Sintering is a critical process in metallurgy and materials science, used to create solid objects from powdered metals without reaching their melting points. The process involves several stages, including powder compaction, controlled heating in a sintering furnace, and cooling. During sintering, atoms diffuse across particle boundaries, leading to bonding and densification. This method is widely used for metals, ceramics, and plastics, offering advantages such as material efficiency, complex shape formation, and improved mechanical properties. The sintering furnace plays a central role in maintaining precise temperature and atmosphere control to ensure optimal results.
Key Points Explained:
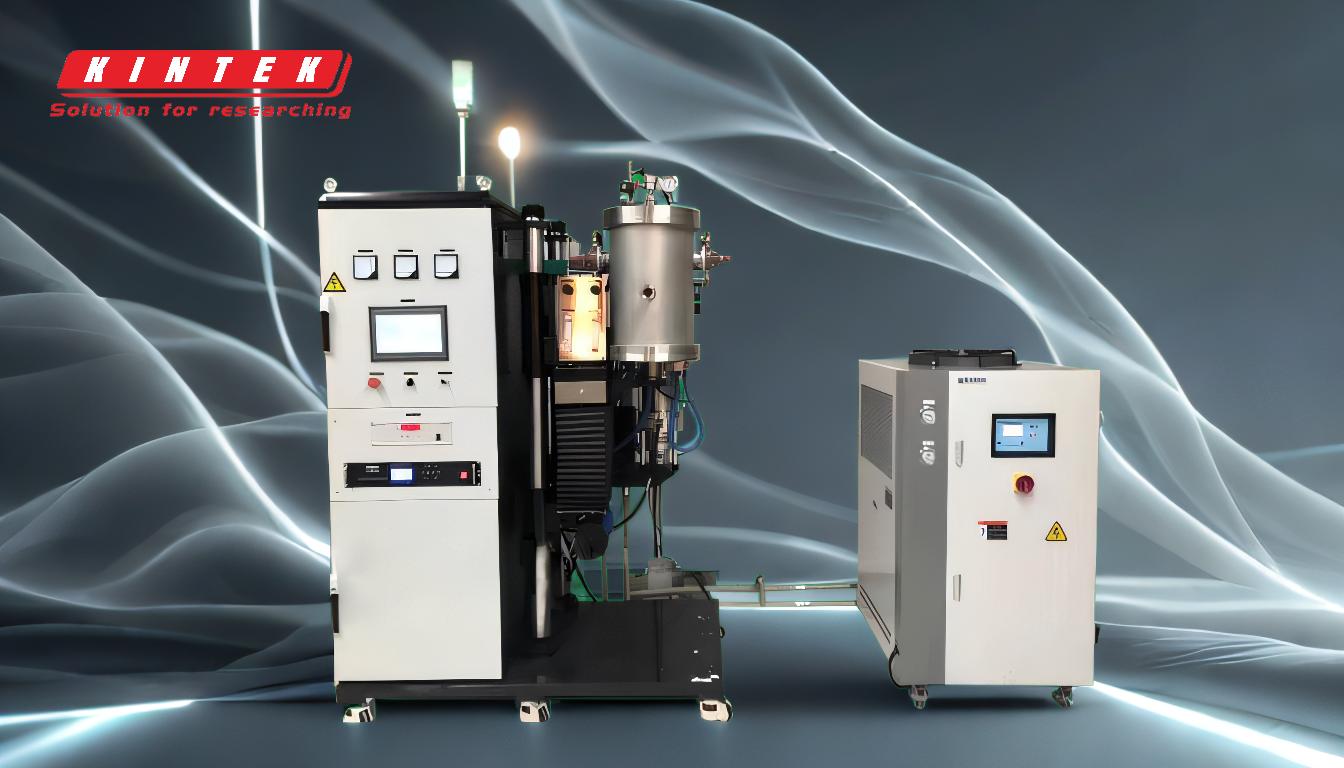
-
Definition and Purpose of Sintering:
- Sintering is a thermal process that fuses powdered materials into a solid mass without melting them.
- It is used to create dense, cohesive structures with improved mechanical properties, such as strength and durability.
- Common applications include the production of metal parts, ceramics, and sintered plastics.
-
Stages of the Sintering Process:
- Powder Preparation: The raw material is processed into fine powder, often mixed with additives like binders or coupling agents to enhance properties.
- Compaction: The powder is pressed into a specific shape using high pressure to eliminate voids and ensure uniformity.
- Heating in a Sintering Furnace: The compacted material is heated in a sintering furnace at temperatures below the melting point. This allows atoms to diffuse, forming bonds between particles and leading to densification.
- Cooling: The sintered product is cooled to solidify into a rigid structure, often with slight shrinkage accounted for in the design.
-
Role of the Sintering Furnace:
- The sintering furnace is critical for maintaining precise temperature control and atmosphere conditions.
- Heating methods include resistance heating elements or induction heating systems.
- Atmosphere control ensures optimal sintering conditions, such as preventing oxidation or facilitating reduction reactions.
-
Mechanisms of Sintering:
- Solid-State Diffusion: Atoms move across particle boundaries, leading to neck formation and bonding.
- Particle Bonding: Particles adhere to each other, reducing porosity and increasing density.
- Densification: The material becomes more compact and cohesive as voids are eliminated.
-
Advantages of Sintering:
- Material Efficiency: Minimal waste compared to traditional machining processes.
- Complex Shapes: Ability to produce intricate geometries that are difficult to achieve with other methods.
- Improved Properties: Enhanced mechanical, thermal, and electrical properties due to controlled microstructure.
-
Applications of Sintering:
- Metals: Used in the production of gears, bearings, and structural components.
- Ceramics: Essential for creating high-strength, wear-resistant components.
- Plastics: Used to produce porous filters and other specialized parts.
By understanding the sintering process and the role of the sintering furnace, manufacturers can optimize their production techniques to achieve high-quality, durable products with tailored properties.
Summary Table:
Aspect | Details |
---|---|
Process Stages | Powder Preparation → Compaction → Heating → Cooling |
Key Mechanisms | Solid-State Diffusion, Particle Bonding, Densification |
Advantages | Material Efficiency, Complex Shapes, Improved Mechanical Properties |
Applications | Gears, Bearings, Structural Components, Ceramics, Porous Filters |
Role of Sintering Furnace | Precise Temperature Control, Atmosphere Regulation, Optimal Bonding Conditions |
Ready to optimize your metal fabrication process? Contact our experts today for tailored sintering solutions!