The rotation speed of a rotary kiln typically ranges from 0.5 to 5 rpm, depending on the specific application and design requirements. Most kilns operate between 1 to 3 rpm, ensuring smooth operation and even heating, which is critical for stable performance. However, modern cement plant kilns can rotate faster, at 4 to 5 rpm, to optimize material flow and processing efficiency. The rotation speed is carefully controlled to balance factors such as retention time, material flow rate, and heat distribution, ensuring optimal calcination or other thermal processes.
Key Points Explained:
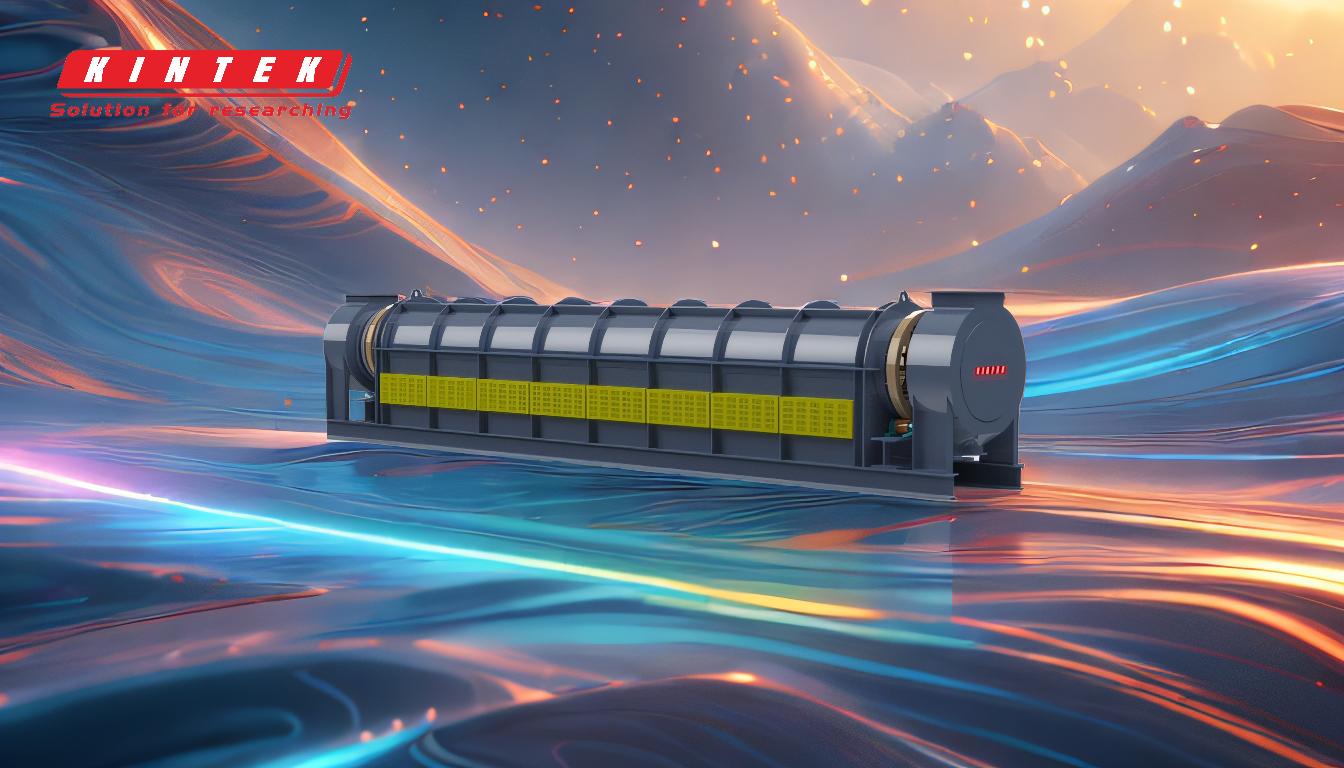
-
Typical Rotation Speed Range:
- Rotary kilns generally rotate at speeds between 0.5 to 5 rpm, with most operating in the 1 to 3 rpm range.
- This slow rotation ensures even heating and smooth operation, which are essential for achieving consistent product quality and stable machine performance.
-
Faster Rotation in Modern Cement Kilns:
- Modern cement plant kilns often operate at higher speeds, ranging from 4 to 5 rpm.
- This increased speed is designed to optimize material flow through the kiln, improving processing efficiency and throughput.
-
Factors Influencing Rotation Speed:
- Retention Time: The time materials spend in the kiln is directly affected by rotation speed. Slower speeds allow for longer retention times, which may be necessary for certain chemical or thermal processes.
- Material Flow Rate: Rotation speed influences how quickly materials move through the kiln. Faster speeds increase flow rates, which can enhance productivity but must be balanced with heat distribution requirements.
- Heat Distribution: Even heating is critical for processes like calcination. The rotation speed must ensure that materials are uniformly exposed to heat sources to achieve the desired chemical or physical transformations.
-
Operational Efficiency and Control:
- The rotation speed is one of several key operational parameters, including inclination angle, temperature, and bed depth, that determine the kiln's performance.
- Proper control of these parameters ensures efficient operation, minimizes energy consumption, and maximizes output quality.
-
Design Considerations:
- The rotation speed is influenced by the material's properties, such as particle size distribution, bulk density, and thermal conductivity.
- These factors affect how the material behaves in the kiln and how the kiln must be designed to achieve the desired process outcomes.
-
Application-Specific Variations:
- Different industries and processes may require specific rotation speeds. For example:
- Cement production often uses higher speeds (4–5 rpm) to maximize throughput.
- Other industries, such as those processing minerals or chemicals, may use slower speeds (1–3 rpm) to ensure thorough heating and reaction.
- Different industries and processes may require specific rotation speeds. For example:
-
Impact on Material Flow:
- The speed of material flow through the kiln is proportional to the rotation speed. Faster rotation speeds result in quicker material movement, which can be beneficial for high-capacity operations but may require adjustments to heating patterns to maintain quality.
By understanding these key points, equipment and consumable purchasers can make informed decisions about rotary kiln specifications, ensuring that the chosen equipment meets their operational and production needs.
Summary Table:
Aspect | Details |
---|---|
Typical Speed Range | 0.5–5 rpm, with most kilns operating at 1–3 rpm. |
Cement Kiln Speeds | Modern cement kilns operate at 4–5 rpm for enhanced efficiency. |
Key Influencing Factors | Retention time, material flow rate, and heat distribution. |
Design Considerations | Particle size, bulk density, and thermal conductivity affect speed choice. |
Applications | Cement production (4–5 rpm); minerals/chemicals (1–3 rpm). |
Need help selecting the right rotary kiln for your application? Contact our experts today!