Hot pressing is a manufacturing process that combines heat and pressure to densify and shape materials, typically ceramics or metals, into near-theoretical density structures. It involves placing powdered material into a die, applying uniaxial pressure (10–30 MPa), and heating it to sintering temperatures simultaneously. This method accelerates densification, reduces processing time, and improves material properties compared to traditional cold pressing and sintering. The process includes steps such as charging the powder, vacuuming to remove impurities, heating to melt the powder, applying pressure to fuse the material, and cooling to solidify the final product. Hot pressing is particularly effective for producing high-density, high-performance materials with minimal defects.
Key Points Explained:
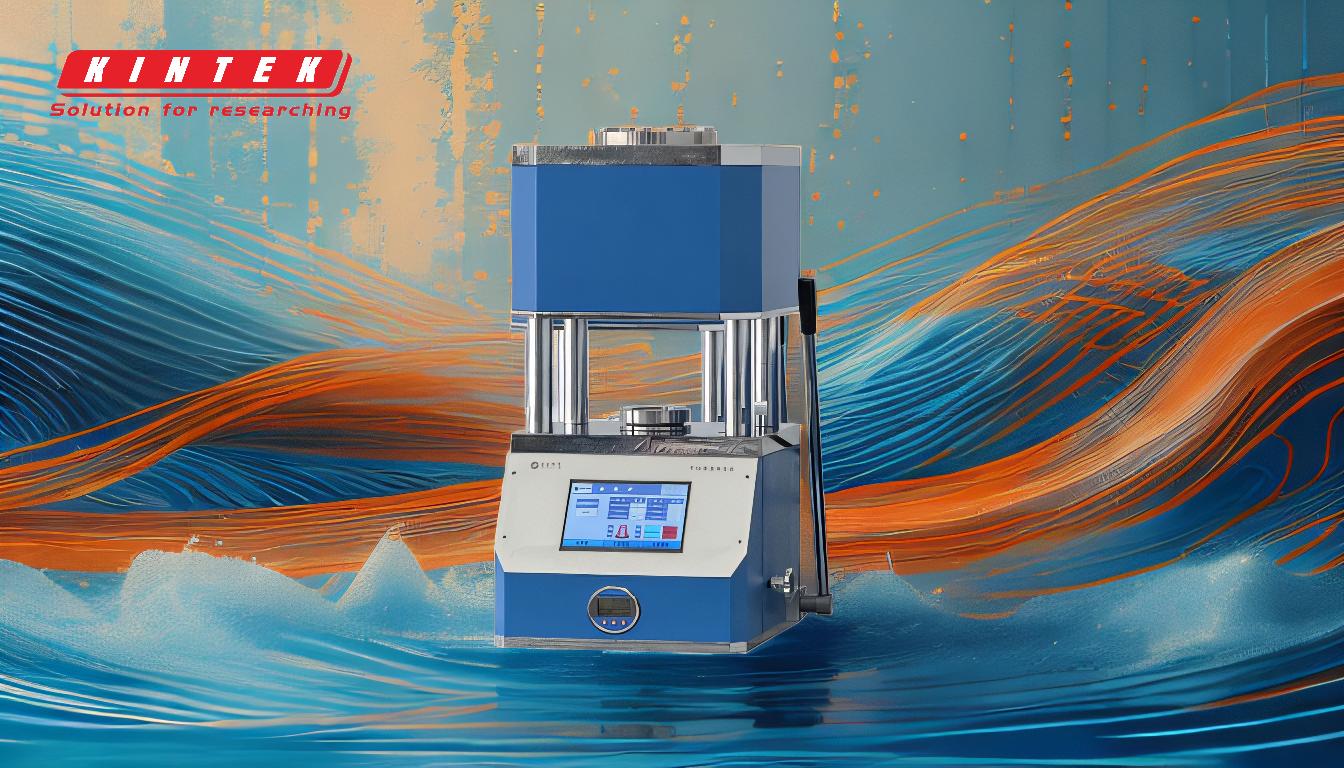
-
Simultaneous Application of Heat and Pressure:
- Hot pressing combines heat and pressure in a single step, unlike traditional methods where pressing and sintering are separate processes. This simultaneous application significantly reduces the time required for phase changes and alloy formation.
- The process involves placing powdered material into a graphite die and applying both heat and pressure at the same time. This ensures that the material densifies uniformly and reaches near-theoretical density.
-
Uniaxial Pressure:
- A uniaxial pressure of 10–30 MPa is applied through a simple-shaped die. This pressure helps in compacting the powder and increasing the densification rate.
- The applied pressure aids in reducing porosity and improving the mechanical properties of the final product, making it denser and stronger.
-
Steps Involved in Hot Pressing:
- Charging: The ceramic or metal powder is loaded into the furnace or die.
- Vacuuming: The furnace is evacuated to create a vacuum, removing gases and impurities that could otherwise cause defects in the final product.
- Heating: The temperature is raised to the sintering temperature, which melts the powder particles and allows them to bond.
- Pressurization: Pressure is applied to fuse the powder particles into a dense, solid structure.
- Cooling: The material is gradually cooled to room temperature to solidify the structure and prevent thermal stress.
-
Advantages Over Traditional Methods:
- Reduced Processing Time: By combining pressing and sintering, hot pressing significantly reduces the overall processing time compared to traditional cold pressing and sintering.
- Improved Material Properties: The simultaneous application of heat and pressure results in materials with higher density, better mechanical properties, and fewer defects.
- Near-Theoretical Density: Hot pressing allows the material to reach densities close to the theoretical maximum, which is difficult to achieve with other methods.
-
Applications:
- Hot pressing is widely used in the production of high-performance ceramics, advanced composites, and specialized metals. It is particularly useful in industries where materials with high strength, wear resistance, and thermal stability are required.
- Common applications include aerospace components, cutting tools, and electronic substrates.
-
Environmental Conditions:
- Hot pressing can be performed in a vacuum or under a positive pressure of inert gas. This environment prevents oxidation and other chemical reactions that could degrade the material quality.
- The use of a vacuum or inert gas also helps in removing any residual gases or impurities from the powder, further enhancing the quality of the final product.
-
Material Considerations:
- The choice of material for the die (typically graphite) is crucial as it must withstand high temperatures and pressures without deforming or reacting with the powder.
- The powder used must have a uniform particle size distribution to ensure even densification and avoid defects in the final product.
By understanding these key points, one can appreciate the efficiency and effectiveness of hot pressing in producing high-quality, dense materials with superior properties. This method is particularly advantageous for industries requiring materials with exceptional mechanical and thermal performance.
Summary Table:
Key Aspect | Details |
---|---|
Process | Combines heat and pressure to densify ceramics or metals. |
Pressure | Uniaxial pressure of 10–30 MPa applied. |
Steps | Charging, vacuuming, heating, pressurization, cooling. |
Advantages | Reduced processing time, improved material properties, near-theoretical density. |
Applications | Aerospace components, cutting tools, electronic substrates. |
Environment | Performed in vacuum or inert gas to prevent oxidation. |
Material Considerations | Graphite dies, uniform particle size distribution for powder. |
Discover how hot pressing can enhance your material production—contact us today for expert guidance!