Annealing is a heat treatment process used to alter the physical and sometimes chemical properties of a material to increase its ductility and reduce its hardness, making it more workable. The process involves heating the metal to a specific temperature, holding it there for a certain period, and then cooling it down at a controlled rate. The duration of the annealing process can vary significantly depending on the type of metal, its thickness, and the desired outcome. The process is divided into three main stages: Recovery, Recrystallization, and Grain Growth. Each stage plays a crucial role in the overall effectiveness of the annealing process.
Key Points Explained:
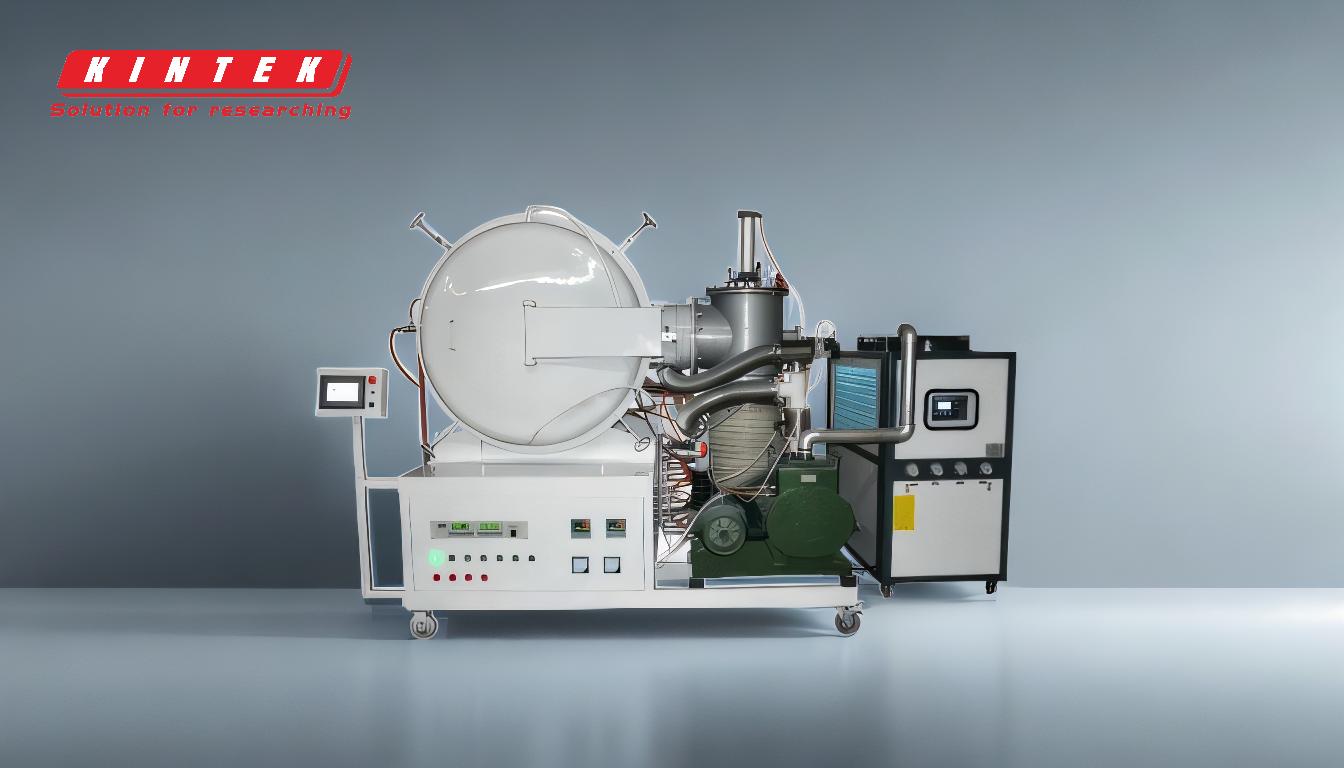
-
Stages of Annealing:
- Recovery: This is the first stage where the metal is heated to a temperature that relieves internal stresses without changing the grain structure. This stage helps in reducing the hardness of the metal slightly.
- Recrystallization: During this stage, the metal is heated above its recrystallization temperature but below its melting point. New grains start to form in the metal, replacing the deformed grains. This stage significantly reduces the hardness and increases the ductility of the metal.
- Grain Growth: If the metal is held at the recrystallization temperature for too long, the grains will continue to grow. Larger grains can decrease the strength of the metal, so this stage must be carefully controlled.
-
Factors Influencing Annealing Time:
- Type of Metal: Different metals have different annealing temperatures and times. For example, steel might require a higher temperature and longer time compared to copper.
- Thickness of the Material: Thicker materials generally require longer annealing times to ensure that the heat penetrates uniformly throughout the material.
- Desired Properties: The specific mechanical properties desired in the final product can also influence the annealing time. For instance, if a very soft and ductile metal is required, the annealing process might be extended.
-
Typical Annealing Times:
- For most metals, the annealing process can take anywhere from a few hours to a full day. The exact time depends on the factors mentioned above. For example, annealing steel might take about 1-2 hours per inch of thickness at the appropriate temperature.
-
Use of Nitrogen Gas Mixtures:
- To prevent oxidation and other chemical reactions during the annealing process, an inert atmosphere is often used. Nitrogen gas mixtures are commonly employed for this purpose, especially when annealing metals that are prone to oxidation at high temperatures.
Understanding these aspects of the annealing process helps in determining the appropriate duration and conditions needed for effective annealing of different metals, ensuring the desired mechanical properties are achieved.
Summary Table:
Factor | Impact on Annealing Time |
---|---|
Type of Metal | Different metals (e.g., steel, copper) require varying temperatures and durations. |
Thickness of Material | Thicker materials need longer annealing times for uniform heat penetration. |
Desired Properties | Softer, more ductile metals may require extended annealing times. |
Typical Duration | Ranges from a few hours to a full day (e.g., 1-2 hours per inch for steel). |
Inert Atmosphere | Nitrogen gas mixtures prevent oxidation, especially for oxidation-prone metals. |
Need help optimizing your annealing process? Contact our experts today for tailored solutions!