The temperature of an industrial kiln can vary significantly depending on its type and purpose. Generally, industrial kilns operate within a wide range of temperatures, from as low as 100°C for drying processes to as high as 1800°C or more for high-temperature applications like ceramic firing or metal heat treatment. The specific temperature is determined by the material being processed and the desired outcome. For example, pottery kilns typically operate between 600°C and 1300°C, while cement kilns can reach up to 1450°C. Understanding the temperature requirements is crucial for selecting the right kiln for a specific industrial application.
Key Points Explained:
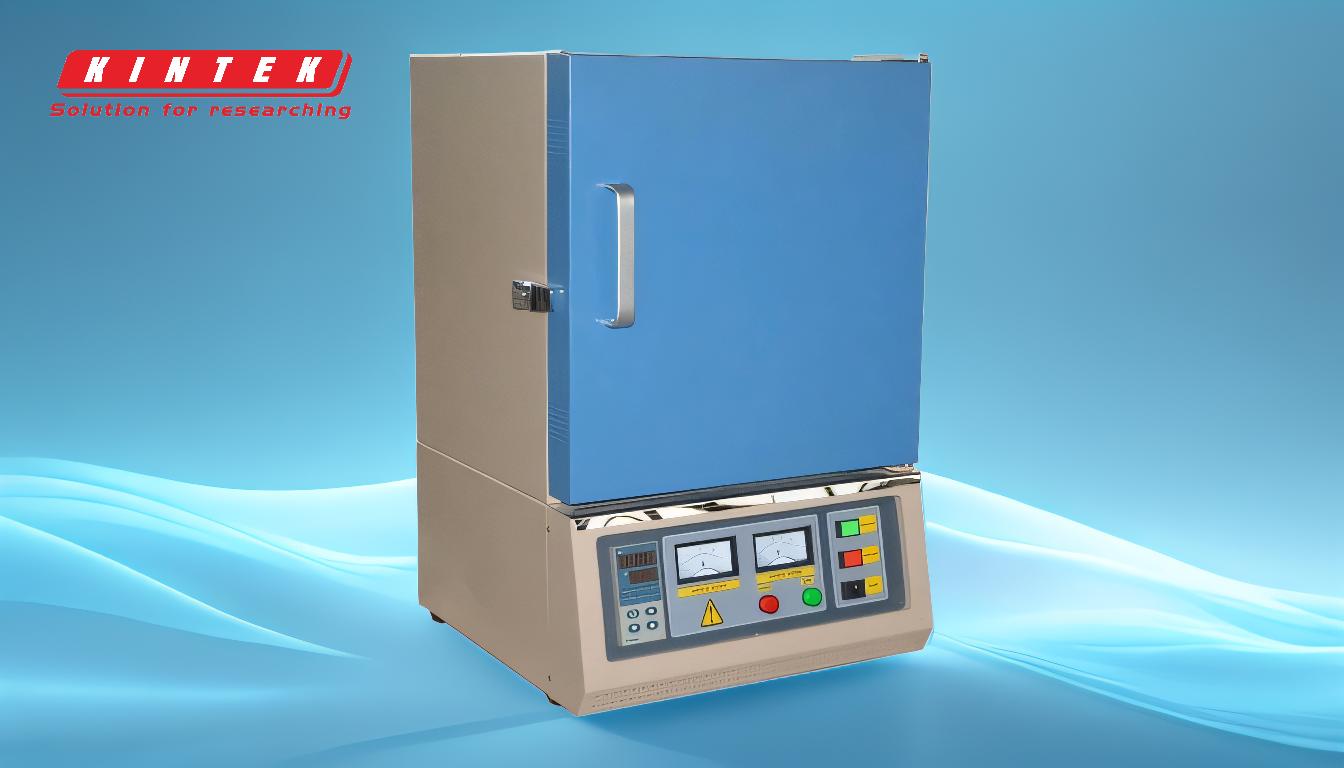
-
Temperature Range of Industrial Kilns:
- Industrial kilns are designed to operate across a broad temperature spectrum, typically ranging from 100°C to 1800°C or higher.
- Lower temperatures (100°C–500°C) are used for drying, curing, or preheating materials.
- Medium temperatures (500°C–1200°C) are common for processes like pottery firing or glass annealing.
- High temperatures (1200°C–1800°C+) are required for advanced applications such as ceramic sintering, metal heat treatment, or refractory material production.
-
Factors Influencing Kiln Temperature:
- Material Properties: The type of material being processed dictates the required temperature. For example, ceramics and metals often require higher temperatures compared to plastics or wood.
- Process Requirements: Different industrial processes, such as drying, firing, or annealing, have specific temperature needs.
- Kiln Design: The construction and insulation of the kiln determine its maximum operating temperature and efficiency.
-
Types of Industrial Kilns and Their Temperature Ranges:
- Pottery Kilns: Typically operate between 600°C and 1300°C, depending on the type of clay and glaze used.
- Cement Kilns: Reach temperatures of up to 1450°C to facilitate the chemical reactions needed for clinker formation.
- Glass Kilns: Operate between 700°C and 1200°C for annealing or melting glass.
- Metal Heat Treatment Kilns: Can exceed 1200°C for processes like hardening or tempering.
- Refractory Kilns: Designed for extreme temperatures, often exceeding 1600°C, to produce materials like bricks or crucibles.
-
Importance of Temperature Control:
- Precise temperature control is critical for achieving consistent results and preventing material defects.
- Advanced kilns use programmable controllers and sensors to maintain accurate temperatures throughout the process.
- Overheating or underheating can lead to product failure, energy waste, or safety hazards.
-
Energy Efficiency and Temperature Management:
- High-temperature kilns consume significant energy, making efficiency a key consideration.
- Insulation materials, such as refractory bricks or ceramic fiber, help retain heat and reduce energy consumption.
- Modern kilns often incorporate heat recovery systems to reuse waste heat and improve sustainability.
-
Applications of High-Temperature Kilns:
- Ceramics and Pottery: Kilns are used to fire clay and glazes at specific temperatures to achieve desired hardness and finish.
- Cement Production: High temperatures are essential for the calcination and sintering of raw materials.
- Metal Processing: Kilns are used for heat treatment, annealing, and sintering of metal parts.
- Refractory Manufacturing: Kilns produce materials capable of withstanding extreme heat for industrial applications.
In conclusion, the temperature of an industrial kiln is highly variable and depends on the specific application and material being processed. Understanding these temperature requirements is essential for selecting the right kiln and ensuring optimal performance in industrial operations.
Summary Table:
Kiln Type | Temperature Range | Common Applications |
---|---|---|
Pottery Kilns | 600°C – 1300°C | Firing clay and glazes |
Cement Kilns | Up to 1450°C | Clinker formation in cement production |
Glass Kilns | 700°C – 1200°C | Annealing or melting glass |
Metal Heat Treatment Kilns | Exceeds 1200°C | Hardening, tempering, and sintering metals |
Refractory Kilns | Exceeds 1600°C | Producing bricks, crucibles, and refractories |
Need help selecting the right industrial kiln for your needs? Contact our experts today for personalized guidance!