Press forging and drop forging are two distinct metalworking processes used to shape metal into desired forms. While both methods involve the application of force to deform metal, they differ significantly in terms of the type of force applied, the speed of deformation, and the resulting material properties. Press forging uses a continuous, controlled force to shape the metal, while drop forging relies on the impact of a hammer or die to achieve the desired form. These differences influence the precision, surface finish, and mechanical properties of the final product. Below, we explore the key distinctions between these two forging techniques in detail.
Key Points Explained:
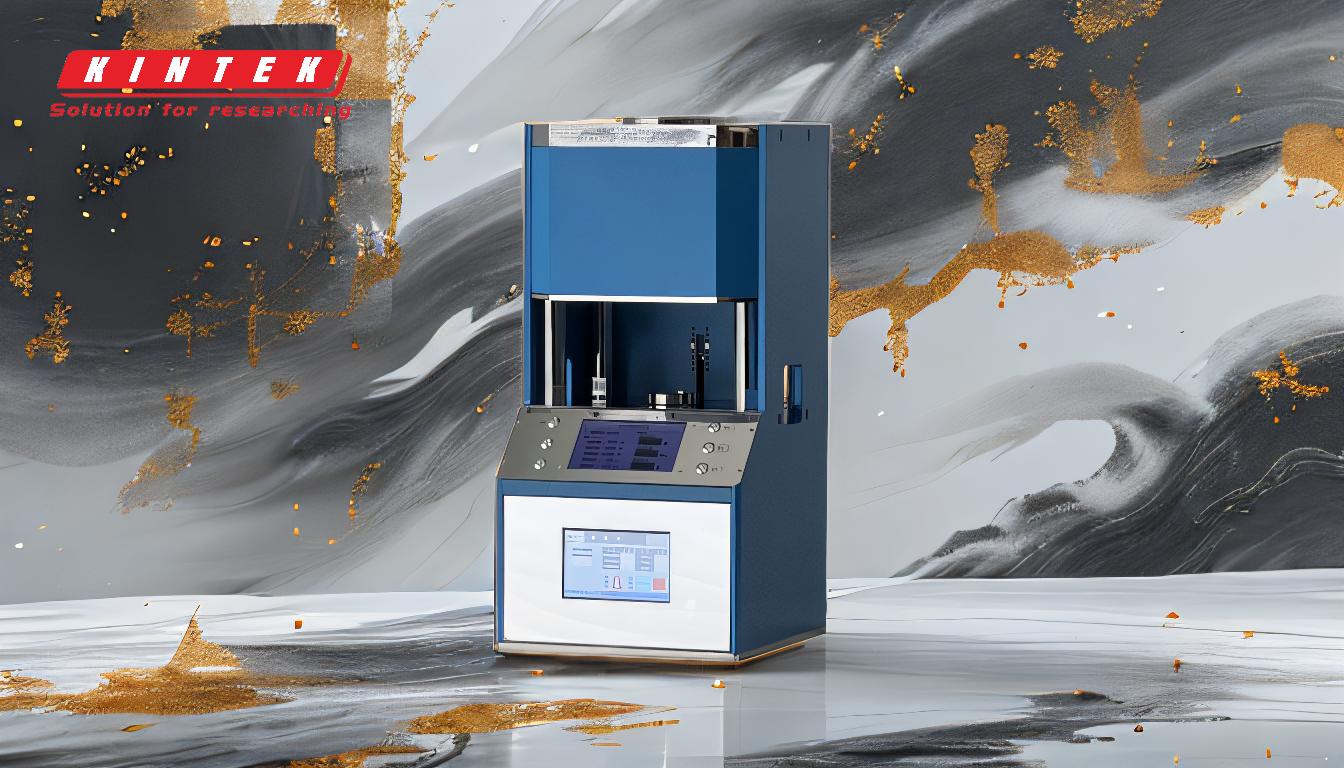
-
Type of Force Applied:
- Press Forging: In press forging, a hydraulic or mechanical press applies a continuous, steady force to the metal workpiece. This force is distributed evenly over a longer period, allowing for precise control over the deformation process.
- Drop Forging: Drop forging, on the other hand, uses a hammer or die that is dropped onto the metal workpiece. The force is applied in a sudden, high-impact manner, which results in rapid deformation.
-
Speed of Deformation:
- Press Forging: The deformation process in press forging is slower and more controlled. This allows for better accuracy and reduces the risk of defects such as cracks or voids in the final product.
- Drop Forging: Drop forging involves a much faster deformation process due to the high-impact nature of the force applied. While this can lead to quicker production times, it may also increase the likelihood of defects if not carefully managed.
-
Precision and Surface Finish:
- Press Forging: The controlled and continuous force in press forging results in a higher degree of precision and a smoother surface finish. This makes it suitable for applications where tight tolerances and high-quality finishes are required.
- Drop Forging: The rapid impact in drop forging can lead to a rougher surface finish and less precision compared to press forging. However, it is often sufficient for applications where surface finish is less critical.
-
Mechanical Properties:
- Press Forging: The slower deformation rate in press forging allows for better grain structure alignment, which can enhance the mechanical properties of the metal, such as strength and durability.
- Drop Forging: While drop forging can also produce strong and durable parts, the rapid deformation may result in a less uniform grain structure, potentially affecting the mechanical properties.
-
Applications:
- Press Forging: Press forging is commonly used for producing complex shapes and high-precision components, such as gears, crankshafts, and other critical parts in the automotive and aerospace industries.
- Drop Forging: Drop forging is often used for simpler shapes and larger components, such as tools, hardware, and structural parts, where precision and surface finish are less critical.
-
Equipment and Cost:
- Press Forging: The equipment used in press forging, such as hydraulic presses, is generally more expensive and requires more maintenance. However, the precision and quality of the final product can justify the higher costs for certain applications.
- Drop Forging: Drop forging equipment, such as hammers and dies, is typically less expensive and easier to maintain. This makes drop forging a more cost-effective option for high-volume production of simpler parts.
In summary, press forging and drop forging each have their own advantages and are suited to different types of applications. Press forging offers greater precision and control, making it ideal for high-quality, complex components, while drop forging is more cost-effective and suitable for simpler, high-volume production. Understanding these differences is crucial for selecting the appropriate forging method based on the specific requirements of the project.
Summary Table:
Aspect | Press Forging | Drop Forging |
---|---|---|
Type of Force Applied | Continuous, steady force (hydraulic/mechanical press) | Sudden, high-impact force (hammer or die) |
Speed of Deformation | Slower, controlled process | Faster, rapid deformation |
Precision & Finish | Higher precision, smoother surface finish | Rougher finish, less precision |
Mechanical Properties | Better grain structure alignment, enhanced strength and durability | Less uniform grain structure, potentially lower mechanical properties |
Applications | Complex shapes, high-precision parts (e.g., gears, crankshafts) | Simpler shapes, high-volume production (e.g., tools, hardware) |
Equipment & Cost | Higher cost, more maintenance (hydraulic presses) | Lower cost, easier maintenance (hammers and dies) |
Need help choosing the right forging method for your project? Contact our experts today!