Sintering temperature is determined by a combination of material properties, desired final product characteristics, and process parameters. Key factors include the type of material being sintered, the required density and mechanical properties of the final product, and the sintering atmosphere. The temperature must be high enough to facilitate particle bonding and densification but not so high as to cause excessive grain growth or material degradation. Additionally, factors such as particle size, composition, and the presence of a liquid phase play a role in determining the optimal sintering temperature. The sintering process is typically carried out in a controlled environment, with the temperature and time carefully adjusted to achieve the desired outcomes.
Key Points Explained:
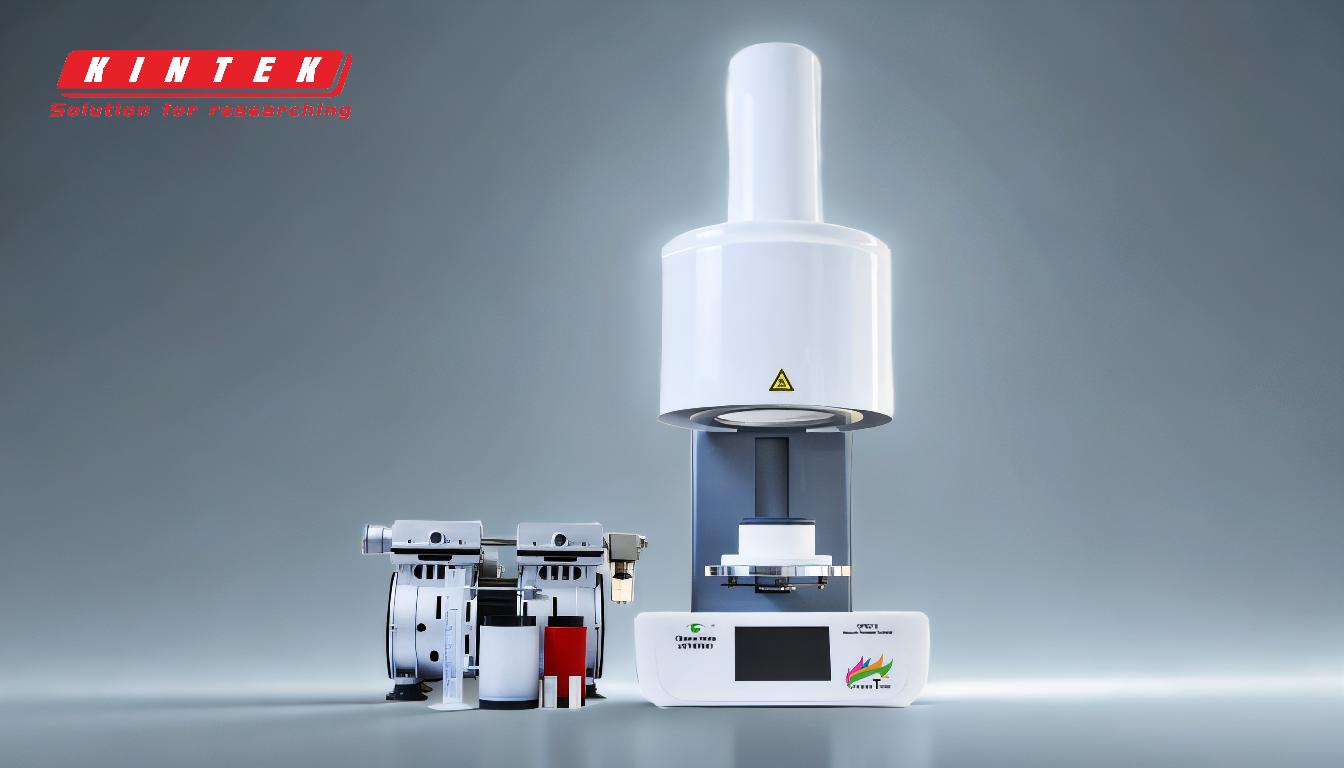
-
Material Properties:
- The type of material being sintered is a primary factor in determining the sintering temperature. Different materials have different melting points and sintering behaviors. For example, metals, ceramics, and polymers each require specific temperature ranges to achieve optimal densification and bonding.
- The composition of the material also plays a role. Homogeneous compositions and finer particle sizes generally allow for lower sintering temperatures due to increased surface area and reactivity.
-
Desired Final Product Characteristics:
- The required density and mechanical properties of the final product significantly influence the sintering temperature. Higher temperatures generally lead to greater densification and improved mechanical properties such as tensile strength, bending fatigue strength, and impact energy.
- However, excessively high temperatures can lead to undesirable grain growth, which may degrade the material's properties. Therefore, the temperature must be carefully balanced to achieve the desired density and mechanical performance without compromising the material's integrity.
-
Sintering Atmosphere:
- The atmosphere in which sintering occurs (e.g., air, vacuum, or inert gases like argon or nitrogen) can affect the sintering temperature. For instance, sintering in a vacuum or inert atmosphere can prevent oxidation and allow for higher temperatures without material degradation.
- The choice of atmosphere depends on the material and the desired properties of the final product. For example, sintering in a reducing atmosphere may be necessary for certain metals to prevent oxidation.
-
Particle Size and Composition:
- Smaller particle sizes generally require lower sintering temperatures because they have a higher surface area, which facilitates faster and more efficient densification.
- The composition of the material, including the presence of any additives or binders, can also influence the sintering temperature. For example, the presence of a liquid phase during sintering can lower the required temperature but must be carefully controlled to avoid defects.
-
Process Parameters:
- The heating rate and applied pressure are critical process parameters that influence the sintering temperature. A faster heating rate can lead to higher densification but may also increase the risk of thermal stresses and defects.
- Applied pressure can enhance particle rearrangement and eliminate porosity, allowing for lower sintering temperatures. However, the pressure must be carefully controlled to avoid damaging the material.
-
Equipment and Sintering Method:
- The type of sintering equipment used (e.g., belt conveyor, push, or batch furnace) can affect the temperature and time required for sintering. Different furnaces have varying heating capabilities and temperature control mechanisms, which must be considered when determining the sintering temperature.
- The sintering method (e.g., conventional, spark plasma sintering, or hot isostatic pressing) also influences the temperature. Advanced methods like spark plasma sintering can achieve high densification at lower temperatures due to the application of electrical currents and pressure.
-
Cooling Rate:
- The cooling rate after sintering can impact the final material properties. Rapid cooling may lead to residual stresses and reduced mechanical properties, while slower cooling can allow for more controlled grain growth and improved properties.
- The cooling rate must be optimized based on the material and desired properties, often requiring a controlled cooling environment.
In summary, determining the sintering temperature involves a comprehensive evaluation of material properties, desired product characteristics, sintering atmosphere, particle size and composition, process parameters, equipment, and cooling rate. Each of these factors must be carefully considered and balanced to achieve the optimal sintering temperature for a given application.
Summary Table:
Factor | Impact on Sintering Temperature |
---|---|
Material Properties | Different materials (metals, ceramics, polymers) require specific temperature ranges for bonding. |
Final Product Density | Higher temperatures improve densification but must avoid excessive grain growth. |
Sintering Atmosphere | Vacuum or inert gases allow higher temperatures without oxidation. |
Particle Size | Smaller particles enable lower sintering temperatures due to increased surface area. |
Process Parameters | Heating rate and applied pressure influence temperature and densification. |
Equipment & Method | Advanced methods like spark plasma sintering achieve densification at lower temperatures. |
Cooling Rate | Controlled cooling prevents residual stresses and improves material properties. |
Need help determining the optimal sintering temperature for your materials? Contact our experts today!