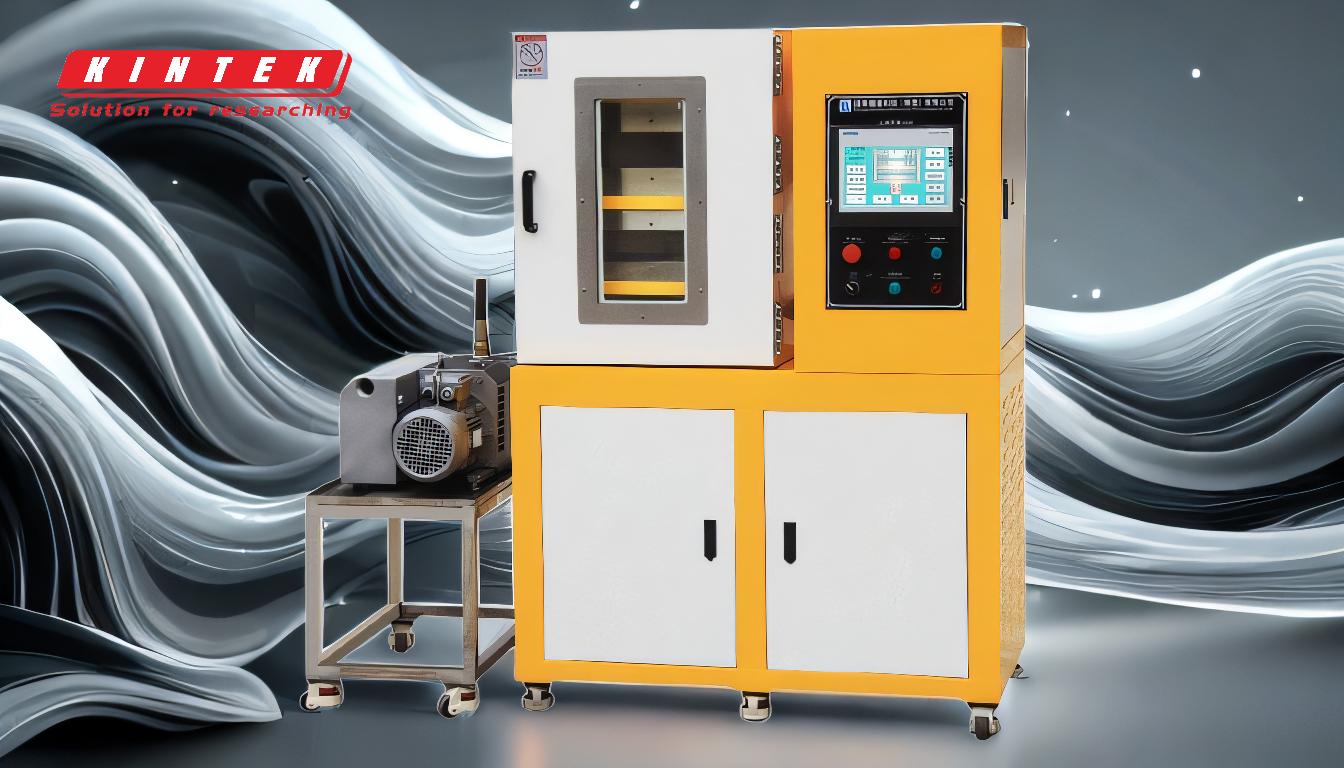
-
Purpose of Vulcanization:
- Vulcanization is a chemical process that improves the physical properties of rubber by introducing cross-links between polymer chains.
- This process makes rubber more durable, elastic, and resistant to heat, chemicals, and wear.
-
Components of a Vulcanizing Machine:
- Hydraulic System: Generates the pressure required for vulcanization. This system typically includes a hydraulic cylinder, pumps, and valves.
- Heating System: Provides the necessary heat for the vulcanization process. Common heating mediums include steam, heat transfer oil, or electric heating elements.
- Mold Plates: These are the surfaces that come into direct contact with the rubber compound. They are heated to the required temperature and pressed together to shape and cure the rubber.
-
Working Mechanism:
- Pressure Application: The hydraulic system applies pressure to the rubber compound, ensuring it fills the mold evenly and achieves the desired shape.
- Heat Application: The heating system raises the temperature of the mold plates, which in turn heats the rubber compound to the optimal vulcanization temperature.
- Curing Process: Under the combined action of heat and pressure, the rubber undergoes a chemical reaction (vulcanization), forming cross-links between polymer chains and resulting in a cured rubber product.
-
Types of Vulcanizing Machines:
- Hydraulic Hot Press Vulcanizers: These machines use hydraulic pressure and heat transfer oil or steam to vulcanize rubber. They are commonly used for manufacturing rubber products like seals, gaskets, and tires.
- Steam Vulcanizers: Utilize steam as the heating medium. They are often used in applications requiring uniform heating, such as in the production of rubber hoses and belts.
- Electric Vulcanizers: Use electric heating elements to provide heat. These are suitable for smaller-scale operations or where precise temperature control is required.
-
Advantages of Vulcanizing Machines:
- Enhanced Rubber Properties: Vulcanization significantly improves the mechanical and chemical properties of rubber, making it suitable for a wide range of industrial applications.
- Precision and Consistency: Modern vulcanizing machines offer precise control over temperature and pressure, ensuring consistent quality in the final product.
- Versatility: These machines can be used to produce a variety of rubber products, from simple seals to complex tire treads.
-
Applications of Vulcanized Rubber:
- Automotive Industry: Tires, seals, and gaskets.
- Construction Industry: Rubber hoses, belts, and vibration dampers.
- Consumer Goods: Footwear, gloves, and other rubber-based products.
-
Maintenance and Safety Considerations:
- Regular Maintenance: Ensuring the hydraulic and heating systems are functioning properly is crucial for consistent performance and longevity of the machine.
- Safety Measures: Operators should be trained to handle high-pressure and high-temperature equipment safely. Proper insulation and safety guards are essential to prevent accidents.
By understanding how a vulcanizing machine works, manufacturers can optimize the vulcanization process to produce high-quality rubber products tailored to specific industrial needs.
Summary Table:
Aspect | Details |
---|---|
Purpose | Improves rubber properties through vulcanization, making it durable and elastic. |
Key Components | Hydraulic system, heating system (steam, oil, or electric), and mold plates. |
Working Mechanism | Combines heat and pressure to create cross-links in rubber polymer chains. |
Types | Hydraulic hot press, steam, and electric vulcanizers. |
Advantages | Enhances rubber strength, elasticity, and resistance to wear and chemicals. |
Applications | Automotive (tires, seals), construction (hoses, belts), and consumer goods. |
Maintenance | Regular checks on hydraulic and heating systems for consistent performance. |
Discover how a vulcanizing machine can improve your rubber production— contact us today for expert advice!