A hydraulic press is a powerful machine that uses hydraulic pressure to generate compressive force. It is widely used in manufacturing, metalworking, and other industries for tasks such as forging, molding, and stamping. The construction of a hydraulic press involves several critical components, including a hydraulic cylinder, a pump, a frame, and control systems. The process begins with designing the press based on its intended application, followed by the fabrication of high-strength materials to ensure durability and precision. Assembly involves integrating the hydraulic system with the mechanical structure, and rigorous testing ensures the press operates safely and efficiently. Below, we explore the key steps and components involved in making a hydraulic press.
Key Points Explained:
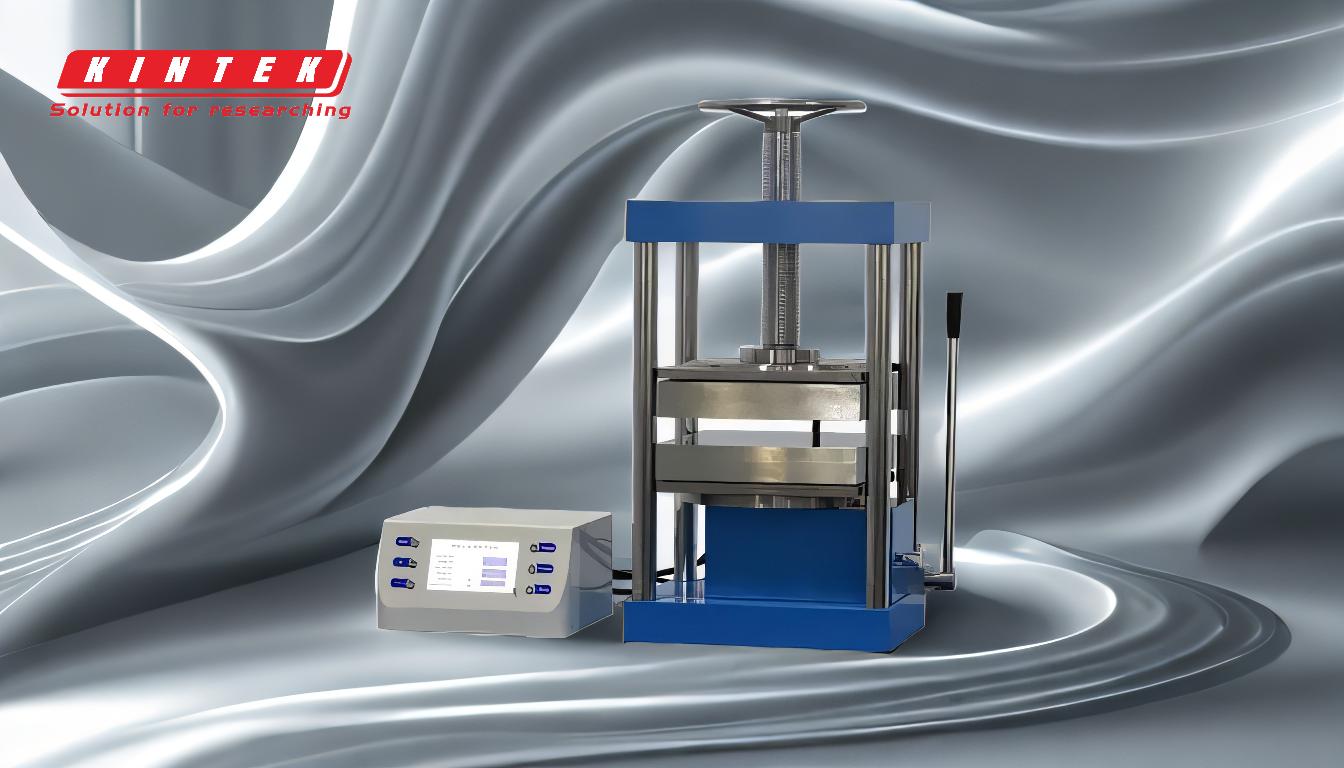
-
Design and Planning:
- The first step in making a hydraulic press is designing it to meet specific requirements, such as force capacity, stroke length, and workspace dimensions.
- Engineers use CAD software to create detailed blueprints, ensuring all components fit together seamlessly.
- The design must account for factors like load distribution, material strength, and safety features.
-
Frame Construction:
- The frame is the backbone of the hydraulic press, providing structural support and stability.
- It is typically made from high-strength steel or cast iron to withstand immense pressure.
- The frame is fabricated using cutting, welding, and machining processes to achieve precise dimensions and alignment.
-
Hydraulic Cylinder Assembly:
- The hydraulic cylinder is the core component that generates the pressing force.
- It consists of a piston, cylinder barrel, seals, and hydraulic fluid.
- Precision machining ensures smooth movement of the piston, while high-quality seals prevent leaks.
-
Hydraulic System Integration:
- The hydraulic system includes a pump, valves, hoses, and a reservoir.
- The pump pressurizes the hydraulic fluid, which is then directed to the cylinder via control valves.
- Proper integration of these components ensures efficient force transmission and smooth operation.
-
Control Systems:
- Modern hydraulic presses are equipped with advanced control systems, including PLCs (Programmable Logic Controllers) and touchscreen interfaces.
- These systems allow operators to adjust parameters like pressure, speed, and cycle time.
- Safety features, such as emergency stop buttons and pressure relief valves, are integrated into the control system.
-
Testing and Calibration:
- Once assembled, the hydraulic press undergoes rigorous testing to ensure it meets performance and safety standards.
- Load testing verifies the press can handle its rated capacity without deformation or failure.
- Calibration ensures accurate force application and consistent operation.
-
Applications and Customization:
- Hydraulic presses are versatile machines used in various industries, including automotive, aerospace, and construction.
- Customization options, such as heated platens for a hydraulic hot press machine, expand their functionality for specific tasks like laminating or curing.
In summary, the construction of a hydraulic press involves a combination of engineering design, precision fabrication, and advanced control systems. Each component plays a critical role in ensuring the machine's performance, durability, and safety. Whether for industrial or specialized applications, hydraulic presses are indispensable tools in modern manufacturing.
Summary Table:
Step | Key Details |
---|---|
Design and Planning | - Use CAD software for blueprints. |
- Account for force capacity, stroke length, and safety features. | |
Frame Construction | - Made from high-strength steel or cast iron. |
- Fabricated using cutting, welding, and machining. | |
Hydraulic Cylinder | - Core component with piston, cylinder barrel, and seals. |
- Precision machining ensures smooth operation. | |
Hydraulic System | - Includes pump, valves, hoses, and reservoir. |
- Ensures efficient force transmission. | |
Control Systems | - Equipped with PLCs and touchscreen interfaces. |
- Adjustable parameters like pressure and speed. | |
Testing and Calibration | - Rigorous load testing and calibration for safety and accuracy. |
Applications | - Used in automotive, aerospace, and construction industries. |
- Customizable for specialized tasks like laminating or curing. |
Ready to explore hydraulic press solutions for your industry? Contact our experts today to get started!