Sintering increases density by compacting and fusing powdered materials into a solid mass through the application of heat and pressure, without reaching the material's melting point. This process reduces porosity by promoting atomic diffusion across particle boundaries, which eliminates gaps between particles and creates a denser, more cohesive structure. The stages of sintering involve particle rearrangement, neck formation, and pore elimination, leading to improved mechanical strength and structural integrity. This method is widely used in ceramics, metals, and plastics manufacturing to produce durable and high-performance materials.
Key Points Explained:
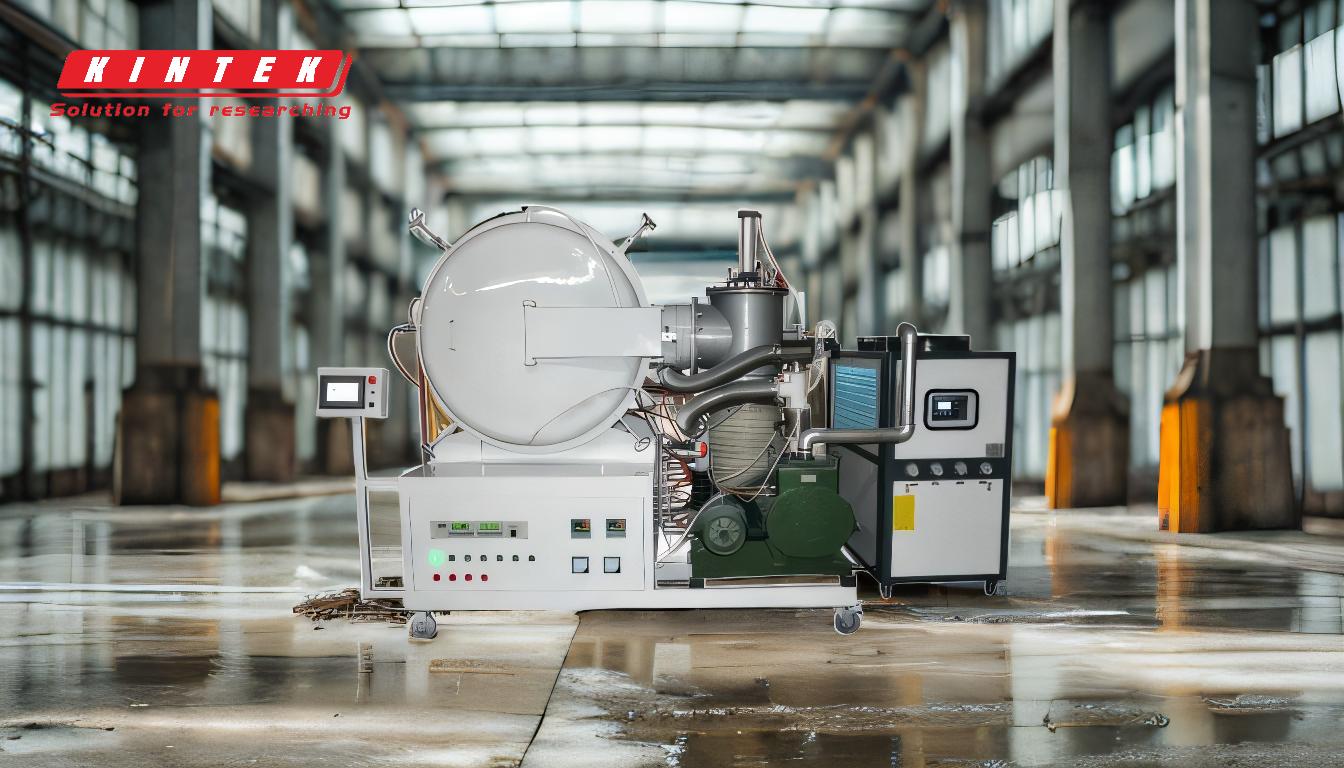
-
Definition of Sintering:
- Sintering is a process that transforms powdered materials into dense, solid bodies by applying heat and pressure below the material's melting point.
- It avoids liquefaction, ensuring the material retains its solid state while achieving densification.
-
Mechanism of Density Increase:
- Atomic Diffusion: At elevated temperatures, atoms in the powder particles diffuse across particle boundaries, fusing them together. This reduces the gaps (porosity) between particles.
- Particle Rearrangement: Under heat and pressure, particles rearrange into a more compact configuration, minimizing empty spaces.
- Neck Formation: As particles fuse, "necks" form at contact points, creating stronger bonds and further reducing porosity.
- Pore Elimination: Over time, smaller pores shrink and disappear, leading to a denser final product.
-
Stages of Sintering:
- Initial Stage: Particles begin to bond at contact points, forming necks.
- Intermediate Stage: Pores become interconnected, and the material begins to densify significantly.
- Final Stage: Pores are isolated and shrink, resulting in a nearly pore-free, dense structure.
-
Role of Heat and Pressure:
- Heat provides the energy needed for atomic diffusion, allowing particles to bond.
- Pressure compacts the powder, reducing the distance between particles and enhancing the diffusion process.
-
Applications of Sintering:
- Ceramics: Used to create strong, durable ceramic components.
- Metals: Commonly used in powder metallurgy to produce metal parts with high strength and precision.
- Plastics: Sintered plastics are used in applications requiring high durability and thermal resistance.
-
Benefits of Increased Density:
- Improved Mechanical Properties: Higher density leads to greater strength, hardness, and wear resistance.
- Enhanced Structural Integrity: Reduced porosity results in fewer weak points, making the material more reliable.
- Better Performance: Dense materials exhibit improved thermal and electrical conductivity.
-
Materials Suitable for Sintering:
- Materials with high melting points, such as tungsten and molybdenum, are ideal for sintering because the process avoids liquefaction.
- Ceramics and metals with fine powder particles are commonly used due to their ability to bond effectively under heat and pressure.
By understanding these key points, it becomes clear how sintering effectively increases density, transforming loose powders into robust, high-performance materials.
Summary Table:
Key Aspect | Description |
---|---|
Definition | Sintering transforms powdered materials into dense solids using heat and pressure. |
Mechanism | Atomic diffusion, particle rearrangement, neck formation, and pore elimination. |
Stages | Initial (neck formation), Intermediate (pore interconnection), Final (pore elimination). |
Role of Heat & Pressure | Heat enables atomic diffusion; pressure compacts particles for densification. |
Applications | Ceramics, metals, and plastics for durable, high-performance materials. |
Benefits | Improved strength, structural integrity, and thermal/electrical conductivity. |
Suitable Materials | High-melting-point materials like tungsten, molybdenum, ceramics, and metals. |
Discover how sintering can enhance your material performance—contact our experts today!