Hot Isostatic Pressing (HIP) is a manufacturing process that reduces porosity in materials by applying uniform heat and pressure from all directions. This process uses an inert gas, such as Argon, to pressurize a vessel containing the material, while simultaneously heating it to temperatures typically below the material's melting point. The combination of heat and pressure eliminates small gaps or pores within the material, leading to increased density and a more uniform composition. HIP is particularly beneficial for materials used in extreme environments, as it enhances mechanical properties, surface finish, and service life by removing internal defects like pores, cracks, and segregation.
Key Points Explained:
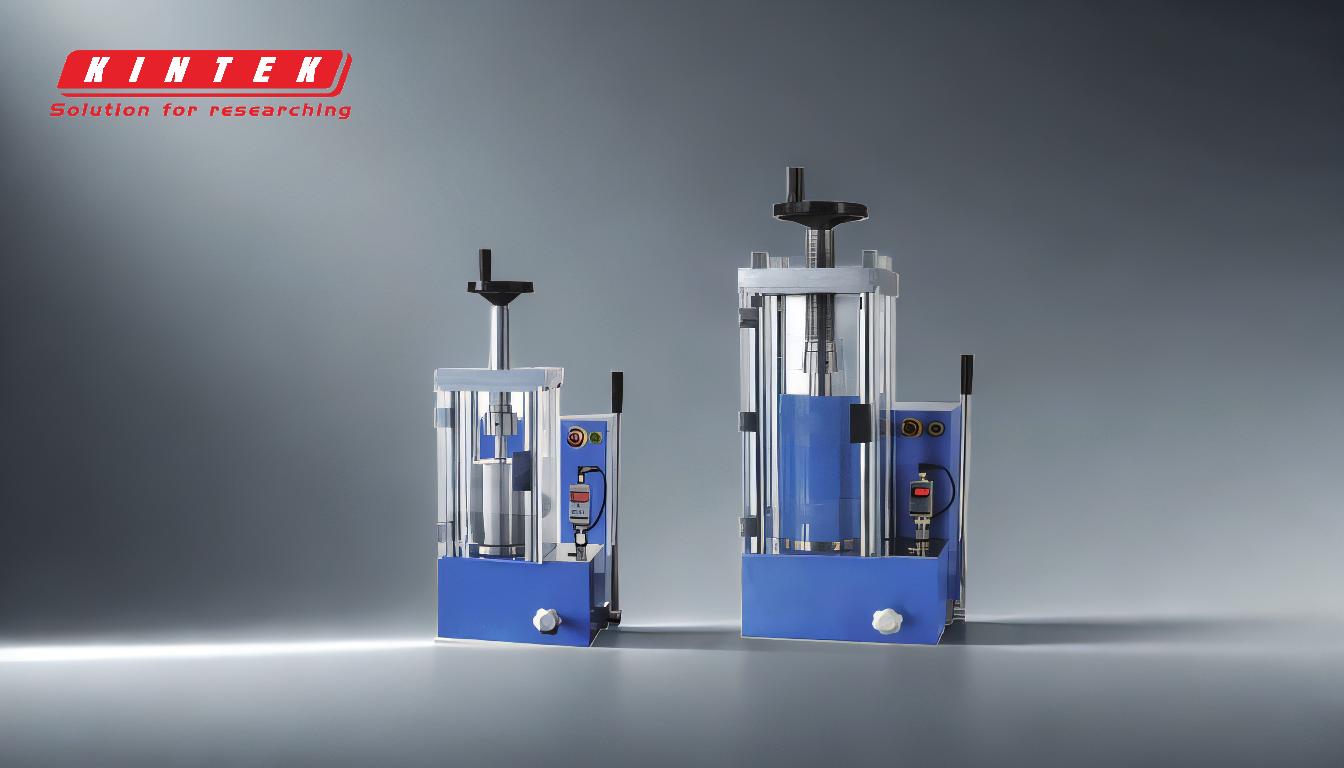
-
Uniform Application of Heat and Pressure:
- HIP applies heat and pressure uniformly from all directions using an inert gas like Argon. This uniform application ensures that the material is compressed evenly, which helps in closing pores and reducing porosity.
- The temperature used is typically below the melting point of the material, which prevents melting while still allowing the material to deform and fill in gaps.
-
Elimination of Porosity:
- The simultaneous application of heat and pressure causes the material to deform plastically, filling in small gaps or pores. This results in a denser material with fewer internal voids.
- Densities greater than 98% of full density are typical, and full density can be achieved with careful control of time, pressure, and temperature.
-
Mechanisms of Densification:
- HIP achieves densification through mechanisms such as bulk deformation, sintering, and creep. Creep, in particular, plays a significant role in the densification process by allowing the material to slowly deform under pressure and heat.
- These mechanisms work together to ensure that the material becomes more compact and uniform, reducing porosity and improving overall material properties.
-
Improvement of Material Properties:
- By eliminating internal porosity, HIP improves the consistency of mechanical properties such as tensile strength, impact strength, and ductility. This makes the material more reliable and durable.
- The process also improves the surface finish of the material, which can be crucial for applications where surface quality is important.
-
Applications in Extreme Environments:
- HIP is particularly valuable for materials used in extreme environments, such as power units and submarine oil pipelines. These applications require materials with high performance and stability, which HIP provides by eliminating internal defects like pores, cracks, and segregation.
- The process extends the service life of materials and can even rejuvenate castings by removing service-induced porosity.
-
Cost and Efficiency Benefits:
- HIP can salvage rejected castings and reduce quality assurance costs by improving the overall quality and reliability of materials.
- The process also allows for the production of complex shapes and large-sized compactions, which can be difficult or impossible to achieve with conventional molding processes.
-
Combination with Other Processes:
- HIP can be used in combination with other processes like Cold Isostatic Pressing (CIP) to further enhance material properties. CIP is often used first to compact the product, followed by sintering and then HIP to achieve full densification.
In summary, Hot Isostatic Pressing is a highly effective method for reducing porosity in materials by applying uniform heat and pressure. This process not only increases material density but also improves mechanical properties, surface finish, and service life, making it indispensable for high-performance applications in extreme environments.
Summary Table:
Aspect | Details |
---|---|
Process | Uniform heat and pressure applied using inert gas (e.g., Argon). |
Porosity Reduction | Eliminates pores, cracks, and voids, achieving >98% density. |
Densification Mechanisms | Bulk deformation, sintering, and creep. |
Material Improvements | Enhances tensile strength, impact strength, ductility, and surface finish. |
Applications | Ideal for extreme environments like power units and submarine pipelines. |
Cost Benefits | Salvages rejected castings and reduces quality assurance costs. |
Combination with CIP | Used with Cold Isostatic Pressing for full densification. |
Discover how Hot Isostatic Pressing can improve your materials—contact our experts today!