A kiln and an oven are both heating devices, but they serve different purposes and operate under different conditions. A kiln is primarily used for firing ceramics, pottery, and other materials at very high temperatures, often exceeding 1000°C, to achieve chemical and physical transformations. It is designed to handle extreme heat and often has specialized insulation and ventilation systems. On the other hand, an oven is typically used for cooking or baking food at much lower temperatures, usually below 300°C. Ovens are designed for even heat distribution and ease of use in domestic or commercial kitchens. The key differences lie in their temperature range, construction materials, and intended applications.
Key Points Explained:
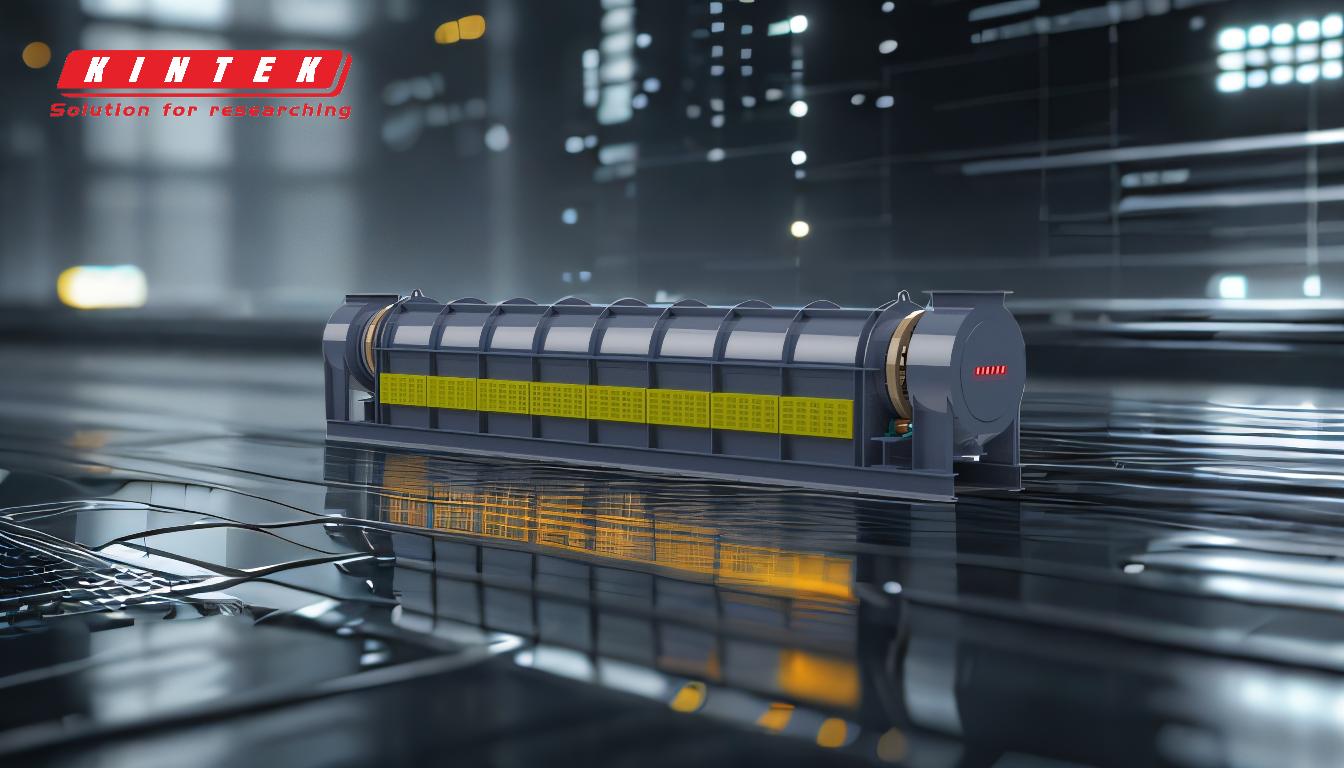
-
Purpose and Applications:
- Kiln: Kilns are primarily used for industrial and artistic purposes, such as firing ceramics, pottery, glass, and metals. They are essential in processes that require high temperatures to achieve chemical changes, like sintering or vitrification.
- Oven: Ovens are designed for cooking and baking food. They are commonly found in domestic kitchens and commercial food establishments. Their primary function is to heat food evenly for consumption.
-
Temperature Range:
- Kiln: Kilns operate at very high temperatures, often ranging from 600°C to over 1700°C, depending on the material being processed. This high heat is necessary for transforming raw materials into finished products.
- Oven: Ovens typically operate at much lower temperatures, usually between 100°C and 300°C. These temperatures are sufficient for cooking food without causing it to burn or undergo chemical changes.
-
Construction and Materials:
- Kiln: Kilns are built to withstand extreme temperatures and are often constructed with refractory materials like firebricks and ceramic fibers. They may also include specialized insulation and ventilation systems to manage heat and fumes.
- Oven: Ovens are generally made from materials like stainless steel, aluminum, and glass, which are suitable for lower temperatures. They are designed for ease of cleaning and maintenance in a kitchen environment.
-
Heat Distribution and Control:
- Kiln: Kilns often have complex heat distribution systems to ensure even firing of materials. They may include multiple heating elements and precise temperature control mechanisms to achieve the desired results.
- Oven: Ovens are designed to distribute heat evenly for cooking food. They typically have simpler heating elements and thermostats to maintain consistent temperatures.
-
Ventilation and Safety:
- Kiln: Kilns require specialized ventilation systems to handle the fumes and gases produced during high-temperature firing. Safety features are crucial to prevent accidents and ensure proper operation.
- Oven: Ovens have basic ventilation systems, usually consisting of vents or fans, to manage steam and odors. Safety features focus on preventing burns and ensuring user-friendly operation.
-
Energy Consumption:
- Kiln: Due to the high temperatures required, kilns consume a significant amount of energy. They are often powered by electricity, gas, or other fuels capable of sustaining prolonged high heat.
- Oven: Ovens consume less energy compared to kilns, as they operate at lower temperatures. They are typically powered by electricity or gas, suitable for domestic and commercial use.
-
Maintenance and Durability:
- Kiln: Kilns require regular maintenance to ensure their refractory materials and heating elements remain in good condition. They are built for durability but need careful handling and upkeep.
- Oven: Ovens are designed for frequent use and easy maintenance. They are generally more user-friendly and require less specialized care compared to kilns.
Understanding these key differences helps in selecting the appropriate equipment for specific tasks, whether it's firing ceramics in a kiln or baking a cake in an oven.
Summary Table:
Aspect | Kiln | Oven |
---|---|---|
Purpose | Firing ceramics, pottery, glass, and metals | Cooking and baking food |
Temperature Range | 600°C to over 1700°C | 100°C to 300°C |
Construction | Refractory materials (firebricks, ceramic fibers) | Stainless steel, aluminum, glass |
Heat Distribution | Complex systems for even firing | Even heat distribution for cooking |
Ventilation | Specialized systems for high-temperature fumes | Basic vents or fans for steam and odors |
Energy Consumption | High energy use due to extreme temperatures | Lower energy use for cooking |
Maintenance | Regular upkeep of refractory materials and heating elements | Easy maintenance and user-friendly design |
Still unsure which heating device is right for your needs? Contact our experts today for personalized advice!