Industrial furnaces are designed to achieve extremely high temperatures, often exceeding 1800°C, depending on their type and application. Tube furnaces and muffle furnaces, for instance, are commonly used in industrial and laboratory settings and can reach temperatures as high as 1800°C. These high temperatures are essential for processes such as material processing, heat treatment, and chemical reactions. The ability to maintain such high temperatures is critical for industries like ceramics, metallurgy, and materials science. Below, we explore the key aspects of industrial furnace temperatures in detail.
Key Points Explained:
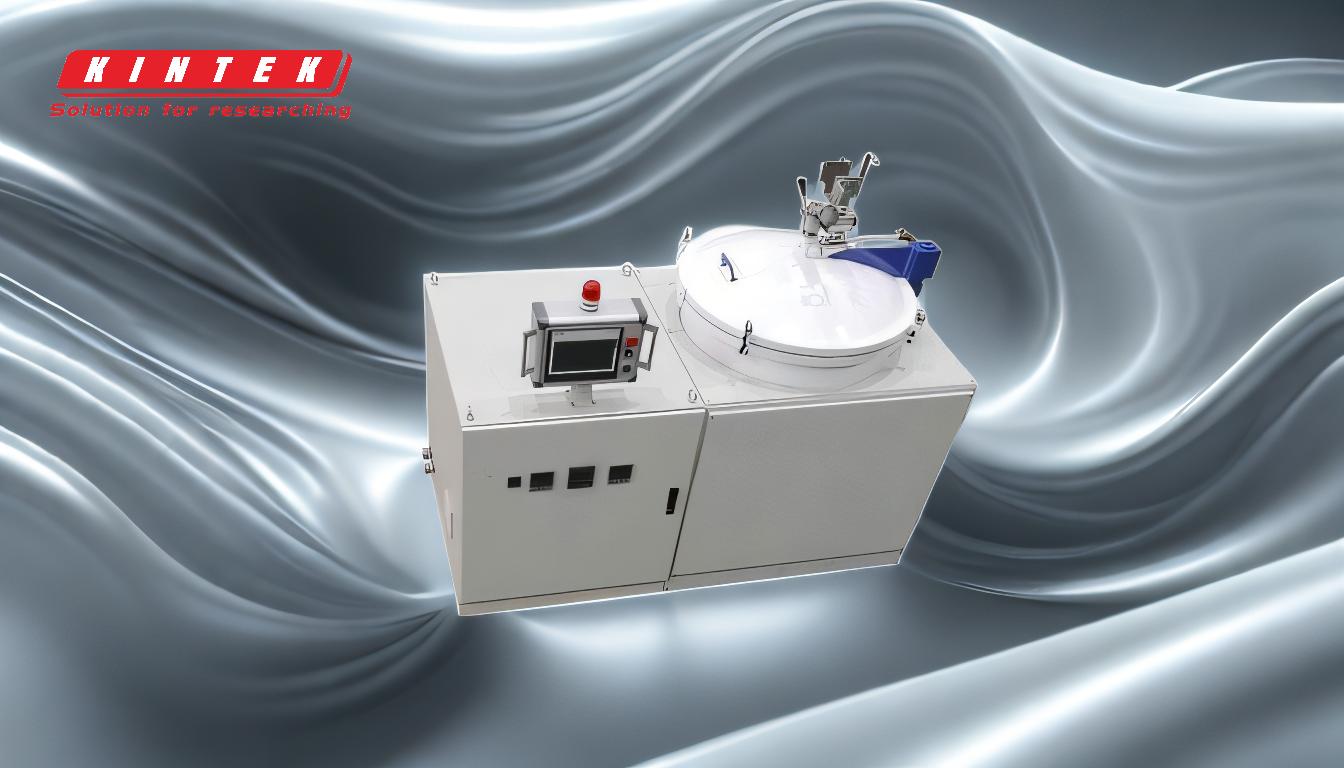
-
Temperature Capabilities of Industrial Furnaces:
- Industrial furnaces, such as tube furnaces and muffle furnaces, are capable of reaching temperatures up to 1800°C or higher. This high-temperature capability is crucial for processes that require intense heat, such as sintering, annealing, and melting.
