Temperature control in induction heating is a critical aspect of ensuring precise and efficient heating processes. It involves a combination of advanced technologies and methodologies to monitor and regulate the temperature of the workpiece or material being heated. The process typically includes the use of temperature sensors, feedback loops, and control systems that adjust the power supplied to the induction coil based on real-time temperature readings. This ensures that the desired temperature is maintained consistently, preventing overheating or underheating, which could compromise the quality of the final product. The integration of these components allows for high levels of accuracy and repeatability in industrial applications.
Key Points Explained:
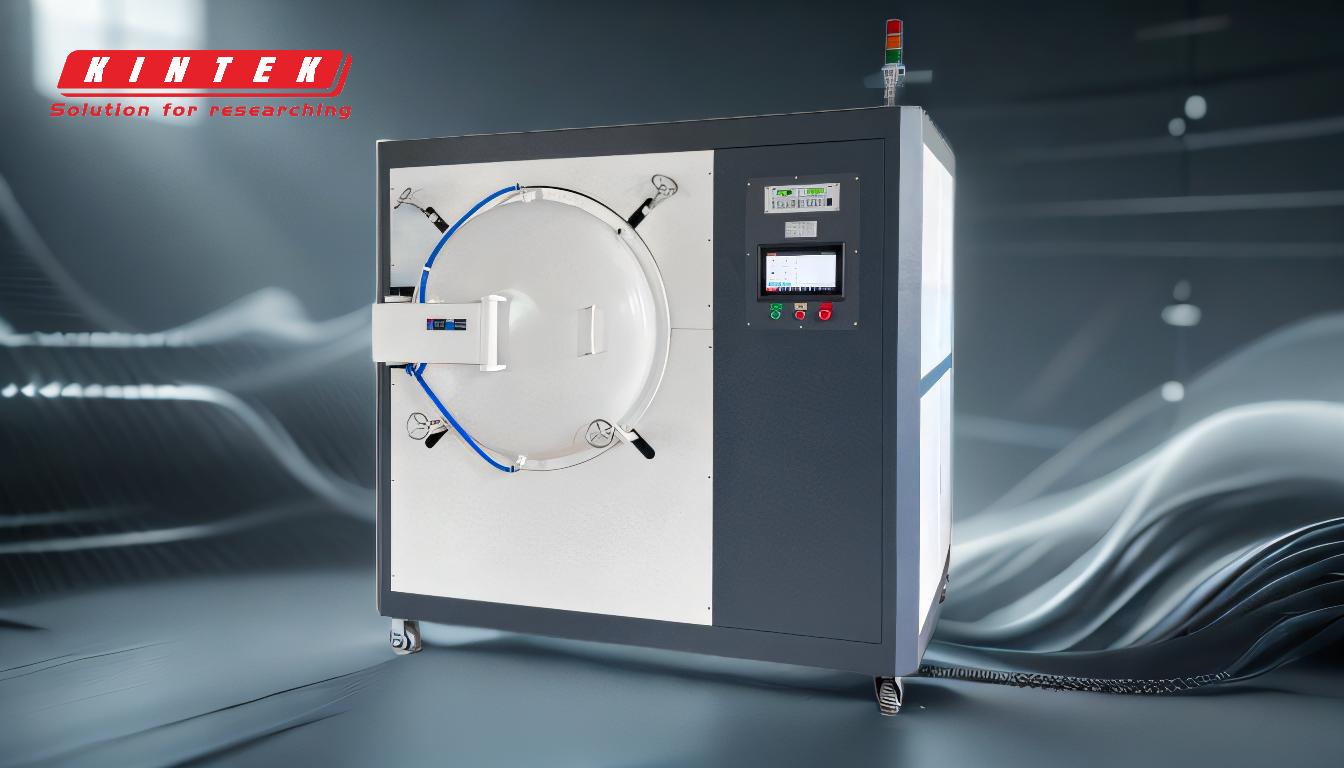
-
Temperature Sensors and Measurement:
- Role: Temperature sensors are fundamental in induction heating systems as they provide real-time data on the temperature of the workpiece.
- Types: Common types of sensors used include thermocouples, infrared pyrometers, and optical pyrometers. Each type has its own advantages depending on the application, such as the need for contact or non-contact measurement.
- Placement: The placement of these sensors is crucial. They must be positioned to accurately reflect the temperature of the area being heated without interfering with the induction process.
-
Feedback Control Systems:
- Function: Feedback control systems use the data from temperature sensors to adjust the power output of the induction heating system.
- Components: These systems typically include a controller, which processes the sensor data, and a power supply that adjusts the current to the induction coil.
- Process: If the sensor detects a temperature below the setpoint, the controller increases the power to the coil, and vice versa. This creates a closed-loop system that continuously adjusts to maintain the desired temperature.
-
Power Regulation:
- Importance: The power supplied to the induction coil directly affects the intensity of the electromagnetic field and, consequently, the heat generated in the workpiece.
- Methods: Power regulation can be achieved through various methods, including phase control, pulse width modulation (PWM), and frequency modulation. These methods allow for precise control over the heating process.
- Efficiency: Efficient power regulation not only ensures accurate temperature control but also minimizes energy consumption, making the process more cost-effective.
-
Advanced Control Algorithms:
- Adaptive Control: Some systems use adaptive control algorithms that can adjust parameters in real-time based on changes in the workpiece or environmental conditions.
- Predictive Control: Predictive models can forecast temperature changes and preemptively adjust the power supply to maintain stability.
- Integration with AI: Advanced systems may integrate artificial intelligence to optimize the heating process based on historical data and predictive analytics.
-
Safety and Redundancy:
- Safety Mechanisms: Temperature control systems often include safety mechanisms such as over-temperature protection and emergency shutdown features to prevent damage to the equipment or workpiece.
- Redundancy: Redundant sensors and control systems can be implemented to ensure reliability. If one sensor or controller fails, the backup can take over, preventing process interruptions.
-
Application-Specific Considerations:
- Material Properties: Different materials have varying thermal properties, such as thermal conductivity and specific heat capacity, which affect how they respond to induction heating. The control system must account for these properties to achieve uniform heating.
- Heating Profile: The desired heating profile, including the rate of temperature increase and the final temperature, must be carefully programmed into the control system. This ensures that the material is heated in a way that meets the specific requirements of the application, such as hardening, annealing, or brazing.
By integrating these key components and considerations, temperature control in induction heating systems can achieve high precision and reliability, essential for a wide range of industrial applications.
Summary Table:
Key Component | Function | Examples/Details |
---|---|---|
Temperature Sensors | Provide real-time temperature data | Thermocouples, infrared pyrometers, optical pyrometers |
Feedback Control Systems | Adjust power output based on sensor data | Includes controllers and power supplies for closed-loop systems |
Power Regulation | Control the intensity of the electromagnetic field | Methods: Phase control, PWM, frequency modulation |
Advanced Control Algorithms | Optimize heating in real-time | Adaptive control, predictive models, AI integration |
Safety and Redundancy | Prevent equipment damage and ensure reliability | Over-temperature protection, emergency shutdown, redundant systems |
Application-Specific Considerations | Tailor heating to material properties and requirements | Thermal conductivity, specific heat capacity, heating profiles for hardening, annealing, brazing |
Discover how precise temperature control can enhance your induction heating processes—contact our experts today!