Vacuum arc melting (VAM) is a specialized process used to produce high-purity metals and alloys with minimal contamination. It involves melting a consumable electrode in a vacuum environment using an electric arc. The process is particularly useful for refining metals that are reactive or prone to oxidation. Key aspects of vacuum arc melting include the use of radiation for heating, proper spacing of workpieces, and addressing challenges like surface roughness, inclusions, and volatile elements. This method ensures the production of high-quality ingots with controlled microstructure and composition.
Key Points Explained:
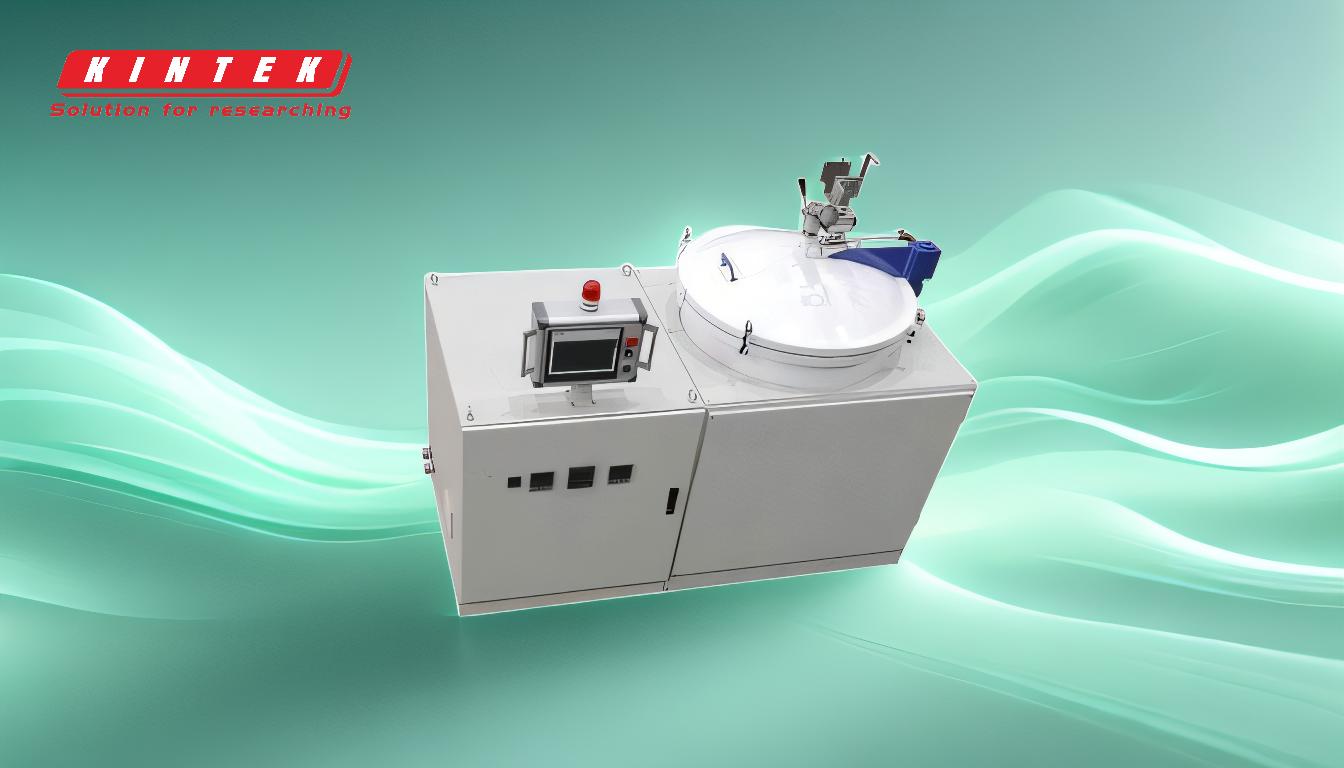
-
Principle of Vacuum Arc Melting:
- Vacuum arc melting operates by creating an electric arc between a consumable electrode and a water-cooled copper mold in a vacuum environment. The arc generates intense heat, melting the electrode and allowing the molten metal to drip into the mold, where it solidifies into an ingot.
- The vacuum environment prevents contamination from atmospheric gases, ensuring high-purity metal production. This is especially important for reactive metals like titanium, zirconium, and tantalum.
-
Role of Radiation in Heating:
- Heating in a vacuum furnace, including a vacuum arc melting furnace, is primarily achieved through radiation. Unlike convection or conduction, radiation does not require a medium and is highly effective in a vacuum.
- Proper spacing of workpieces within the furnace is critical to ensure uniform heating and avoid temperature gradients that could lead to defects in the final product.
-
Challenges in the Process:
- Surface Roughness and Porosity: The molten metal splash during the arc melting process can result in a rough and porous surface on the remelted ingot. This necessitates surface peeling or machining before further processing.
- Inclusions and Volatile Elements: The surface of the ingot may contain high levels of inclusions and volatile elements, which must be removed to ensure the material's integrity.
- Desulfurization Limitation: Unlike some other refining processes, vacuum arc melting does not include a desulfurization step. Therefore, the sulfur content of the consumable electrode must be controlled beforehand to avoid compromising the final product's quality.
-
Advantages of Vacuum Arc Melting:
- Produces high-purity metals with minimal contamination.
- Allows precise control over the microstructure and composition of the alloy.
- Suitable for melting reactive and refractory metals that are difficult to process in conventional furnaces.
-
Applications:
- Vacuum arc melting is widely used in industries requiring high-performance materials, such as aerospace, medical implants, and nuclear technology. It is particularly valuable for producing superalloys, titanium alloys, and other advanced materials.
By addressing these key points, vacuum arc melting ensures the production of high-quality metals and alloys with exceptional properties, making it a critical process in advanced manufacturing.
Summary Table:
Aspect | Details |
---|---|
Principle | Electric arc melts consumable electrode in a vacuum, forming high-purity ingots. |
Heating Mechanism | Radiation ensures uniform heating in a vacuum environment. |
Challenges | Surface roughness, inclusions, volatile elements, and no desulfurization. |
Advantages | High-purity metals, controlled microstructure, ideal for reactive alloys. |
Applications | Aerospace, medical implants, nuclear technology, and advanced materials. |
Discover how vacuum arc melting can enhance your material production—contact our experts today for more details!