The lifespan of a coating, such as PVD (Physical Vapor Deposition) coating, varies significantly based on several factors. These include the type of substrate material, the thickness of the coating, the bond strength between the coating and the substrate, and the environmental conditions such as exposure to high temperatures and wear. Understanding these factors can help in predicting the durability and performance of the coating in specific applications.
Key Points Explained:
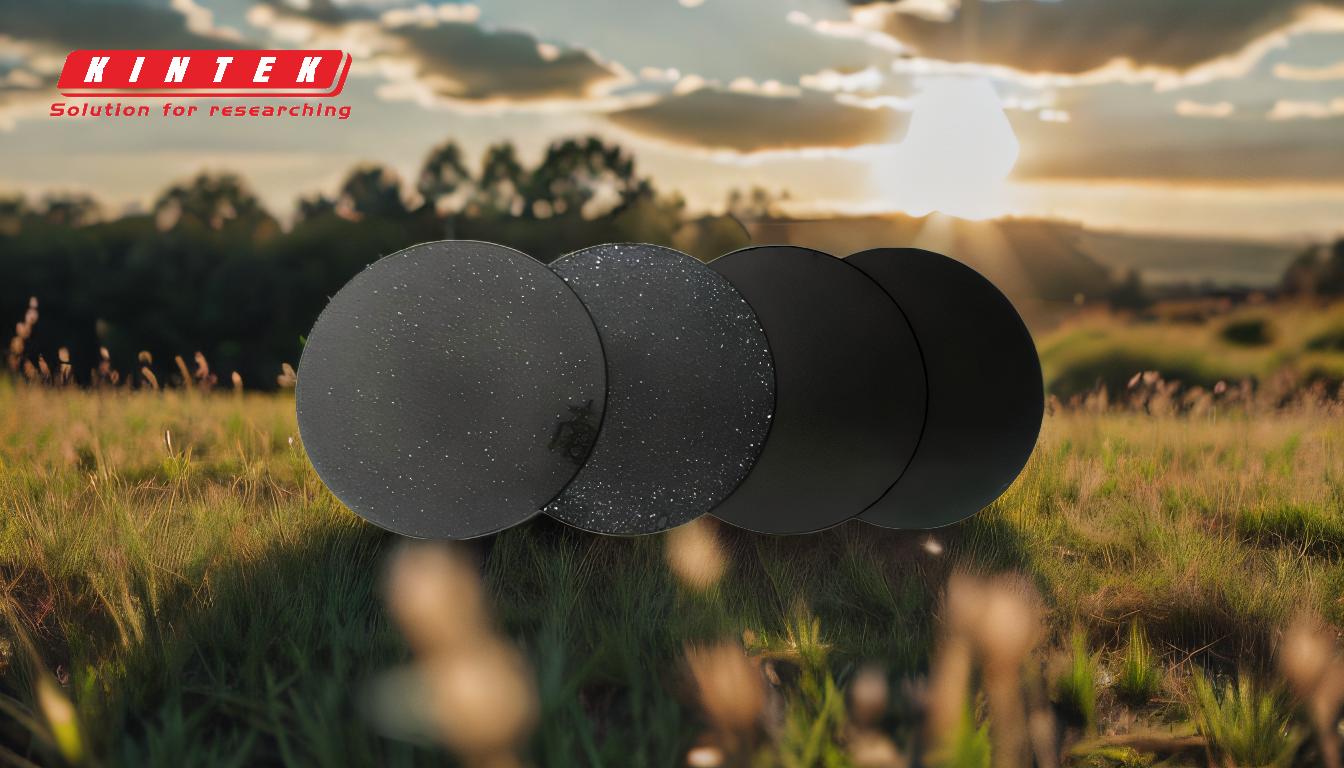
-
Type of Substrate:
- Explanation: The material on which the coating is applied plays a crucial role in determining the lifespan of the coating. Different substrates have varying surface energies and chemical compositions, which can affect how well the coating adheres and performs over time.
- Impact: For instance, coatings on metals like stainless steel might last longer compared to those on softer materials due to better adhesion and resistance to wear.
-
Thickness of the Coating:
- Explanation: The thickness of the coating is directly proportional to its durability. Thicker coatings generally provide better protection against wear and corrosion.
- Impact: However, excessively thick coatings might lead to issues like cracking or delamination, especially under mechanical stress or thermal cycling.
-
Bond Strength Between Coating and Substrate:
- Explanation: The adhesion strength between the coating and the substrate is critical for the longevity of the coating. Stronger bonds ensure that the coating remains intact under mechanical stress and environmental exposure.
- Impact: Techniques like surface preparation (cleaning, etching) and the use of intermediate layers can enhance bond strength, thereby extending the coating's lifespan.
-
Exposure to High Temperatures:
- Explanation: High temperatures can cause thermal expansion and stress at the interface between the coating and the substrate, potentially leading to cracking or delamination.
- Impact: Coatings designed to withstand high temperatures, such as those used in aerospace or automotive applications, are formulated to maintain integrity under thermal stress.
-
Exposure to Wear:
- Explanation: The operational environment, including factors like friction, abrasion, and impact, significantly affects the coating's durability. Coatings in high-wear environments need to have high hardness and wear resistance.
- Impact: For example, coatings on cutting tools or industrial machinery parts are often subjected to intense wear, necessitating the use of highly durable materials like titanium nitride (TiN) or diamond-like carbon (DLC).
Understanding these factors and how they interact is essential for selecting the right coating for a specific application, ensuring optimal performance and longevity. By considering the type of substrate, coating thickness, bond strength, and environmental exposures, one can make informed decisions that enhance the durability and effectiveness of the coating.
Summary Table:
Factor | Explanation | Impact |
---|---|---|
Type of Substrate | Material properties affect adhesion and performance. | Coatings on metals like stainless steel last longer due to better adhesion and wear resistance. |
Thickness of the Coating | Thicker coatings offer better protection but may crack under stress. | Optimal thickness ensures durability without compromising integrity. |
Bond Strength | Strong adhesion prevents delamination under stress. | Surface preparation and intermediate layers enhance bond strength. |
High Temperatures | Thermal stress can cause cracking or delamination. | High-temperature-resistant coatings maintain integrity in demanding applications. |
Exposure to Wear | Friction, abrasion, and impact reduce coating lifespan. | Durable materials like TiN or DLC are used in high-wear environments. |
Optimize your coating performance—contact us today for expert advice!