Induction heating is a non-contact heating process that utilizes electromagnetic induction and Joule heating to generate heat within conductive materials, such as metals and semiconductors. The process involves creating a transient magnetic field using an alternating current in a coil, which induces eddy currents in the material. These eddy currents flow against the material's resistivity, generating heat through Joule heating. This method is highly efficient, fast, and widely used in industrial, medical, and domestic applications due to its precision and advantages over traditional heating techniques.
Key Points Explained:
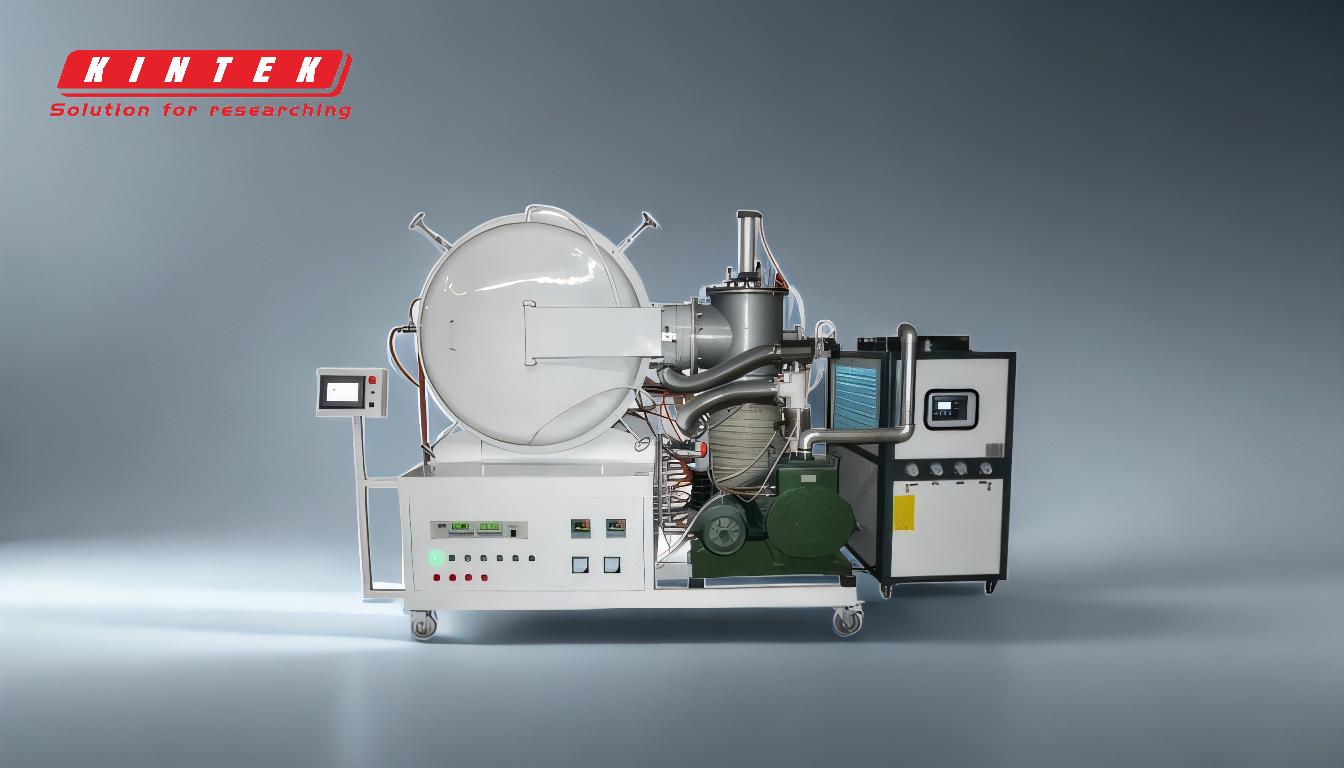
-
Electromagnetic Induction:
- Induction heating relies on electromagnetic induction, where an alternating current (AC) flows through a coil (solenoid), creating a transient magnetic field.
- This magnetic field induces electric currents, known as eddy currents, in nearby conductive materials.
- The strength and frequency of the alternating current determine the intensity and depth of the induced eddy currents.
-
Eddy Currents and Joule Heating:
- Eddy currents are loops of electrical current induced within the conductive material due to the changing magnetic field.
- As these currents flow, they encounter the material's electrical resistance, which converts the electrical energy into heat through the Joule heating effect.
- The amount of heat generated depends on the material's resistivity and the magnitude of the eddy currents.
-
Non-Contact Heating:
- Induction heating is a non-contact process, meaning the heat is generated directly within the material without physical contact between the heating source (coil) and the material.
- This eliminates contamination and allows for precise and localized heating, making it ideal for applications requiring high accuracy.
-
Material Suitability:
- Induction heating is most effective with materials that are electrically conductive, such as metals (e.g., steel, copper, aluminum) and semiconductors.
- Materials with higher magnetic permeability and electrical conductivity heat more efficiently due to stronger eddy current generation.
-
Applications and Advantages:
- Industrial Uses: Melting metals, forging, brazing, and heat treatment.
- Medical Applications: Sterilization of instruments and localized heating in medical devices.
- Domestic Uses: Induction cooktops for fast and energy-efficient cooking.
- Advantages: Faster heating, energy efficiency, precise temperature control, and reduced contamination compared to traditional methods like flame or resistance heating.
-
Process Control and Efficiency:
- The frequency of the alternating current can be adjusted to control the depth of heating, allowing for surface heating or deep penetration as needed.
- Induction heating systems can achieve high thermal efficiency, as energy is directly transferred to the material with minimal losses.
By leveraging the principles of electromagnetic induction and Joule heating, induction heating provides a versatile, efficient, and precise method for heating conductive materials across various industries.
Summary Table:
Key Aspect | Description |
---|---|
Electromagnetic Induction | Alternating current in a coil creates a magnetic field, inducing eddy currents. |
Eddy Currents & Joule Heating | Eddy currents generate heat through material resistance (Joule heating). |
Non-Contact Heating | Heat is generated within the material without physical contact, reducing contamination. |
Material Suitability | Effective for conductive materials like metals and semiconductors. |
Applications | Industrial (melting, forging), medical (sterilization), domestic (cooktops). |
Advantages | Fast, energy-efficient, precise, and contamination-free heating. |
Ready to explore the benefits of induction heating for your applications? Contact us today to learn more!