Sintering is a critical process in materials science that involves heating powdered materials below their melting point to bond particles together, leading to densification and improved material properties. One of the most significant effects of sintering is its impact on grain size, which plays a crucial role in determining the mechanical, thermal, and electrical properties of the final product. During sintering, grains grow as particles bond and densify, influenced by factors such as temperature, time, and pressure. This grain growth can enhance material strength, durability, and conductivity, but excessive grain growth may lead to undesirable properties. Understanding how sintering affects grain size is essential for optimizing material performance in applications ranging from industrial components to advanced ceramics.
Key Points Explained:
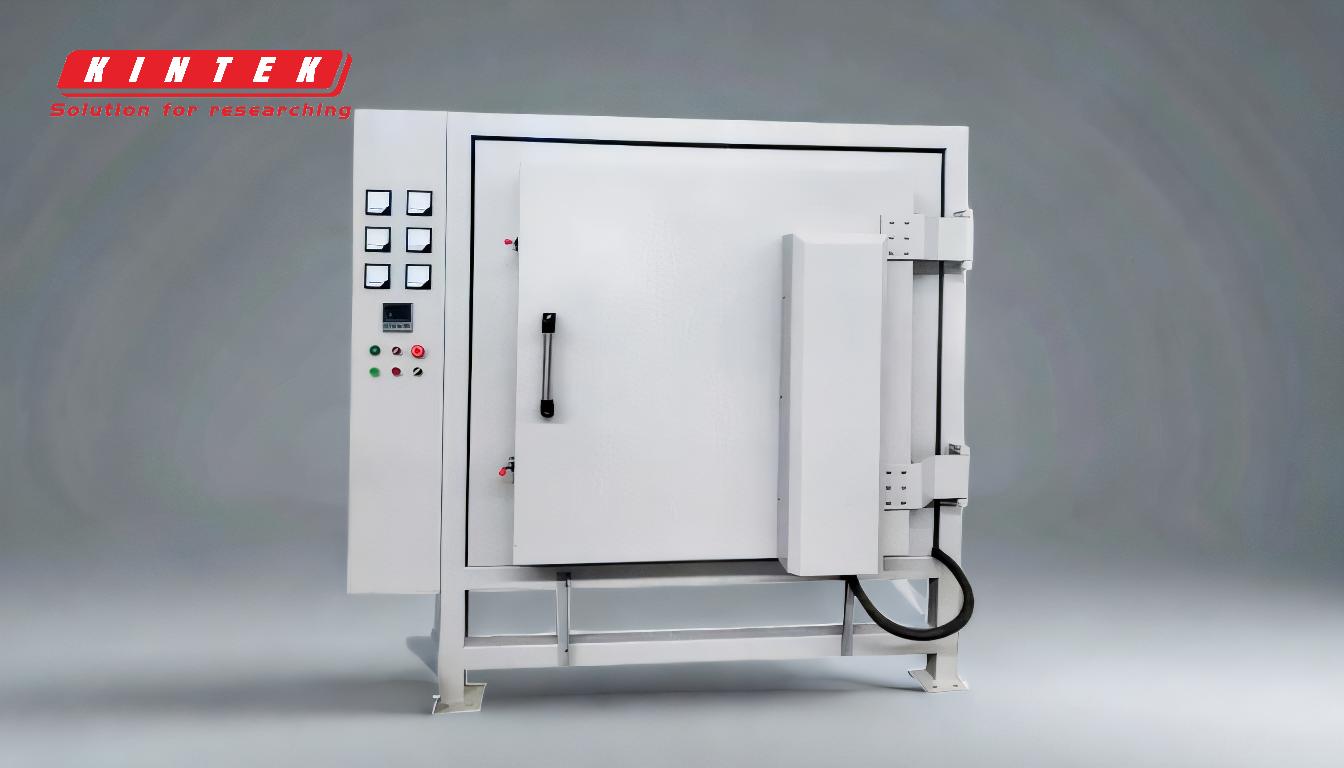
-
What is Sintering?
- Sintering is a process that combines powdered materials by applying heat and pressure without melting them.
- It is used to create dense, cohesive structures with improved mechanical, thermal, and electrical properties.
- Common applications include manufacturing bearings, jewelry, heat pipes, and shotgun shells.
-
How Sintering Affects Grain Size
- Grain Growth Mechanism: During sintering, particles bond and densify, leading to grain growth. This occurs as atoms diffuse across grain boundaries, causing smaller grains to merge into larger ones.
- Temperature and Time: Higher sintering temperatures and longer sintering times generally promote greater grain growth. However, excessive grain growth can lead to reduced material strength.
- Pressure and Density: Applied pressure during sintering can enhance densification and control grain size, resulting in a more uniform microstructure.
-
Impact of Grain Size on Material Properties
- Strength and Durability: Smaller grain sizes typically result in higher strength and hardness due to the Hall-Petch relationship, which states that smaller grains impede dislocation movement.
- Thermal and Electrical Conductivity: Larger grains can improve conductivity by reducing the number of grain boundaries, which act as barriers to electron and heat flow.
- Porosity and Corrosion Resistance: Sintering reduces surface porosity, which enhances corrosion resistance and tensile strength. However, excessive grain growth can lead to increased porosity at grain boundaries.
-
Controlling Grain Size During Sintering
- Optimizing Temperature and Time: Careful control of sintering temperature and duration is essential to achieve the desired grain size and material properties.
- Use of Additives: Certain additives can inhibit grain growth, allowing for finer grain structures and improved mechanical properties.
- Pressure-Assisted Sintering: Techniques like hot pressing or spark plasma sintering (SPS) can be used to control grain size and achieve high-density materials.
-
Trade-offs in Grain Size Optimization
- While smaller grains improve strength and hardness, they may reduce thermal and electrical conductivity.
- Larger grains can enhance conductivity but may compromise mechanical properties.
- The optimal grain size depends on the specific application and desired material performance.
-
Applications and Implications
- In ceramics, sintering is used to achieve high-density, fine-grained structures for applications requiring strength and durability.
- In metals, sintering is employed to produce components with controlled porosity and grain size, such as bearings and filters.
- Advanced sintering techniques, such as microwave sintering, offer precise control over grain size and microstructure.
By understanding how sintering affects grain size, manufacturers can tailor the process to achieve the desired material properties for specific applications. This knowledge is crucial for optimizing performance and ensuring the reliability of sintered components in various industries.
Summary Table:
Aspect | Impact of Sintering on Grain Size |
---|---|
Grain Growth Mechanism | Particles bond and densify, leading to grain growth as atoms diffuse across grain boundaries. |
Temperature and Time | Higher temperatures and longer times promote grain growth; excessive growth can reduce strength. |
Pressure and Density | Applied pressure enhances densification and controls grain size for a uniform microstructure. |
Strength and Durability | Smaller grains increase strength and hardness due to the Hall-Petch relationship. |
Conductivity | Larger grains improve thermal and electrical conductivity by reducing grain boundary barriers. |
Porosity and Corrosion | Sintering reduces porosity, enhancing corrosion resistance, but excessive grain growth may increase it. |
Control Methods | Optimize temperature, time, additives, and pressure-assisted techniques for desired grain size. |
Applications | Used in ceramics, metals, and advanced materials for strength, conductivity, and durability. |
Ready to optimize your sintering process? Contact our experts today for tailored solutions!