The PVD sputtering process is a widely used thin-film deposition technique that involves the ejection of atoms or molecules from a target material through bombardment by high-energy ions, typically argon ions. These ejected atoms travel through a vacuum chamber and condense onto a substrate to form a thin, uniform film. The process begins with the generation of plasma, which contains argon ions and electrons. These ions are accelerated toward the target material, causing atoms to be sputtered off. The sputtered atoms then travel through the chamber and deposit onto the substrate, creating a thin film. This method is highly controllable and is used in various industries, including semiconductors, optics, and decorative coatings.
Key Points Explained:
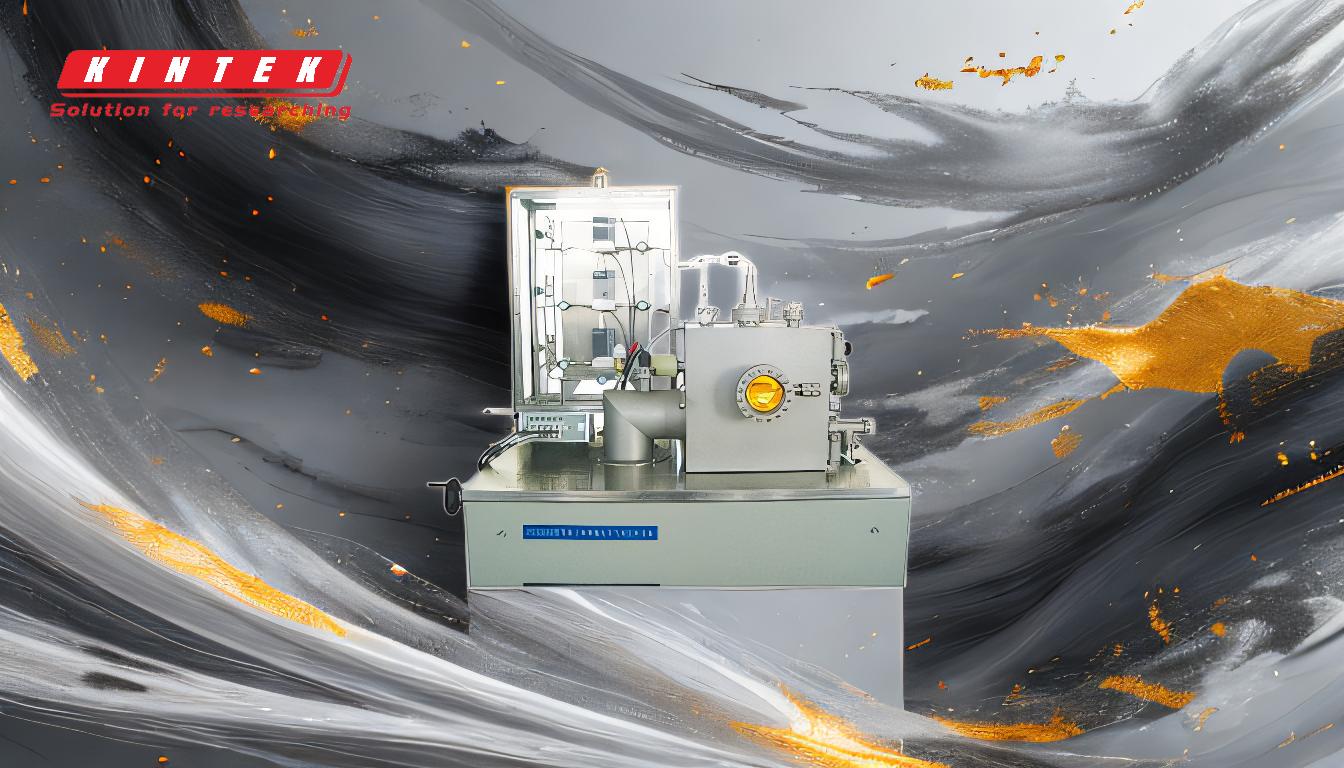
-
Introduction to PVD Sputtering:
- PVD (Physical Vapor Deposition) sputtering is a process used to deposit thin films of material onto a substrate.
- It is a vacuum-based technique where atoms or molecules are ejected from a target material and deposited onto a substrate.
-
Generation of Plasma:
- The process begins with the generation of plasma inside a vacuum chamber.
- Plasma is created by ionizing a gas, typically argon, which results in a mixture of argon ions and electrons.
- This plasma is essential for the sputtering process as it provides the high-energy ions needed to bombard the target material.
-
Bombardment of the Target Material:
- High-energy argon ions from the plasma are accelerated toward the target material.
- When these ions strike the target, they transfer their energy to the atoms of the target material.
- This energy transfer causes atoms or molecules to be ejected from the target surface, a process known as sputtering.
-
Transport of Sputtered Atoms:
- The ejected atoms or molecules travel through the vacuum chamber.
- The vacuum environment ensures that the sputtered atoms travel in a straight line without colliding with gas molecules, which could otherwise alter their path and reduce the quality of the deposited film.
-
Deposition on the Substrate:
- The sputtered atoms eventually reach the substrate, where they condense and form a thin film.
- The substrate is typically positioned opposite the target material to ensure uniform deposition.
- The thickness and properties of the film can be controlled by adjusting parameters such as the power applied to the plasma, the pressure in the chamber, and the distance between the target and the substrate.
-
Advantages of PVD Sputtering:
- Precision: The process allows for precise control over the thickness and composition of the deposited film.
- Versatility: It can be used to deposit a wide range of materials, including metals, alloys, and ceramics.
- Uniformity: The vacuum environment and controlled parameters ensure a uniform and consistent film deposition.
- Adhesion: The high-energy process results in strong adhesion of the film to the substrate.
-
Applications of PVD Sputtering:
- Semiconductors: Used in the fabrication of integrated circuits and other electronic components.
- Optics: Applied in the production of anti-reflective coatings, mirrors, and optical filters.
- Decorative Coatings: Used to create durable and aesthetically pleasing finishes on consumer products.
- Hard Coatings: Applied to tools and components to improve wear resistance and durability.
-
Challenges and Considerations:
- Cost: The equipment and vacuum environment required for PVD sputtering can be expensive.
- Complexity: The process requires precise control over various parameters, which can be complex and requires skilled operators.
- Material Limitations: While versatile, not all materials can be easily sputtered, and some may require specialized conditions or targets.
In summary, PVD sputtering is a highly controlled and versatile thin-film deposition technique that involves the ejection of atoms from a target material through high-energy ion bombardment. The process is widely used in various industries due to its precision, uniformity, and ability to deposit a wide range of materials. However, it also comes with challenges such as cost and complexity, which need to be considered when selecting this method for specific applications.
Summary Table:
Aspect | Details |
---|---|
Process Overview | Ejection of atoms from a target material via high-energy ion bombardment. |
Key Steps | Plasma generation, target bombardment, atom transport, and film deposition. |
Advantages | Precision, versatility, uniformity, and strong adhesion. |
Applications | Semiconductors, optics, decorative coatings, and hard coatings. |
Challenges | High cost, process complexity, and material limitations. |
Discover how PVD sputtering can enhance your manufacturing process—contact our experts today!