The preparation of cement using the rotary kiln method involves a series of well-defined steps that transform raw materials into clinker, which is then ground to produce cement. The rotary kiln is a critical piece of equipment in this process, designed to heat raw materials to extremely high temperatures, facilitating chemical reactions that result in the formation of clinker. The process begins with the preparation of raw materials, which are then fed into the rotary kiln. As the kiln rotates, the materials move downward due to gravity and are exposed to high temperatures, undergoing calcination and other chemical reactions. The resulting clinker is cooled and ground to produce cement. This method is highly efficient and has been refined over time to optimize energy use and production capacity.
Key Points Explained:
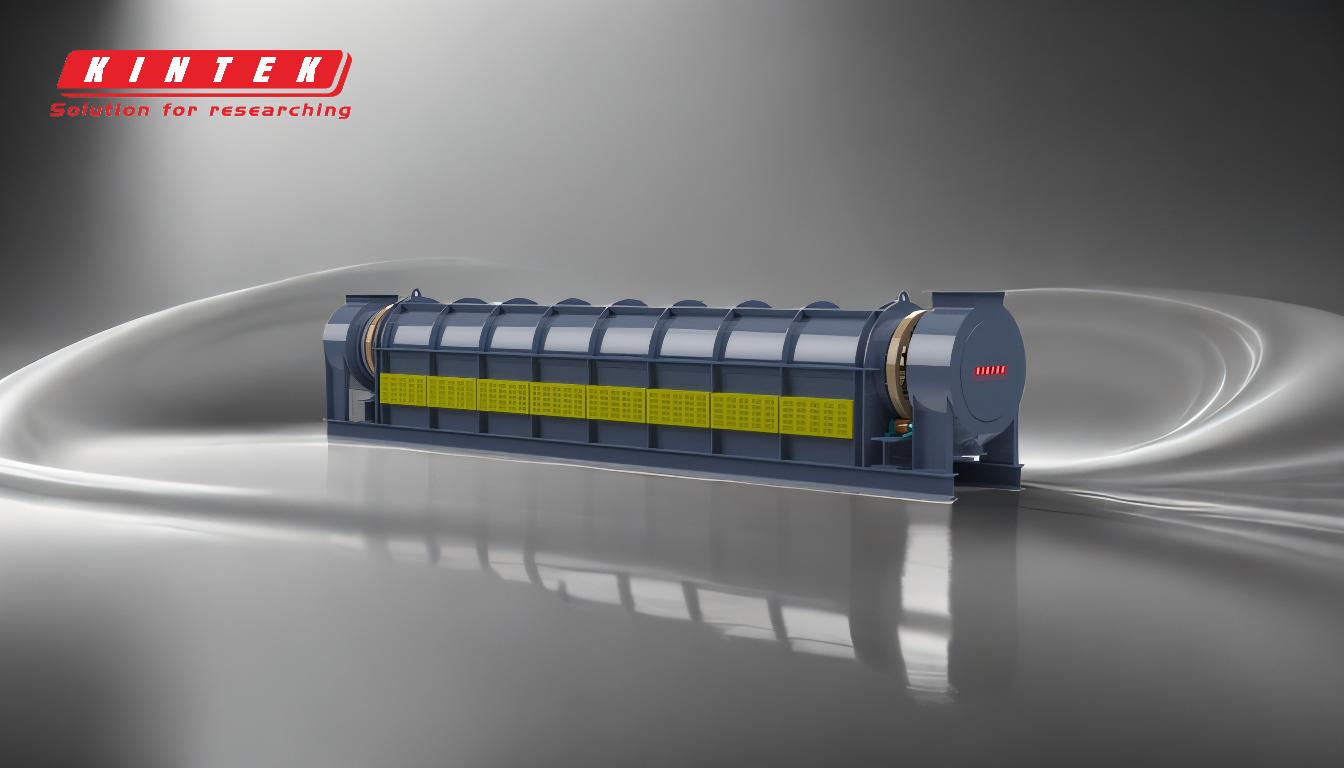
-
Role of the Rotary Kiln in Cement Production:
- The rotary kiln is the core equipment in cement production, responsible for heating raw materials to high temperatures to facilitate chemical reactions.
- It is a large, slightly inclined, rotating cylinder that allows materials to move downward while being exposed to heat.
- The kiln's design ensures uniform heating and mixing of materials, which is crucial for the formation of clinker.
-
Preparation of Raw Materials:
- Raw materials, primarily limestone and clay, are crushed and blended to form a homogeneous mixture.
- This mixture, known as raw meal, is fed into the upper end of the rotary kiln.
- The composition of the raw meal is carefully controlled to ensure the desired chemical reactions occur during the heating process.
-
Heating and Chemical Reactions in the Kiln:
- As the raw meal moves through the kiln, it is heated to temperatures ranging from 1400°C to 1500°C.
- The heating process causes the raw materials to undergo calcination, where limestone (CaCO₃) decomposes into lime (CaO) and carbon dioxide (CO₂).
- Further heating leads to the formation of clinker minerals, primarily alite (C₃S), belite (C₂S), aluminate (C₃A), and ferrite (C₄AF), through a series of complex chemical reactions.
-
Kiln Operation and Temperature Control:
- The rotary kiln operates by rotating slowly, allowing the materials to tumble and mix, ensuring even exposure to heat.
- Hot gases, generated either internally by a flame or externally in a furnace, flow through the kiln, either co-currently or counter-currently to the material flow.
- Temperature profiles within the kiln are carefully controlled based on chemical and thermal analyses to ensure optimal reaction conditions.
-
Clinker Formation and Cooling:
- As the materials reach the lower end of the kiln, they form clinker, a nodular material that is the intermediate product in cement production.
- The clinker is then rapidly cooled in a clinker cooler to preserve its mineral structure and improve grindability.
- Cooling also allows for the recovery of heat, which can be reused in the kiln, improving energy efficiency.
-
Grinding and Final Cement Production:
- The cooled clinker is ground into a fine powder, typically in a ball mill, along with a small amount of gypsum (CaSO₄·2H₂O) to control the setting time of the cement.
- The final product is Portland cement, which is then stored in silos before being packaged and shipped.
-
Energy Efficiency and Technological Advancements:
- Modern rotary kilns are designed to be energy-efficient, often using coal as the primary energy source.
- Advances in kiln technology, such as preheaters and precalciners, have significantly reduced energy consumption and increased production capacity.
- These developments have made the rotary kiln method the most widely used and efficient process for cement production worldwide.
In summary, the rotary kiln method for cement preparation is a complex but highly efficient process that involves precise control of raw materials, temperature, and chemical reactions. The resulting clinker is ground to produce cement, which is essential for construction and infrastructure development. The continuous advancements in rotary kiln technology have further optimized this process, making it more energy-efficient and environmentally friendly.
Summary Table:
Key Steps | Description |
---|---|
Raw Material Preparation | Limestone and clay are crushed, blended, and fed into the rotary kiln. |
Heating & Chemical Reactions | Materials are heated to 1400°C–1500°C, undergoing calcination and clinker formation. |
Clinker Cooling | Clinker is rapidly cooled to preserve mineral structure and improve grindability. |
Grinding & Final Production | Clinker is ground with gypsum to produce Portland cement, ready for packaging. |
Energy Efficiency | Modern kilns use advanced tech like preheaters to reduce energy consumption. |
Discover how the rotary kiln method can optimize your cement production—contact our experts today!