- Tube furnaces often feature multiple heating zones, allowing for precise temperature control across different sections of the furnace. This is particularly useful for processes that require uniform heating or specific temperature gradients.
-
Applications Requiring High Temperatures:
- Industries such as ceramics, metals, and minerals rely on furnaces that can sustain high temperatures. For example:
- Ceramics production often involves firing materials at temperatures above 1000°C to achieve desired properties like hardness and durability.
- Metallurgical processes, such as alloy production and heat treatment, require furnaces that can reach and maintain temperatures sufficient to alter the microstructure of metals.
- Mineral processing may involve calcination or sintering, which demand high temperatures to drive off volatile components or fuse particles.
- Industries such as ceramics, metals, and minerals rely on furnaces that can sustain high temperatures. For example:
-
Types of Industrial Furnaces:
- Tube Furnaces: These are designed with one or more heating zones and are often used in research and industrial applications. They can achieve temperatures up to 1800°C and are ideal for processes requiring controlled atmospheres or precise temperature profiles.
- Muffle Furnaces: Known for their ability to isolate samples from direct contact with heating elements, muffle furnaces are widely used in laboratories and small-scale industrial settings. They can also reach temperatures of 1800°C or higher, making them suitable for high-temperature material processing.
- Arc Furnaces: These are typically used in large-scale industrial applications, such as steelmaking. While their temperature capabilities are not explicitly mentioned in the references, they are known to operate at extremely high temperatures, often exceeding 1500°C, to melt and refine metals.
-
Importance of Temperature Control:
- Precise temperature control is vital in industrial furnaces to ensure consistent results and avoid material degradation. For example:
- Overheating can lead to undesirable chemical reactions or material damage.
- Underheating may result in incomplete processing, such as insufficient sintering or melting.
- Modern furnaces are equipped with advanced control systems, including thermocouples and programmable logic controllers (PLCs), to maintain accurate and stable temperatures.
- Precise temperature control is vital in industrial furnaces to ensure consistent results and avoid material degradation. For example:
-
Material Considerations:
- The construction materials of industrial furnaces must withstand extreme temperatures without degrading. Common materials include:
- Refractory ceramics, which provide excellent thermal insulation and resistance to high temperatures.
- High-temperature alloys, such as those containing nickel or chromium, which offer durability and resistance to oxidation.
- These materials ensure the longevity and reliability of furnaces operating at high temperatures.
- The construction materials of industrial furnaces must withstand extreme temperatures without degrading. Common materials include:
-
Industrial vs. Laboratory Furnaces:
- While both industrial and laboratory furnaces can reach similar high temperatures, their designs and applications differ:
- Industrial furnaces are typically larger and built for continuous operation, handling bulk materials.
- Laboratory furnaces are smaller and designed for precise, controlled experiments, often with additional features like atmosphere control.
- While both industrial and laboratory furnaces can reach similar high temperatures, their designs and applications differ:
In summary, industrial furnaces are engineered to achieve and maintain extremely high temperatures, often up to 1800°C or more. Their ability to sustain such temperatures is essential for a wide range of industrial processes, from material processing to metallurgy. The choice of furnace type, temperature control mechanisms, and construction materials all play a critical role in ensuring efficient and reliable operation.
Summary Table:
Aspect | Details |
---|---|
Max Temperature | Up to 1800°C or higher |
Key Applications | Ceramics, metallurgy, mineral processing |
Furnace Types | Tube, muffle, and arc furnaces |
Temperature Control | Advanced systems like thermocouples and PLCs ensure precision |
Construction Materials | Refractory ceramics, high-temperature alloys (nickel, chromium) |
Industrial vs. Lab Furnaces | Industrial: bulk materials; Lab: precise, controlled experiments |
Need a high-temperature furnace for your application? Contact us today to find the right solution!