Sintering temperature plays a critical role in determining the final particle size of materials, particularly in ceramics and powdered metals. At higher temperatures, particles undergo densification and grain growth due to increased atomic diffusion and material transfer. This process is driven by pressure changes and free energy differences across particle surfaces, especially when particle sizes are small (radius of curvature less than a few microns). Fine-grained materials are often preferred in ceramic technologies because they exhibit enhanced mechanical properties and better control over microstructure. However, excessive sintering temperatures can lead to undesirable grain growth, reducing material performance. Understanding the balance between temperature and particle size is essential for optimizing material properties.
Key Points Explained:
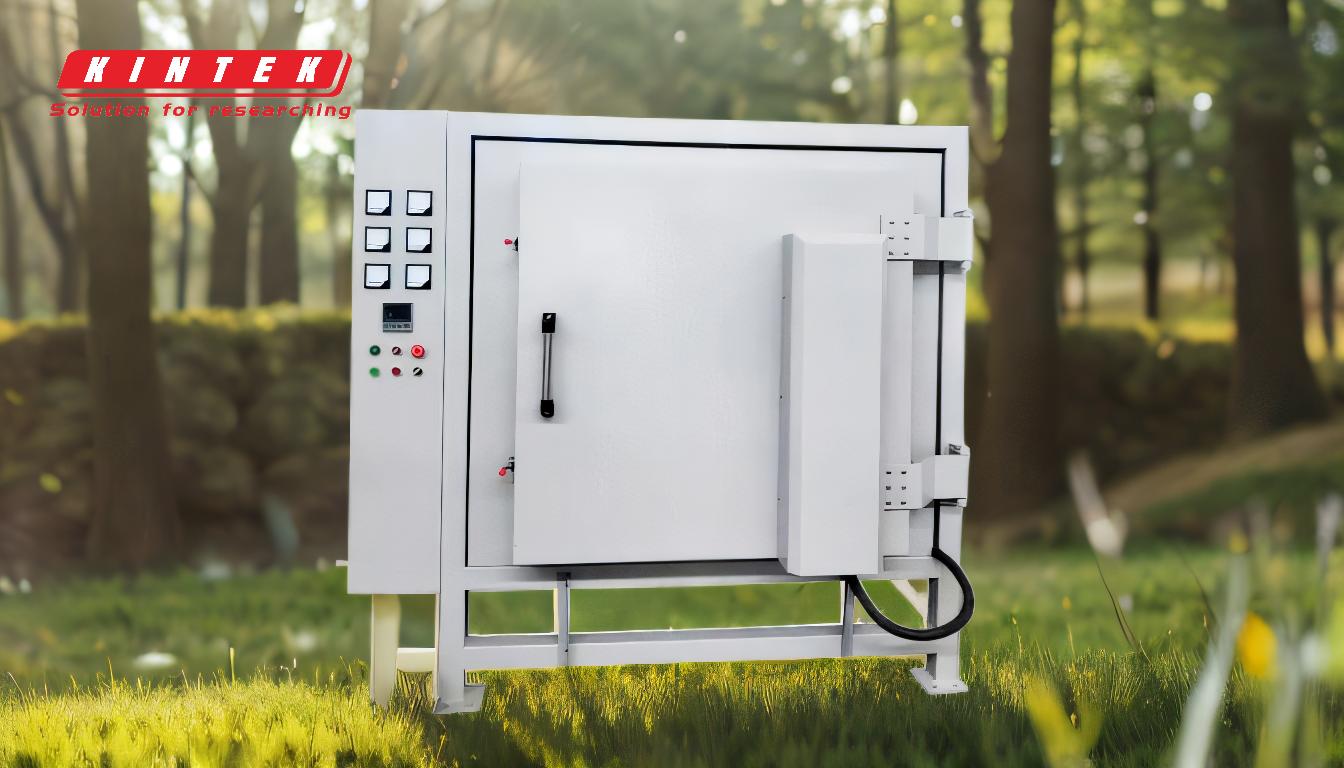
-
Material Transfer Mechanisms at High Temperatures:
- At elevated sintering temperatures, atomic diffusion becomes more active, facilitating material transfer between particles.
- Pressure changes and free energy differences across particle surfaces drive this transfer, especially in fine-grained materials where the radius of curvature is small (less than a few microns).
- These mechanisms lead to densification and particle coalescence, reducing porosity and increasing particle size.
-
Grain Growth and Its Implications:
- Higher sintering temperatures promote grain growth, where smaller grains merge to form larger ones.
- While some grain growth is necessary for densification, excessive growth can degrade material properties such as strength and toughness.
- Fine-grained materials are preferred in many applications because they offer better mechanical properties and microstructural control.
-
Role of Particle Size in Sintering:
- Smaller particles have higher surface energy due to their larger surface area-to-volume ratio, making them more susceptible to sintering at lower temperatures.
- As sintering progresses, particles coalesce, and the average particle size increases.
- The initial particle size distribution significantly influences the final microstructure and properties of the sintered material.
-
Optimal Sintering Temperature:
- The sintering temperature must be carefully controlled to achieve the desired balance between densification and grain growth.
- Too low a temperature may result in incomplete sintering, leaving excessive porosity.
- Too high a temperature can cause rapid grain growth, compromising material performance.
-
Applications in Ceramic Technologies:
- Fine-grained materials are widely used in ceramic technologies due to their superior mechanical properties and ability to form dense, uniform microstructures.
- The sintering temperature is a critical parameter in manufacturing processes such as powder metallurgy and advanced ceramics, where precise control over particle size and microstructure is essential.
By understanding the relationship between sintering temperature and particle size, manufacturers can optimize processing conditions to achieve materials with tailored properties for specific applications.
Summary Table:
Key Factor | Impact on Sintering |
---|---|
Temperature | Higher temperatures increase atomic diffusion, leading to densification and grain growth. |
Particle Size | Smaller particles sinter faster due to higher surface energy and surface area-to-volume ratio. |
Grain Growth | Excessive grain growth at high temperatures can degrade material strength and toughness. |
Optimal Temperature | Balancing temperature ensures densification without excessive grain growth. |
Applications | Fine-grained materials are preferred in ceramics for superior mechanical properties. |
Optimize your sintering process for better material performance—contact our experts today!