Industrial furnaces are critical equipment in various industries, designed to generate and transfer heat for processes such as melting, refining, drying, or sintering materials. They operate through a combination of heat generation and transfer mechanisms, including radiation, convection, and conduction. Industrial furnaces are broadly categorized into electrical and fired types, with electrical furnaces using arc or high-frequency induction and fired furnaces relying on fuel combustion. The design of an industrial furnace typically includes a radiant section (firebox) for direct heat radiation and a convection section for additional heat recovery. Heat transfer fluids are used to measure and control the temperature, ensuring efficient and precise heating for industrial applications.
Key Points Explained:
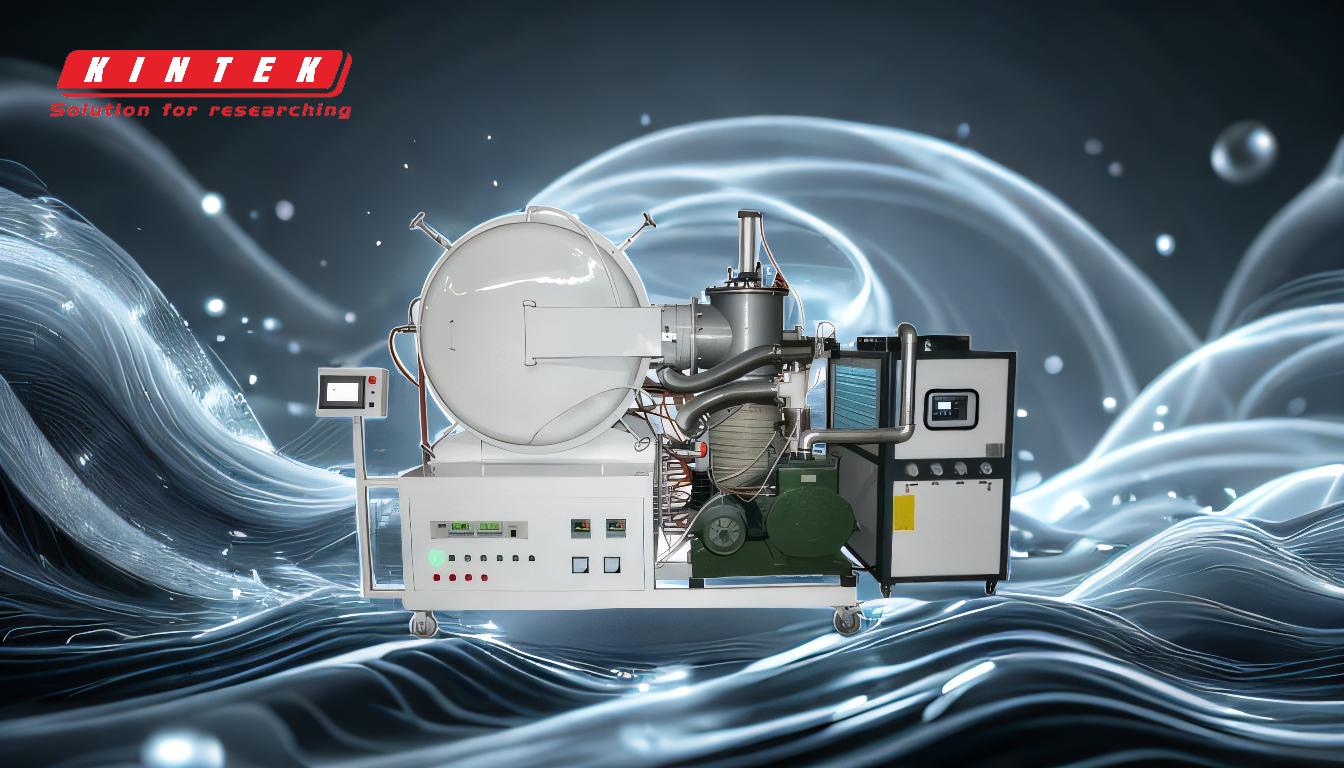
-
Types of Industrial Furnaces:
- Electrical Furnaces: These include arc furnaces and high-frequency induction furnaces. Arc furnaces are used for refining metals, while induction furnaces are ideal for melting metals. They are more expensive but environmentally friendly as they do not produce pollutants.
- Fired Furnaces: These rely on the combustion of fuels such as gas or oil to generate heat. They are widely used in industries like refineries, petrochemical plants, and chemical manufacturing due to their efficiency and cost-effectiveness.
-
Common Industrial Furnace Models:
- Gas Furnaces: Utilize natural gas or propane as fuel for combustion.
- Electric Furnaces: Use electricity for heating, offering precise temperature control.
- Oil Furnaces: Employ oil as a fuel source, often used in applications requiring high heat output.
-
Heat Transfer Mechanisms:
- Radiation: Heat radiates from burners to the material or fluid in tubes, primarily occurring in the radiant section (firebox) of the furnace.
- Convection: Heat is carried by gas or liquid flow, typically in the convection section above the firebox, where additional heat recovery occurs.
- Conduction: Heat transfers through solid surfaces, such as the walls of tubes, ensuring even distribution of heat.
-
Components of an Industrial Furnace:
- Radiant Section (Firebox): The area where burners generate heat, and direct radiation heats the tubes containing the material or fluid.
- Convection Section: Located above the firebox, this section recovers additional heat through convection, improving overall efficiency.
- Heat Transfer Fluid: Used to measure and control the temperature of the furnace, ensuring optimal heating conditions.
-
Applications of Industrial Furnaces:
- Metal Refining and Melting: Electrical furnaces, such as arc and induction furnaces, are commonly used in metalworking industries.
- Drying and Sintering: Fired furnaces are used for drying materials or sintering finished parts in industries like ceramics and manufacturing.
- Fluid Heating: Process furnaces are essential in refineries and chemical plants for heating fluids to specific temperatures.
-
Temperature Measurement and Control:
- The temperature of the heat transfer fluid is measured at the surface of the tubes on the "hot" side, where the highest degree of heat transfer occurs. This ensures accurate temperature control and efficient operation.
-
Advantages of Different Furnace Types:
- Electric Furnaces: Offer precise temperature control and are environmentally friendly, making them suitable for applications requiring high accuracy.
- Fired Furnaces: Provide high heat output and are cost-effective, making them ideal for large-scale industrial operations.
By understanding these key points, equipment and consumable purchasers can make informed decisions about the type of furnace best suited for their specific industrial needs, ensuring optimal performance and efficiency.
Summary Table:
Aspect | Details |
---|---|
Types | Electrical (arc, induction) and Fired (gas, oil) furnaces |
Heat Transfer | Radiation, Convection, Conduction |
Components | Radiant Section (Firebox), Convection Section, Heat Transfer Fluid |
Applications | Metal refining, drying, sintering, fluid heating |
Advantages | Electric: Precise control, eco-friendly; Fired: High heat, cost-effective |
Need help choosing the right industrial furnace for your needs? Contact our experts today for tailored solutions!