Heat transfer in a furnace primarily occurs through two main mechanisms: indirect heat transfer and direct heat transfer. Indirect heat transfer involves the movement of heat through metal walls and tube and shell units, which are commonly used in industrial furnaces to ensure efficient and controlled heat distribution. Direct heat transfer, on the other hand, is typically associated with processes like char and biomass combustion, where heat is transferred directly to the material being processed. Understanding these mechanisms is crucial for optimizing furnace performance and ensuring energy efficiency.
Key Points Explained:
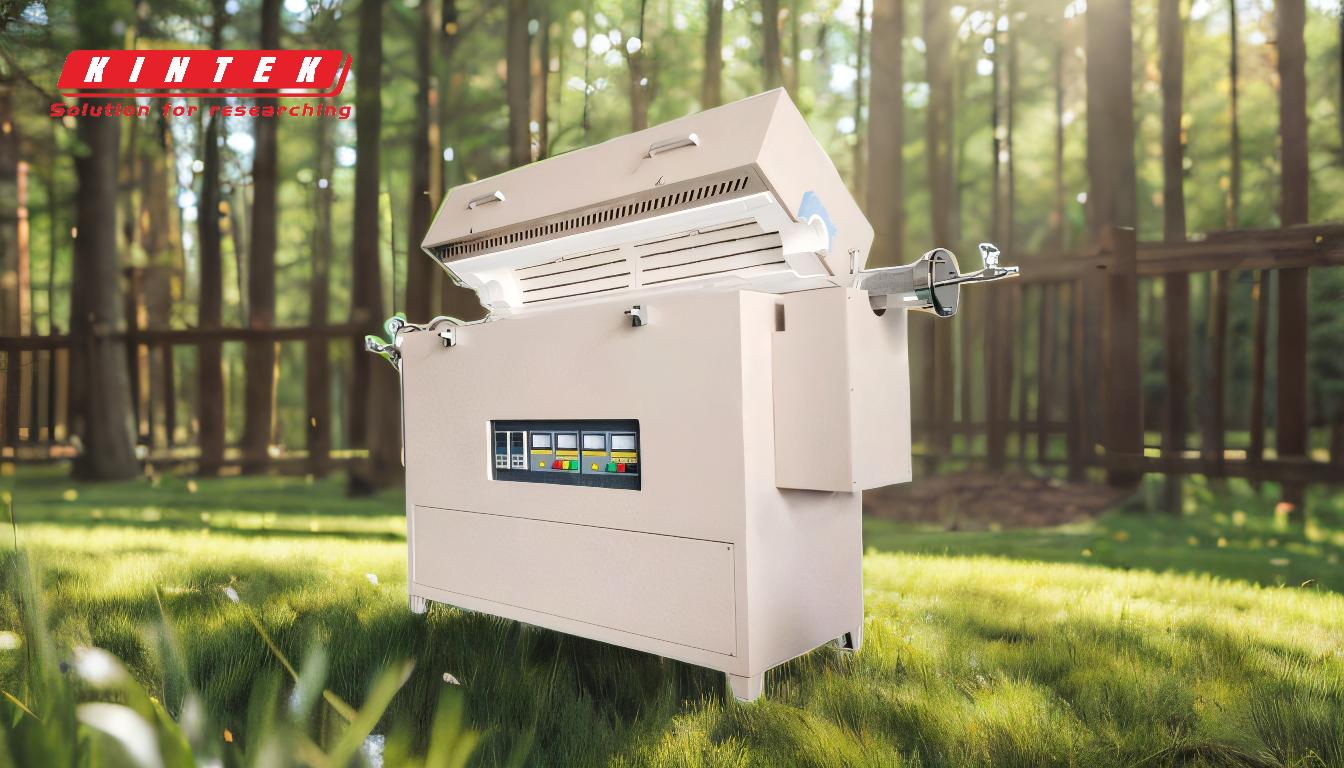
-
Indirect Heat Transfer:
- Mechanism: Heat is transferred through metal walls, tubes, and shell units. This method is common in industrial furnaces where the heat source is separated from the material being heated.
- Applications: Used in processes where precise temperature control is required, such as in chemical reactors, heat exchangers, and certain types of industrial furnaces.
- Advantages: Provides better control over the heating process, reduces the risk of contamination, and enhances safety by isolating the heat source from the material.
-
Direct Heat Transfer:
- Mechanism: Heat is transferred directly to the material, often through combustion processes involving char, biomass, or other fuels. This method is common in applications like biomass boilers and certain types of industrial heating processes.
- Applications: Suitable for processes where high temperatures are needed quickly, such as in the combustion of biomass for energy production or in the pyrolysis of organic materials.
- Advantages: Can achieve higher temperatures more rapidly, is often more energy-efficient for specific applications, and can be simpler in design compared to indirect systems.
-
Comparison and Considerations:
- Efficiency: Indirect heat transfer is generally more efficient for processes requiring precise temperature control, while direct heat transfer can be more efficient for high-temperature applications.
- Safety: Indirect systems are often safer as they isolate the heat source, reducing the risk of fire or contamination. Direct systems require careful management of combustion processes to ensure safety.
- Design Complexity: Indirect systems tend to be more complex due to the need for heat exchangers and insulation, whereas direct systems can be simpler but may require more robust materials to withstand high temperatures.
Understanding these heat transfer mechanisms is essential for selecting the appropriate furnace design and optimizing operational efficiency. Each method has its own set of advantages and challenges, and the choice between them depends on the specific requirements of the application.
Summary Table:
Aspect | Indirect Heat Transfer | Direct Heat Transfer |
---|---|---|
Mechanism | Heat moves through metal walls, tubes, and shell units. | Heat is transferred directly to the material via combustion (e.g., char, biomass). |
Applications | Chemical reactors, heat exchangers, industrial furnaces. | Biomass boilers, pyrolysis, high-temperature industrial processes. |
Advantages | Precise temperature control, reduced contamination, enhanced safety. | Rapid high temperatures, energy-efficient for specific uses, simpler design. |
Efficiency | More efficient for precise temperature control. | More efficient for high-temperature applications. |
Safety | Safer due to isolated heat source. | Requires careful combustion management to ensure safety. |
Design Complexity | More complex due to heat exchangers and insulation. | Simpler design but may need robust materials for high temperatures. |
Need help selecting the right furnace for your application? Contact our experts today to optimize your heat transfer process!