Creating high pressure in a laboratory setting is a critical process for various scientific experiments and industrial applications. High pressure can be achieved through mechanical, hydraulic, or pneumatic systems, each tailored to specific requirements. Among these, hydraulic systems, such as the hydraulic hot press, are widely used due to their ability to generate immense force with precision. This process involves the use of hydraulic fluid, pistons, and cylinders to amplify pressure, enabling controlled and reproducible conditions. Understanding the principles and equipment involved is essential for achieving desired experimental outcomes.
Key Points Explained:
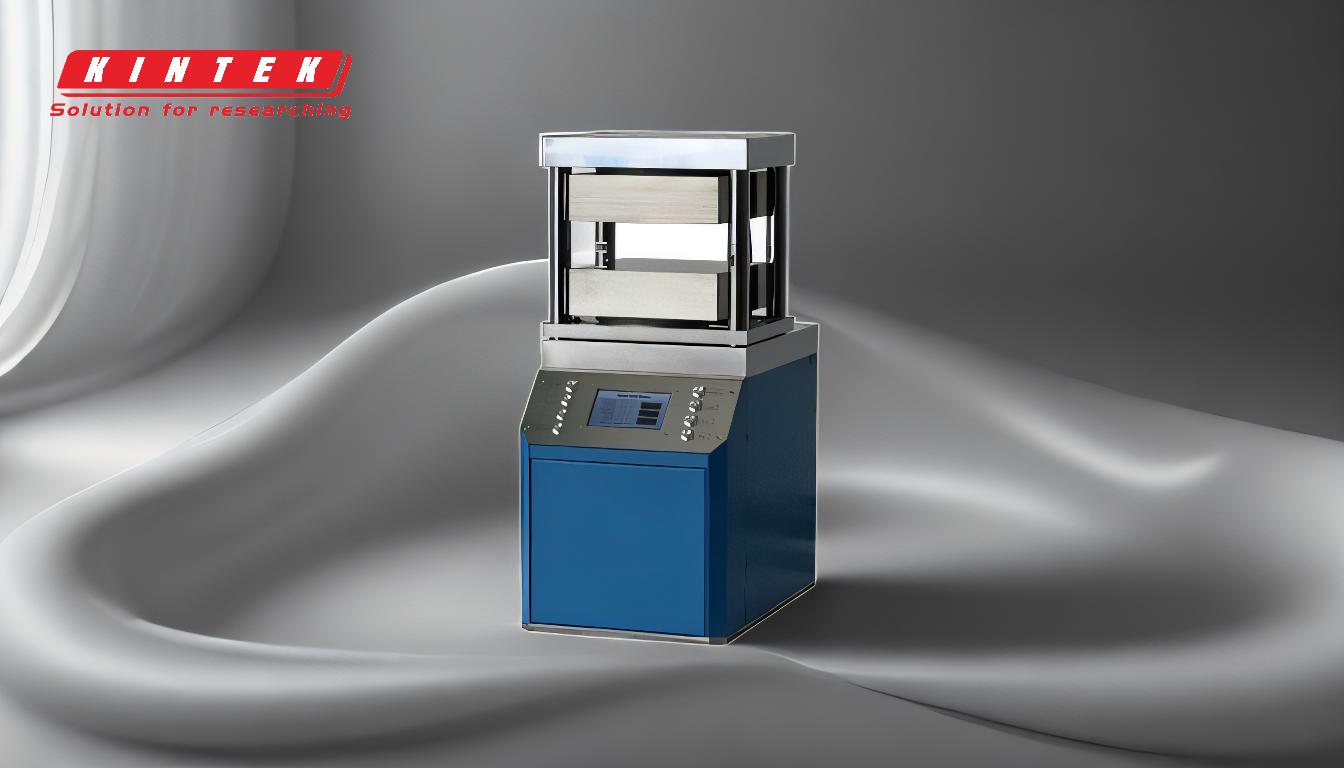
-
Principles of High-Pressure Generation
- High pressure is created by applying force over a small area, as defined by the formula ( P = F/A ), where ( P ) is pressure, ( F ) is force, and ( A ) is area.
- In laboratories, this is often achieved using mechanical or hydraulic systems that amplify force through levers, pistons, or fluid dynamics.
- Hydraulic systems, like the hydraulic hot press, are particularly effective because they use incompressible fluids to transmit force uniformly, resulting in precise and high-pressure outputs.
-
Hydraulic Systems in Laboratories
- Hydraulic systems consist of a pump, hydraulic fluid, cylinders, and pistons. The pump pressurizes the fluid, which then transfers the force to the piston, creating high pressure.
- The hydraulic hot press is a common example, used in applications like material synthesis, compaction, and testing. It can generate pressures up to several thousand psi (pounds per square inch).
- These systems are preferred for their ability to maintain consistent pressure over extended periods, which is crucial for experiments requiring stability.
-
Components of a Hydraulic Hot Press
- Hydraulic Pump: Generates the initial pressure by compressing the hydraulic fluid.
- Cylinder and Piston: The cylinder houses the piston, which moves under the pressure of the hydraulic fluid, applying force to the sample.
- Pressure Gauge: Monitors the pressure levels to ensure accuracy and safety.
- Heating Elements (in hot presses): Combine pressure with high temperatures for processes like sintering or molding.
-
Applications of High-Pressure Systems
- Material Synthesis: High pressure is used to create new materials, such as synthetic diamonds or advanced ceramics.
- Compression Testing: Evaluates the strength and durability of materials under extreme conditions.
- Chemical Reactions: Some reactions require high pressure to proceed, such as polymerization or catalysis.
- Sample Preparation: High-pressure systems are used to prepare samples for analysis, ensuring uniformity and consistency.
-
Safety Considerations
- High-pressure systems must be designed with safety features, such as pressure relief valves and fail-safes, to prevent accidents.
- Regular maintenance and inspection of hydraulic components are essential to avoid leaks or system failures.
- Operators should be trained in proper handling and emergency procedures to mitigate risks.
-
Advantages of Hydraulic Systems
- High Force Output: Hydraulic systems can generate significantly higher forces compared to mechanical systems.
- Precision Control: Pressure can be finely adjusted and maintained, ensuring reproducibility.
- Versatility: Suitable for a wide range of applications, from material testing to chemical synthesis.
-
Limitations and Alternatives
- Hydraulic systems require regular maintenance and can be complex to operate.
- Alternatives include pneumatic systems (using compressed air) and mechanical presses, though these may not achieve the same pressure levels.
- For ultra-high-pressure applications, diamond anvil cells are used, capable of reaching pressures in the gigapascal range.
By understanding the principles and components of high-pressure systems, particularly hydraulic systems like the hydraulic hot press, laboratories can effectively create and control high-pressure environments for a variety of scientific and industrial purposes.
Summary Table:
Aspect | Details |
---|---|
Principles | Force applied over a small area (P = F/A). Hydraulic systems amplify force. |
Key Components | Hydraulic pump, fluid, cylinder, piston, pressure gauge, heating elements. |
Applications | Material synthesis, compression testing, chemical reactions, sample prep. |
Advantages | High force output, precision control, versatility. |
Safety Considerations | Pressure relief valves, regular maintenance, operator training. |
Ready to enhance your lab's high-pressure capabilities? Contact us today to learn more about hydraulic systems!