The sputtering process is a widely used technique for depositing thin films of materials onto substrates. It involves creating a vacuum in a reaction chamber, introducing an inert gas like argon, and ionizing the gas to form a plasma. High-energy ions from the plasma bombard a target material, causing atoms to be ejected and deposited onto a substrate, forming a thin film. This process is highly controllable and can be used to deposit a wide range of materials with precise thickness and uniformity. The key steps include creating a vacuum, introducing and ionizing the gas, generating a plasma, and accelerating ions to sputter target atoms onto the substrate.
Key Points Explained:
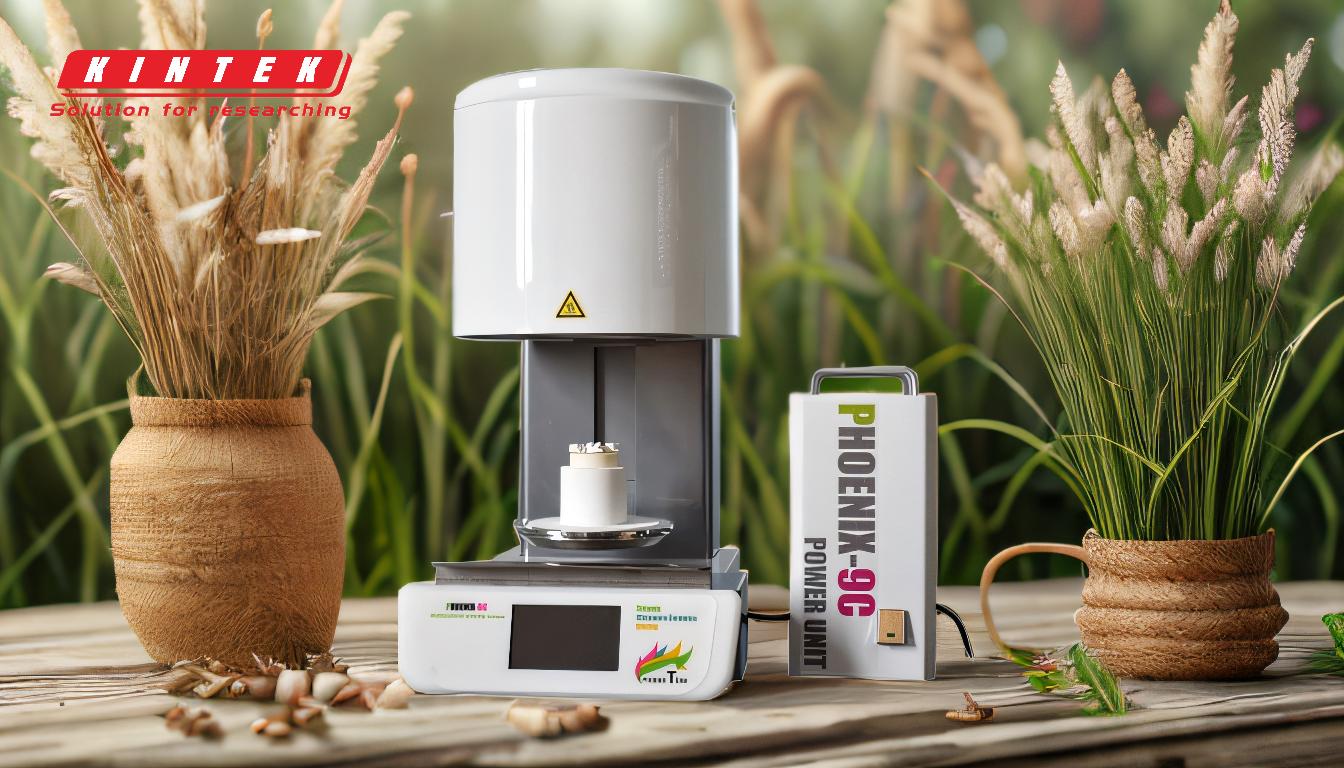
-
Creating a Vacuum in the Chamber:
- The first step in the sputtering process is to create a vacuum within the reaction chamber. This involves reducing the internal pressure to around 1 Pa (0.0000145 psi) to eliminate moisture and impurities. A vacuum environment is crucial because it prevents contamination from residual gases and ensures a clean surface for deposition. The vacuum also allows for better control over the sputtering process by minimizing unwanted reactions.
