In a vacuum furnace, heat transfer occurs primarily through radiation, as the absence of air or other gases eliminates convection and conduction as viable mechanisms. Radiation involves the transfer of heat in the form of electromagnetic waves, which do not require a medium to propagate. This makes it the dominant mode of heat transfer in vacuum environments. The vacuum furnace's design, including its heating elements and reflective surfaces, optimizes radiative heat transfer to ensure uniform and efficient heating of the materials being processed. The vacuum system, consisting of pumps, valves, and measuring instruments, maintains the low-pressure environment necessary for this process. Understanding the principles of radiative heat transfer and the components of the vacuum system is essential for optimizing the performance of a vacuum furnace.
Key Points Explained:
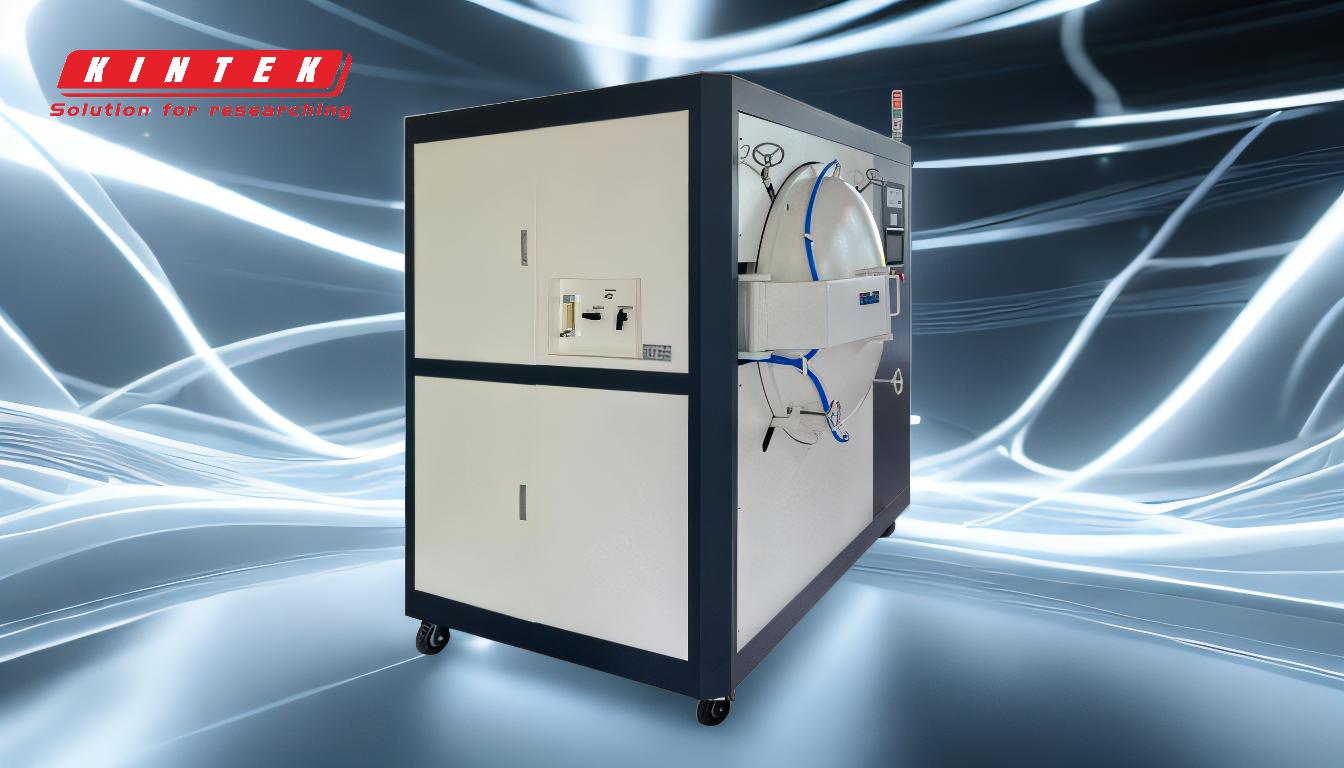
-
Heat Transfer in a Vacuum Furnace:
- In a vacuum furnace, heat transfer occurs almost exclusively through radiation. This is because the vacuum environment lacks air or other gases, which eliminates convection and conduction as significant heat transfer mechanisms.
