Film thickness control in evaporation systems is a critical aspect of thin-film deposition processes, ensuring that the deposited layers meet specific thickness requirements for various applications. This control is achieved through a combination of precise monitoring techniques, feedback mechanisms, and advanced system designs. The process involves measuring the deposition rate and integrating it over time to determine the film thickness. Key methods include quartz crystal microbalance (QCM) monitoring, optical monitoring, and feedback loops that adjust the evaporation rate in real-time. These techniques ensure uniformity, repeatability, and accuracy in film thickness, which is essential for applications in optics, electronics, and coatings.
Key Points Explained:
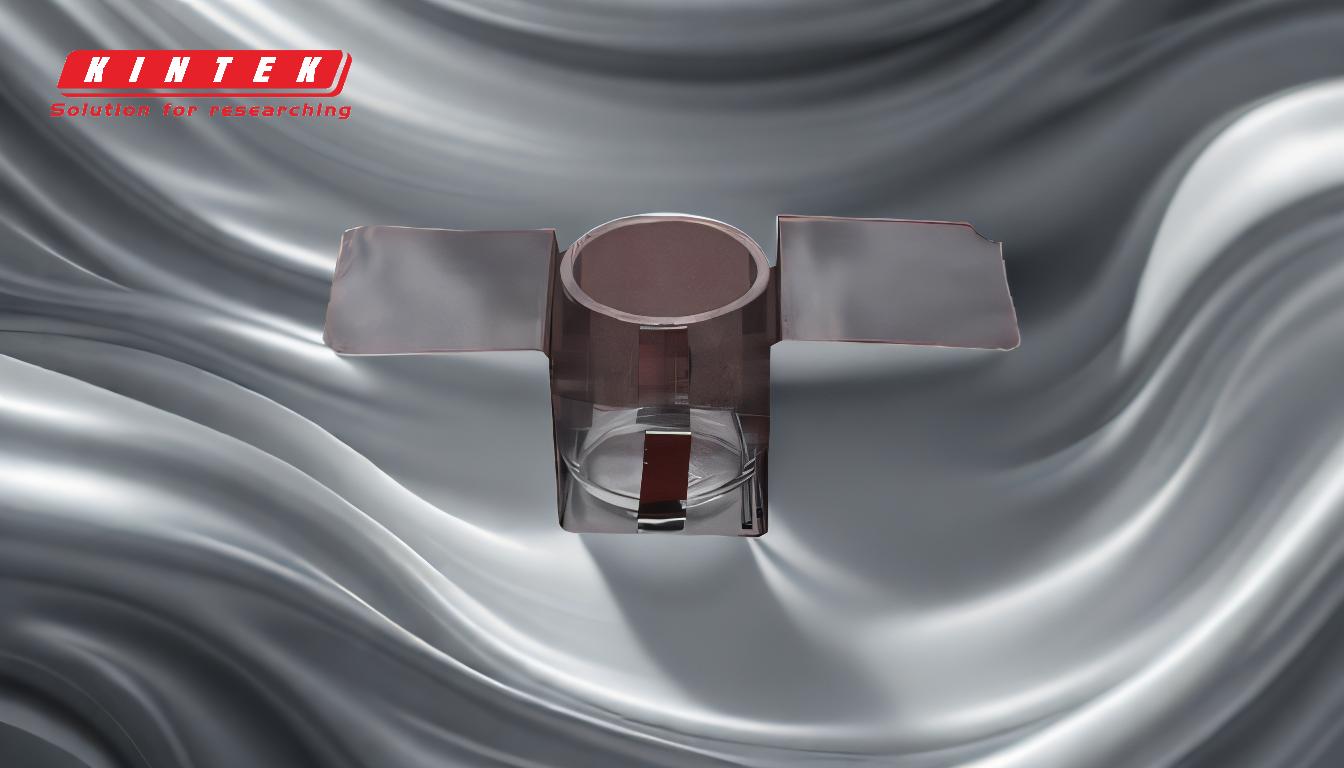
-
Quartz Crystal Microbalance (QCM) Monitoring:
- QCM is a widely used method for real-time film thickness monitoring. It works by measuring the change in resonant frequency of a quartz crystal as material is deposited on its surface.