-
Introducing an Inert Gas:
- Once a vacuum is established, an inert gas, typically argon, is introduced into the chamber. Argon is chosen because it is chemically inert, meaning it does not react with the target material or the substrate. The gas is introduced at a controlled pressure, usually in the range of 10-1 to 10-3 mbar. This low-pressure environment is essential for maintaining the stability of the plasma that will be generated in the next steps.
-
Generating a Plasma:
- A high voltage (typically 3-5 kV) is applied across the chamber to ionize the argon gas, creating a plasma. The plasma consists of positively charged argon ions and free electrons. The ionization process is often enhanced by the presence of a magnetic field, which helps to confine the plasma and increase the density of ions. This step is critical because the plasma is the source of the high-energy ions that will be used to sputter the target material.
-
Accelerating Ions Towards the Target:
- The target material, which is the source of the atoms to be deposited, is negatively charged (cathode). The positively charged argon ions in the plasma are attracted to the negatively charged target. When these ions collide with the target, they transfer their kinetic energy to the target atoms. This energy transfer is sufficient to dislodge atoms from the target surface, a process known as sputtering.
-
Ejection and Deposition of Target Atoms:
- The sputtered atoms are ejected from the target surface in the form of neutral particles. These particles traverse the vacuum chamber and are transported to the substrate. The substrate is typically positioned opposite the target, and the sputtered atoms condense on its surface, forming a thin film. The deposition process is highly controlled, allowing for precise thickness and uniformity of the film.
-
Formation of a Thin Film:
- The sputtered atoms that reach the substrate adhere to its surface, forming a thin film. The film's properties, such as thickness, uniformity, and adhesion, are influenced by various factors, including the energy of the sputtered atoms, the substrate temperature, and the pressure within the chamber. The substrate may be heated to temperatures ranging from 150°C to 750°C, depending on the desired properties of the coating. This heating helps to improve the adhesion and quality of the deposited film.
-
Role of Magnetic Fields:
- In some sputtering systems, a magnetic field is used to enhance the ionization process and confine the plasma around the target. This is known as magnetron sputtering. The magnetic field increases the density of the plasma, leading to a higher rate of ion bombardment on the target. This results in a more efficient sputtering process and allows for higher deposition rates.
-
Control and Optimization:
- The sputtering process is highly controllable, with various parameters that can be adjusted to optimize the deposition. These parameters include the voltage applied, the pressure of the inert gas, the magnetic field strength, and the substrate temperature. By carefully controlling these variables, it is possible to deposit thin films with specific properties, such as electrical conductivity, optical transparency, or mechanical strength.
-
Applications of Sputtering:
- Sputtering is used in a wide range of applications, including the manufacture of semiconductors, optical coatings, and thin-film solar cells. It is also used in the production of hard coatings for tools and decorative coatings for consumer products. The ability to deposit a wide variety of materials with precise control makes sputtering a versatile and valuable technique in modern manufacturing and research.
In summary, the sputtering process is a complex but highly controlled method for depositing thin films of materials onto substrates. It involves creating a vacuum, introducing an inert gas, generating a plasma, and using high-energy ions to sputter atoms from a target material onto a substrate. The process is influenced by various parameters, including voltage, pressure, magnetic fields, and substrate temperature, which can be adjusted to achieve the desired film properties. Sputtering is widely used in industries ranging from electronics to optics, making it a critical technology in modern manufacturing.
Summary Table:
Step | Description |
---|---|
1. Create a Vacuum | Reduce chamber pressure to ~1 Pa to eliminate impurities and ensure clean deposition. |
2. Introduce Inert Gas | Add argon gas at 10-1 to 10-3 mbar to maintain plasma stability. |
3. Generate Plasma | Apply 3-5 kV to ionize argon gas, creating a plasma of ions and electrons. |
4. Accelerate Ions | Positively charged ions bombard the negatively charged target material. |
5. Eject Target Atoms | Target atoms are sputtered and deposited onto the substrate. |
6. Form Thin Film | Sputtered atoms condense on the substrate, forming a uniform thin film. |
7. Use Magnetic Fields | Magnetic fields enhance plasma density and sputtering efficiency (magnetron sputtering). |
8. Optimize Parameters | Adjust voltage, pressure, magnetic field, and substrate temperature for desired film properties. |
9. Applications | Used in semiconductors, optical coatings, solar cells, and hard coatings. |
Discover how sputtering can revolutionize your thin film applications—contact our experts today!