- Radiation involves the emission of electromagnetic waves from a heat source, such as heating elements, which then travel through the vacuum and are absorbed by the material being heated. This process does not require a medium, making it ideal for vacuum environments.
-
Mechanism of Radiative Heat Transfer:
- Radiative heat transfer is governed by the Stefan-Boltzmann law, which states that the energy radiated per unit area of a black body is proportional to the fourth power of its absolute temperature. This means that even small increases in temperature can significantly enhance heat transfer.
- The heating elements in a vacuum furnace are designed to emit radiation efficiently, often using materials like tungsten or graphite that can withstand high temperatures and emit intense infrared radiation.
-
Role of the Vacuum Environment:
- The vacuum environment is crucial for minimizing heat loss through convection and conduction. By removing air and other gases, the furnace ensures that heat is transferred primarily by radiation, leading to more controlled and uniform heating.
- The vacuum system, which includes components like vacuum pumps, valves, and measuring instruments, maintains the low-pressure environment necessary for effective radiative heat transfer.
-
Components of the Vacuum System:
- Vacuum Pumps: These are used to evacuate air and other gases from the furnace chamber, creating the low-pressure environment required for radiative heat transfer.
- Vacuum Valves: These control the flow of gases into and out of the furnace, helping to maintain the desired vacuum level.
- Vacuum Measuring Instruments: These monitor the pressure inside the furnace, ensuring that it remains within the optimal range for heat treatment processes.
-
Advantages of Radiative Heat Transfer in Vacuum Furnaces:
- Uniform Heating: Radiative heat transfer ensures that heat is distributed evenly across the material, reducing the risk of hot spots or uneven heating.
- Efficiency: Since radiation does not require a medium, it is a highly efficient method of heat transfer in a vacuum, leading to faster heating times and lower energy consumption.
- Precision: The ability to control the temperature and radiation intensity allows for precise heat treatment processes, which is critical for applications like metal hardening or brazing.
-
Applications of Vacuum Furnaces:
- Vacuum furnaces are widely used in industries that require precise and controlled heat treatment processes, such as aerospace, automotive, and electronics manufacturing.
- Common applications include annealing, brazing, sintering, and hardening of metals, where the absence of oxygen and other reactive gases prevents oxidation and contamination of the materials being processed.
-
Comparison with Other Furnace Types:
- Muffle Furnace: Similar to a vacuum furnace, heat transfer in a muffle furnace also occurs primarily through radiation. However, a muffle furnace operates at atmospheric pressure and may use a protective atmosphere to prevent oxidation.
- Salt Bath Furnace: In contrast, heat transfer in a salt bath furnace occurs mainly through convection, as the molten salt comes into direct contact with the material, providing rapid and uniform heating. This method is less suitable for processes that require a vacuum environment.
-
Optimization of Heat Transfer in Vacuum Furnaces:
- Heating Elements: The choice of heating elements is critical for optimizing radiative heat transfer. Materials like tungsten and graphite are commonly used due to their high emissivity and ability to withstand extreme temperatures.
- Reflective Surfaces: The interior surfaces of the furnace chamber are often lined with reflective materials to maximize the efficiency of radiative heat transfer by reflecting radiation back onto the material being heated.
- Temperature Control: Advanced temperature control systems are used to regulate the intensity of radiation, ensuring that the material is heated to the desired temperature without overheating or underheating.
By understanding these key points, users can better appreciate the unique advantages of vacuum furnaces and how they leverage radiative heat transfer to achieve precise and efficient heat treatment processes.
Summary Table:
Key Aspect | Details |
---|---|
Heat Transfer Mechanism | Primarily through radiation, as convection and conduction are eliminated. |
Role of Vacuum Environment | Removes air/gases, enabling efficient radiative heat transfer. |
Key Components | Vacuum pumps, valves, and measuring instruments maintain low pressure. |
Advantages | Uniform heating, energy efficiency, and precise temperature control. |
Applications | Aerospace, automotive, and electronics manufacturing. |
Learn how a vacuum furnace can optimize your heat treatment processes—contact our experts today!