To achieve the greatest joint strength in brazing, several factors must be carefully considered, including the selection of materials, joint design, surface preparation, and the brazing process itself. Brazing involves joining two or more metal parts using a filler metal with a melting point above 450°C (842°F) but below the melting point of the base metals. The strength of the brazed joint depends on the quality of the bond, the filler metal's properties, and the joint's design. Below is a detailed explanation of how to maximize joint strength in brazing.
Key Points Explained:
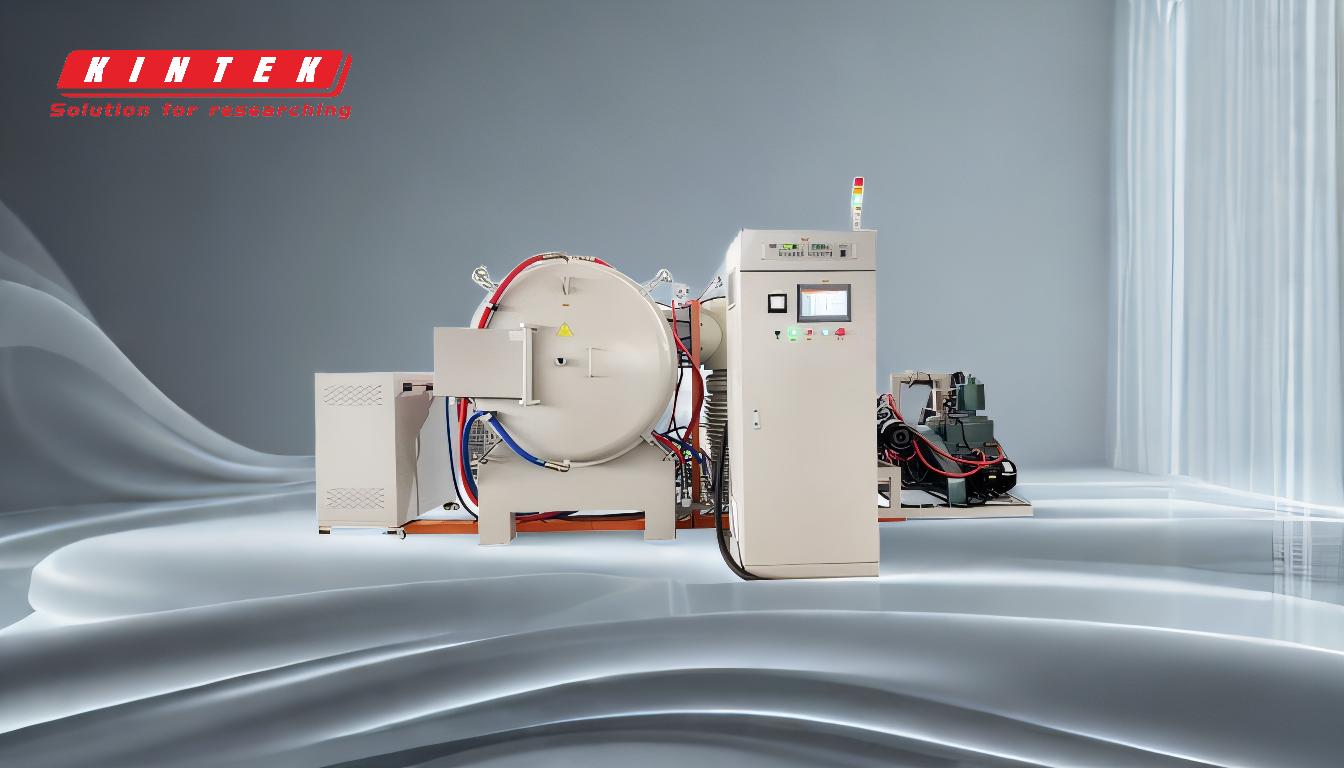
-
Proper Joint Design:
- The design of the joint is critical for achieving maximum strength. A well-designed joint ensures even distribution of stress and optimal flow of the filler metal.