- The frequency shift is directly proportional to the mass of the deposited film, allowing for precise calculation of film thickness.
- QCM systems are highly sensitive and can detect thickness changes at the nanoscale, making them ideal for applications requiring precise control.
-
Optical Monitoring:
- Optical techniques, such as interferometry, are used to measure film thickness by analyzing the interference patterns created by light reflecting off the substrate and the deposited film.
- These methods are non-contact and can provide real-time feedback on film thickness and uniformity.
- Optical monitoring is particularly useful for transparent or semi-transparent films, where thickness can be inferred from the optical properties.
-
Deposition Rate Control:
- The deposition rate is a critical parameter in controlling film thickness. It is typically controlled by adjusting the power supplied to the evaporation source or the temperature of the material being evaporated.
- Feedback loops are often employed to maintain a constant deposition rate. These loops use data from QCM or optical monitors to adjust the evaporation parameters in real-time.
- Consistent deposition rates ensure uniform film thickness across the substrate.
-
Time-Based Thickness Control:
- Film thickness can also be controlled by integrating the deposition rate over time. By knowing the deposition rate and the desired thickness, the system can calculate the required deposition time.
- This method is straightforward but relies heavily on maintaining a stable deposition rate, which can be challenging without real-time monitoring.
-
Substrate Rotation and Uniformity:
- To achieve uniform film thickness across the substrate, many evaporation systems incorporate substrate rotation. This ensures that all areas of the substrate are exposed equally to the evaporation source.
- Uniformity is further enhanced by optimizing the geometry of the evaporation source and the substrate holder.
-
System Calibration and Calibration Standards:
- Regular calibration of the evaporation system is essential for accurate film thickness control. This involves using calibration standards with known thicknesses to verify the accuracy of the monitoring systems.
- Calibration ensures that the system maintains its precision over time, reducing the risk of errors in film thickness.
-
Advanced Feedback Systems:
- Modern evaporation systems often incorporate advanced feedback systems that integrate data from multiple sensors (e.g., QCM, optical monitors) to provide comprehensive control over the deposition process.
- These systems can automatically adjust parameters such as evaporation rate, substrate temperature, and chamber pressure to achieve the desired film thickness.
-
Applications and Importance of Thickness Control:
- Precise control of film thickness is crucial for applications such as optical coatings, semiconductor devices, and protective coatings. In optics, for example, the thickness of anti-reflective coatings must be precisely controlled to achieve the desired optical properties.
- In semiconductor manufacturing, thin films with specific thicknesses are used to create electronic components with precise electrical characteristics.
By combining these techniques, evaporation systems can achieve highly accurate and repeatable control over film thickness, meeting the stringent requirements of modern thin-film applications.
Summary Table:
Method | Description | Key Benefits |
---|---|---|
Quartz Crystal Microbalance (QCM) | Measures frequency shift to calculate film thickness in real-time. | High sensitivity, nanoscale accuracy, ideal for precise applications. |
Optical Monitoring | Analyzes interference patterns to measure thickness non-invasively. | Real-time feedback, suitable for transparent/semi-transparent films. |
Deposition Rate Control | Adjusts evaporation rate via power or temperature control for uniform thickness. | Ensures consistent deposition rates and uniform film thickness. |
Substrate Rotation | Rotates substrate for equal exposure to the evaporation source. | Enhances film uniformity across the substrate. |
Advanced Feedback Systems | Integrates multiple sensors for automated parameter adjustments. | Achieves precise control over evaporation rate, temperature, and pressure. |
Need precise film thickness control for your applications? Contact our experts today to learn more!