Low-Pressure Chemical Vapor Deposition (LPCVD) is a specialized technique used in the semiconductor industry for depositing thin films with high uniformity and quality. Unlike traditional CVD, LPCVD operates at lower pressures and higher temperatures, which enhances gas diffusion and improves film properties such as uniformity, resistivity, and trench-filling capabilities. The process eliminates the need for carrier gases, reducing contamination and making it a preferred method for applications requiring precise and reproducible thin films.
Key Points Explained:
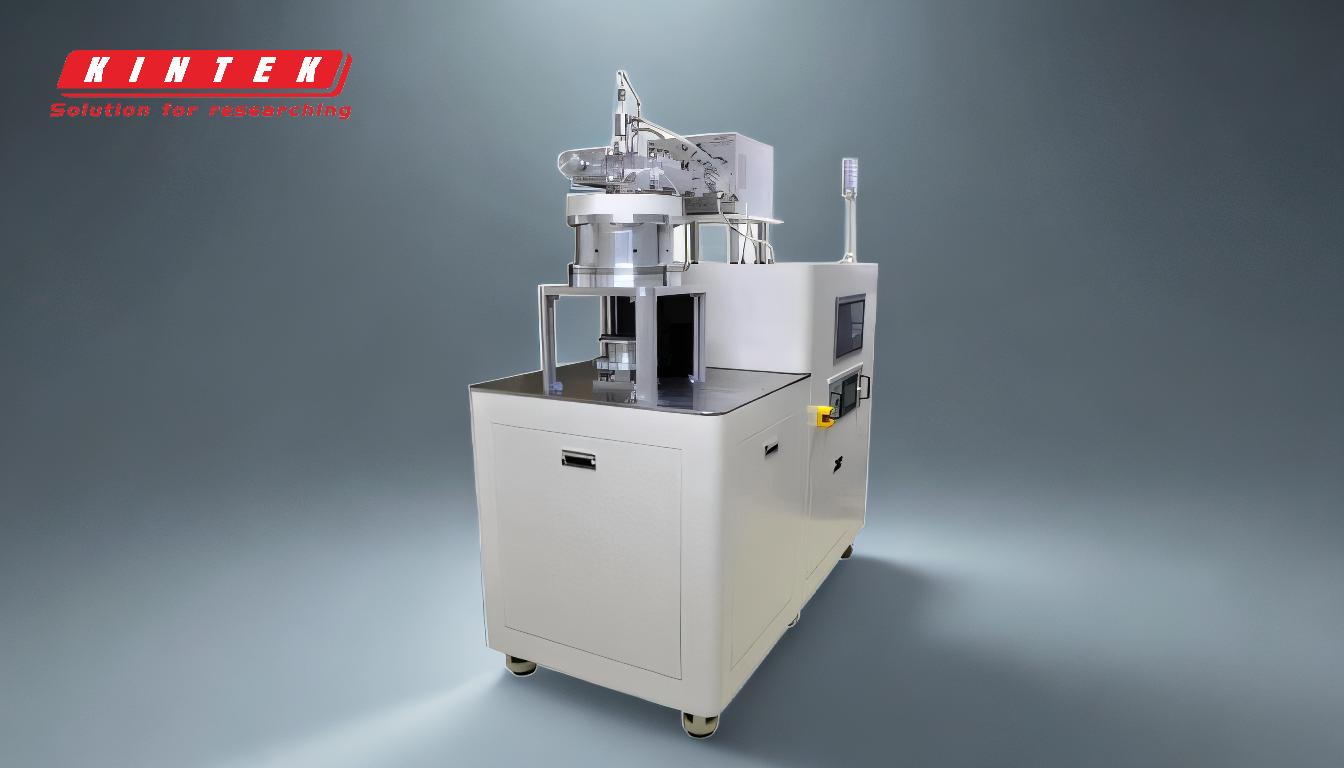
-
Fundamental Principle of LPCVD:
- LPCVD operates under low-pressure conditions, typically ranging from 0.1 to 10 Torr, combined with high thermal environments (400°C to 900°C). This setup enhances the gas diffusion coefficient and increases the mean free path of gas molecules within the reaction chamber.
- The low-pressure environment ensures faster gas transport rates, allowing for efficient removal of impurities and reaction by-products from the reaction zone.
-
Advantages of Low-Pressure Environment:
- Improved Film Uniformity: The low-pressure conditions ensure that gas molecules distribute more evenly across the substrate, leading to highly uniform film deposition.
- Enhanced Resistivity Uniformity: The consistent gas flow and reduced turbulence in the reaction chamber result in films with uniform electrical properties.
- Superior Trench Coverage: LPCVD excels at filling high-aspect-ratio trenches and vias, a critical requirement in semiconductor manufacturing.
-
Elimination of Carrier Gases:
- Unlike traditional CVD, LPCVD does not require carrier gases, which are often a source of particle contamination. This makes LPCVD a cleaner and more reliable process for depositing high-purity films.
-
Thermal and Chemical Reactions:
- The high thermal environment in LPCVD facilitates the chemical reactions necessary for film deposition. The heat breaks down volatile precursors, enabling them to react and deposit as a solid film on the substrate.
- The stoichiometry of the deposited films is highly controlled, resulting in dense and high-quality insulator films.
-
Applications in Semiconductor Industry:
- LPCVD is widely used for depositing thin films such as silicon dioxide (SiO₂), silicon nitride (Si₃N₄), and polysilicon. These films are essential for creating insulating layers, gate dielectrics, and other critical components in semiconductor devices.
- The reproducibility and uniformity of LPCVD films make it a preferred choice for advanced semiconductor manufacturing processes.
-
Process Control and Scalability:
- The thickness of the deposited films can be precisely controlled by adjusting the deposition time and power. This scalability ensures that LPCVD can meet the stringent requirements of modern semiconductor fabrication.
In summary, LPCVD is a highly efficient and reliable method for depositing thin films in semiconductor manufacturing. Its low-pressure, high-temperature environment ensures superior film quality, uniformity, and trench-filling capabilities, making it indispensable for advanced semiconductor applications.
Summary Table:
Aspect | Details |
---|---|
Pressure Range | 0.1 to 10 Torr |
Temperature Range | 400°C to 900°C |
Key Advantages | Improved film uniformity, enhanced resistivity, superior trench coverage, no carrier gases |
Applications | Silicon dioxide (SiO₂), silicon nitride (Si₃N₄), polysilicon deposition |
Process Control | Precise film thickness control via deposition time and power adjustments |
Unlock the potential of LPCVD for your semiconductor projects—contact our experts today!