- Common joint designs include lap joints, butt joints, and scarf joints. Lap joints are often preferred for brazing because they provide a larger surface area for bonding, which enhances strength.
- The clearance between the parts being joined (joint gap) should be carefully controlled. A gap of 0.05 to 0.15 mm (0.002 to 0.006 inches) is typically ideal for capillary action to draw the filler metal into the joint.
-
Surface Preparation:
- Cleanliness is essential for a strong brazed joint. Contaminants such as oil, grease, oxides, and dirt can prevent proper wetting and bonding of the filler metal.
- Surfaces should be cleaned using mechanical methods (e.g., abrasion) or chemical methods (e.g., degreasing and pickling) before brazing.
- Proper surface preparation ensures that the filler metal can flow smoothly and form a strong metallurgical bond with the base metals.
-
Selection of Filler Metal:
- The choice of filler metal significantly impacts joint strength. The filler metal should have good wettability, compatibility with the base metals, and appropriate mechanical properties.
- Common filler metals include silver-based alloys, copper-based alloys, and nickel-based alloys. The selection depends on the base metals and the operating conditions of the joint.
- The filler metal should also have a suitable melting range to ensure it flows properly without overheating the base metals.
-
Controlled Heating and Cooling:
- Uniform heating is crucial for achieving a strong brazed joint. Uneven heating can lead to incomplete bonding or thermal stresses.
- The heating method (e.g., torch, furnace, induction) should be selected based on the joint's size, shape, and materials.
- Controlled cooling is equally important to prevent cracking or distortion. Rapid cooling should be avoided unless the materials and process specifically require it.
-
Use of Flux or Protective Atmosphere:
- Flux is often used to remove oxides and promote wetting of the filler metal. It also protects the joint from oxidation during the brazing process.
- In some cases, a protective atmosphere (e.g., inert gas or vacuum) is used instead of flux to prevent oxidation and contamination.
- The choice between flux and a protective atmosphere depends on the materials and the brazing method.
-
Avoiding Re-Melting Existing Joints:
- When repairing defective joints, it is better to apply a small amount of additional filler metal rather than re-melting the existing joint. Re-melting can alter the microstructure of the joint and reduce its strength.
- Most braze alloys develop a higher re-melt temperature after the initial braze, which can make re-melting less effective and potentially harmful to the joint.
-
Post-Braze Inspection and Testing:
- After brazing, the joint should be inspected for defects such as voids, cracks, or incomplete bonding. Non-destructive testing methods (e.g., visual inspection, X-ray, ultrasonic testing) can be used to ensure quality.
- Mechanical testing (e.g., tensile or shear testing) may also be performed to verify the joint's strength.
By carefully considering these factors, the greatest joint strength in brazing can be achieved. Proper joint design, surface preparation, filler metal selection, controlled heating and cooling, and the use of flux or protective atmospheres all contribute to a strong and reliable brazed joint. Additionally, avoiding re-melting existing joints and conducting thorough post-braze inspections ensure the integrity of the joint over time.
Summary Table:
Factor | Key Considerations |
---|---|
Joint Design | Use lap joints for larger bonding area; maintain 0.05–0.15 mm gap for capillary action. |
Surface Preparation | Clean surfaces thoroughly to remove contaminants; use mechanical or chemical methods. |
Filler Metal Selection | Choose alloys (e.g., silver, copper, nickel) with good wettability and compatibility. |
Heating & Cooling | Ensure uniform heating; avoid rapid cooling to prevent cracks or distortion. |
Flux/Protective Atmosphere | Use flux or inert gas to prevent oxidation and promote filler metal flow. |
Avoid Re-Melting | Add new filler metal instead of re-melting to preserve joint strength. |
Post-Braze Inspection | Inspect for defects using visual, X-ray, or ultrasonic testing; perform mechanical tests. |
Need expert advice on achieving strong brazed joints? Contact us today for tailored solutions!